Morris & Perry boost output with Sandvik DI550
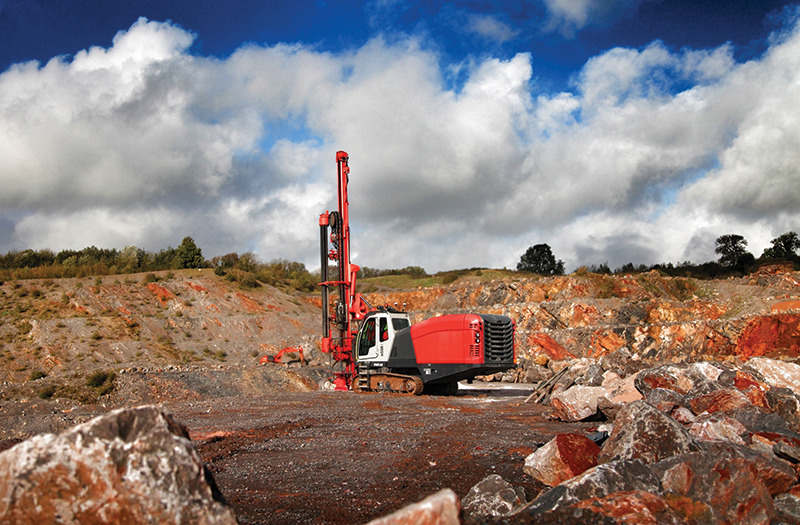
First published in the March 2014 issue of Quarry Management
Based in Somerset, family owned Morris & Perry, suppliers of aggregates, asphalt and ready-mixed concrete across the south-west of England, have set their sights on increased production with the purchase of a new Sandvik DI550 drill rig. The acquisition marks the latest stage in a partnership between Morris & Perry and Sandvik that stretches back many years.
The new Sandvik rig will be used to spearhead the latest phase in the development of Morris & Perry’s Gurney Slade Quarry in the Mendip Hills. ‘We needed a drill rig that was faster and more productive to allow us to blast more quickly and efficiently,’ said assistant quarry manager Elliot Light.
The 24-tonne Sandvik DI550 down-the-hole rig has made an immediate impact on efficiency at the site; the machine’s 24.4m3 capacity at 24 bar compressor pressure and 5in hammer make it highly productive. ‘With our old rig, it would take a full working day to drill for a blast,’ explained Mr Light. ‘The Sandvik DI550 has reduced that to just a few hours, drilling up to 300m in a single shift. Even the tracking is faster on the new machine, meaning we can get it on station and working far more quickly.’
According to Mr Light, this additional efficiency has not come at the cost of increased fuel consumption. In fact, Morris & Perry say they have recorded a ‘notable reduction’ in fuel consumption since the arrival of the new rig. This reduction has been achieved thanks to the unit’s Tier 3-compliant Caterpillar C13 diesel engine, which delivers 328kW at 1,800 rev/min, as well as a variety of advanced controls including automatic flow and pressure control and engine rev/min optimization during different phases of operation.
A key consideration for Morris & Perry was the safety and efficiency of drill rig operator Jason Caley, who, although an experienced operator, described the DI550 as a ‘step up’ from the machines he is used to. ‘It was quite daunting when the machine first arrived. It seems very sophisticated and complex but it is actually very straightforward,’ he said. ‘The training from Sandvik really put my mind at ease. In truth, the automation systems take care of most machine functions so I can concentrate on drilling.’
Elliot Light added: ‘In our experience, an operator who is safe and comfortable is far more productive. The working environment within the Sandvik DI550 is superb and I know that Jason loves the heated seat. And, when he does have to leave the cab to carry out daily maintenance duties, all service points are readily to hand and easily accessible. A lot of thought has gone into the design of this machine.’
Although it is still relatively early days in the working life of Morris & Perry’s new Sandvik DI550 rig, the company does not have any regrets about its purchasing decision. ‘The overall package from Sandvik has been very good,’ said Mr Light. ‘They helped us through the selection process, worked with us when the machine was delivered, gave the operator all the training required to make him safe and productive, and they have been on hand with advice and support ever since. It’s a brand we trust and I would definitely buy from Sandvik again.’
