Glensanda Quarry Update
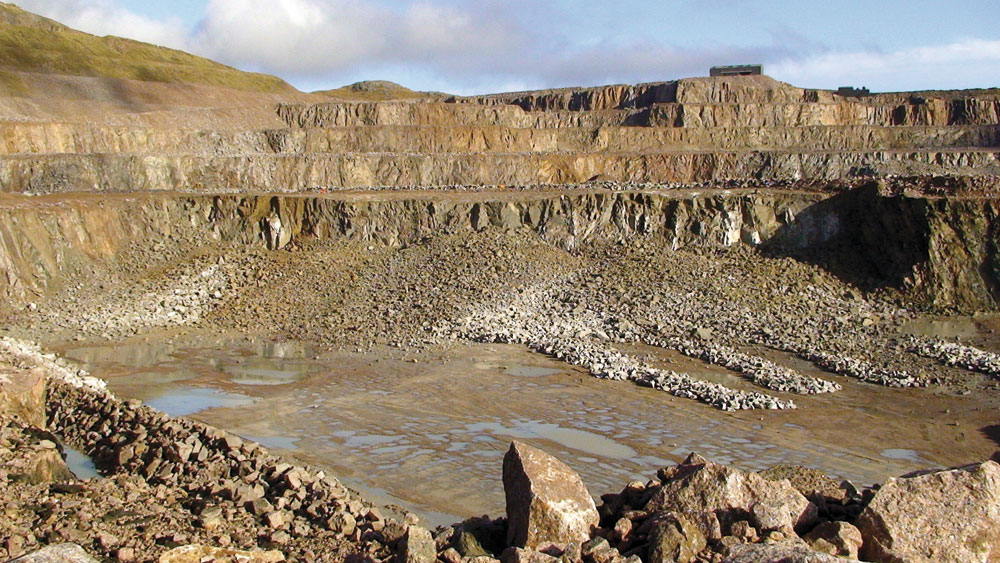
Ian Christie, drilling and blasting manager with BAM Ritchies, and David Gibson, business development manager with BAM Ritchies, outline the latest developments in drilling and blasting at the UK’s largest quarry
Glensanda Quarry, operated by Aggregate Industries, is the largest granite quarry in Europe and the largest quarry in the UK. In 2008 Quarry Management featured changes to the drilling and blasting operations at the site, and now, some four years on, an update is timely.
Before 2008, the site traditionally used in-house drilling with shotfiring operations carried out by Orica from an on-site bulk emulsion manufacturing plant. Drilling operations were carried out by two site-operated Ingersoll Rand DM-45E rigs drilling 168mm diameter holes, together with four ECM 350 pneumatic rigs that were used for production and development blasting. A total of nine staff were employed, producing approximately 6 million tonnes per year.
Today the quarry produces 7.5 million tonnes of blasted rock per year (approximately 150,000 tonnes per week), all of which must be suitable for loading by Caterpillar 992 loading shovels. This represents a drilling requirement of around 3,000m per week or 150,000m per year.
Since 2008, BAM Ritchies have been providing the drilling and blasting service in the quarry, producing about 7 million tonnes per annum, after Aggregate Industries sought the provision of a best-value, innovative service using the latest drilling and blasting techniques.
Since starting, a number of notable changes have been introduced with far-reaching benefits, including increased production, reduced costs and a significantly reduced carbon footprint, brought about by fuel-efficient drill rigs and higher unit production outputs.
In addition, the use of modern rigs and methods, based upon industry-leading risk assessments and procedures, is helping the company’s commitment to eliminate incidents and accidents. The new developments and techniques cover all elements of the drilling and blasting operations.
Surveying and face profiling
Surveying and face profiling is carried out using MDL’s Quarryman Pro with Quarry.4 from Co-Ordinated Survey Systems. Low cloud and heavy snow are common at the site, with heavy cloud sometimes lasting for days. This can have a massive impact on profiling as a typical scan can take up to 45min to complete due to the size of the faces being fired.
However, future improvements in technology and software will make this a much quicker and efficient process through the use of the fast-scan feature on the latest Quarryman Pro combined with developments in the survey software. These developments will allow profiles to be carried out in less than 10min, thereby significantly reducing time lost waiting for the cloud to lift.
Drilling
All of the drilling equipment previously used on site has been decommissioned and replaced. The primary resource now comprises two Atlas Copco L7 drill rigs, both fitted with the COPROD system, Glensanda being the only site in the UK to operate the COPROD system on L7 rigs drilling with a 102mm drill string. Both rigs are fitted with the COP 4050-series rock drill that provides 48kW of energy at a frequency of 50Hz through the COPROD drill string, which comprises an outer guide tube and inner drill steel that carries the drill’s energy to the 127mm bit.
With the COPROD system the L7 is approximately 30% more fuel efficient in a drilling shift compared with a standard down-the-hole (DTH) machine of similar size. Having an average penetration rate in excess of 1.0m per minute, the L7 has nearly twice the penetration rate of the DTH machines, making the fuel economy per metre even greater.
Each L7 is capable of drilling 350m in a normal shift drilling regulated benches on a varying staggered pattern, depending on the local geology of the quarry. It is necessary to present the blasted muckpile in a specific profile allow it to be easily and safely worked by the loading shovels, and to ensure that the material ravels freely as it is dug.
The site also operates an Atlas Copco remote-control D9 rig fitted with a top-hammer. BAM Ritchies own and operate the largest fleet of this kind of rig in the UK. The D9 is used for both production and development blasting, and has the ability to drill in some of the most inaccessible areas of the quarry with little difficulty. The operator is able always to safely operate the rig using the remote-control unit, while the rig itself can be safely anchored using its own built-in winch.
More recently a Sandvik DP1100i has been introduced to the site, bringing further benefits. These include: easy adjustment of all parameter settings from the cabin; several factory-preset drilling parameters for different rock conditions; operator tuning and storage of optimal parameters for each drilling location; and an easy return to the pre-settings for drill bit rev/min, penetration rates and hole depth.
Other benefits include: excellent torque control for good rotation and good rock contact, self-adjustment of power level according to penetration rates, feed, percussion follow-up for maximum penetration rates, and selectable auto-collaring. In addition, highly productive operation is available from day one as a result of simulator-based operator training.
This state-of-the-art drill rig has other benefits such as low fuel consumption that produces 90 tonnes less CO2 at 6,700 engine hours than the previous similar rigs. Not only does this reduce the effect on climate change, it also reduces costs to the contractor, client and end customer.
Safety is a crucial consideration and the latest generation of rigs have FOPS/ROPS certified cabins that are: pressurized to exclude dust; offer clear visibility for the operator; provide efficient filtration for incoming and recirculating air; and feature air-conditioning, cabin suspension to eliminate vibrations and an opening safety grille for window cleaning.
Other benefits include high-frequency stabilizer rock bits, large fuel tanks and wide, powerful tracks.
A comprehensive web-based reporting system records site data including production, hours, fuel consumption, condition and rig location, while service- requirement forecasting ensures that the company’s rigs are maintained in productive condition to ensure client satisfaction.
Blasting
The site has its own bulk-emulsion manufacturing plant which is supplied and operated by Orica, who use an all-terrain bulk truck to deliver the product to the blast site. The current requirement is approximately 1,500 tonnes of bulk emulsion per year.
The site was one of the first in the UK to introduce electronic initiation as the sole means of initiating explosives. While this means of initiation is up to four times more expensive, the benefits in terms of blast ratio, fragmentation, pattern and control of throw offer a much larger payback for both the contractor and the client.
The key to ongoing success is ensuring that sufficient development work is carried out in line with normal production, much of which will only be accessible by the variable fleet of specialist rigs. These areas must now be blasted and opened up to allow production drilling and the future development of the quarry to take place. In the coming years it will be necessary to blast the rock that surrounds Glensanda’s glory hole, while a second shaft is being constructed.
Investigation of ground vibration during blasting will be used to ensure minimal disruption to the glory hole and that no oversize material which could potentially cause a blockage is allowed to fall back into the shaft.
Benefits
All of the drilling and blasting work now carried out at Glensanda Quarry is done by just seven personnel. Jim MacDougall, BAM Ritchies quarry engineer, commented: ‘With a continually changing and increasingly demanding production environment, it is essential that the drill and blast operations adapt to the needs of the quarry. Staying ahead with advances in technology and improvements within the industry is key to the operation’s success.’