Sandvik DX800 drills deeper into the forest
Meanwhile, north of the border the UK’s primary timber producer – the Forestry Commission – is using a 15-tonne Sandvik DX800 drill rig to win valuable road-building rock in areas inaccessible to most other drill rigs.
Galloway Forest is Europe’s largest man-made forest, covering an area of almost 800km2 in south-west Scotland. Established in 1947, the forest is a key provider of valuable timber for use in UK mills, and as its trees mature new roads are required to carry timber trucks deeper into the forest. Fortunately, in addition to its extensive timber reserves, the forest also has huge reserves of granite and greywacke that are ideal for road-building applications, and which do not have to be imported from outside the confines of the forest. But while this rock is plentiful, it is also difficult to reach.
‘At first glance, the terrain looks quite smooth and gently undulating,’ said quarry manager Norrie Russell. ‘But when you strip away the overburden, the rock beneath is craggy, the gradients are steep, and there’s no clear pathway for people, let alone machines.
‘This is less of a quarry and more a rock formation, and we are required to drill and blast rock as we find it. We don’t have the luxury of well-maintained haul roads and managed gradients like traditional quarries. Every day is a new challenge. We have to manoeuvre over rocky outcrops and up and down seemingly impossible grades to drill and blast in order to create new access roads for the timber trucks. We are pioneering, and our DX800 is required to go where no other machine can go.’
Despite these geological and topographical challenges, the Forestry Commission still manages to run an effective drilling, blasting and quarrying operation, a fact that Mr Russell believes is due largely to the recent purchase of the Commission’s second DX800 drill rig. ‘Quite simply, the DX800 can access areas that no other machine of this type could reach,’ he said. ‘The independently oscillating tracks and the ability to tilt both the cab and the mast back and forth makes the machine incredibly manoeuvrable and stable on even the most difficult and arduous terrain. Having looked at a number of different machines prior to purchasing our second Sandvik, I honestly believe that no other drill rig could work like the DX800.’
This view shared by rig operator Walter Handley, who cited the DX800’s slewing upper-structure as another key benefit. ‘On terrain as difficult as this, it is important to keep tracking to an absolute minimum to avoid loosening the ground beneath,’ he said. ‘With the DX800’s 180° slew capability, I can drill five bores while keeping the tracks in a fixed position. It’s safer and far more productive on terrain like this.’
According to Norrie Russell, the Sandvik DX800 regularly drills more than 200m of 102mm boreholes in an 8h working shift, despite the challenging terrain and variations in required drill depths. ‘Some of the bores at the front of the area to be blasted will be relatively shallow, maybe as little as 2.5–3.0m in depth,’ he said. ‘But the bores towards the back of the blast area will go down 7m or more with a 3m spacing between. We tend to blast weekly and each blast will drop 5,000 tonnes of rock. That rock is passed through a jaw crusher to reduce it to –65mm, and then through a cone crusher to produce sufficient fines for road-building applications.’
As an existing Sandvik customer, Mr Russell said the company’s after-sales support capability was another factor in the Forestry Commission’s purchasing decision. ‘We buy all our drill bits and rods from Sandvik. They are generally available with a 24h turnaround and we have found them to be extremely hard-wearing and durable,’ he commented. ‘When you’re working in a location as remote as this, it is nice to know that a reliable source of parts and support is just a phone call away.’
Above all, however, Mr Russell points to the machine’s mobility and manoeuvrability in difficult terrain, and the comfort it affords the operator, as the features that make it stand out from the rest. ‘There is not another machine on the market that could go where our Sandvik goes or do what our Sandvik does,’ he said. ‘We firmly believe that a comfortable operator is a productive operator, and in the DX800 our operator is well protected from noise, dust, vibration and the weather.’
Operator Walter Handley agreed. ‘I love this drill rig,’ he enthused. ‘Compared to competitive machines, the Sandvik DX800 is truly first class. No other machine can match it.’
For further information visit: www.construction.sandvik.com
- Subscribe to Quarry Management, the monthly journal for the mineral products industry, to read articles before they appear on Agg-Net