Digitization in the Quarry
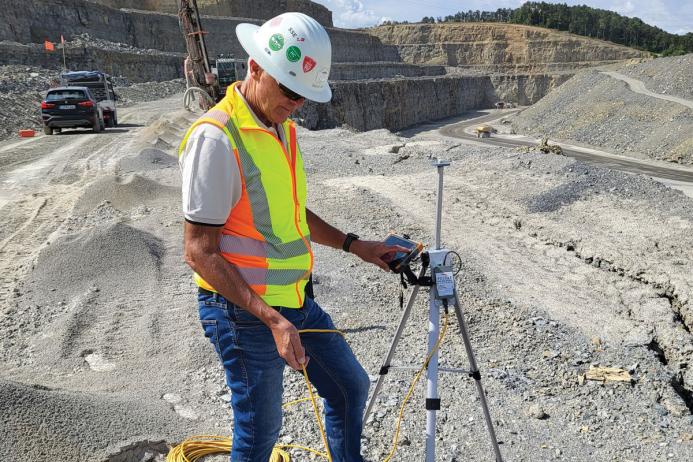
First published in the April 2024 issue of Quarry Management
Combining safety and efficiency
When it comes to blasting, there is one aspect that stands above all others – safety. The key to success for blasting in quarries and mines is to combine safety with optimum of economic efficiency. Working with the highest possible precision during planning, drilling, and blasting is, therefore, indispensable. How can these requirements be optimally integrated into the daily workflow? Digitalization is opening up new possibilities in this area and the solutions already available are more advanced than you might imagine.
Johannes Kutschera knows all these requirements of the blasting industry inside out. He works for geo-konzept GmbH, who offer hardware and software for the design, optimization, and documentation of large borehole blasting and are one of the global market leaders in this field. As head of the company’s mining department, Mr Kutschera has been involved in digital development for more than 15 years and knows the real pain points of the industry – and the possibilities that arise from the use of digital solutions.
‘We cover the entire drilling and blasting workflow,’ he said. ‘It starts with measuring and scanning the rock face, which can sometimes also be carried out by drone. Based on the 3D data obtained, the drilling pattern is digitally planned in an optimized way and then transferred to a GNSS-supported drill rig. The boreholes are precisely measured using a probe in order to adjust the parameters, and these data are also incorporated into the process.’
According to Mr Kutschera, the use of explosives and blast planning can thus be made not only more efficient, but also safer at the same time. Efficiency and safety are the cornerstones of any extraction blasting, which above all requires drilling with maximum precision.
The 3D borehole navigation system RiGuide not only eliminates the need to manually mark and stake out the drill pattern, but also the errors that could be associated with this. The hole collar positions transferred from the computer are precisely controlled via GNSS and the drilling direction, angle, and depth are accurately implemented. Thus, even complex drill patterns with different drilling directions and angles are no longer a problem. By avoiding holes that are too short or too long, vibrations are reduced, subdrill is minimized, and subsequent costs are avoided. As no bearing points are required with RiGuide, the drill rig can be used in all weather and light conditions. Documentation of the entire drilling process and the precise allocation of drill dust samples is easy to implement, as these are not only stored in the system software but can also be viewed and retrieved by everyone involved, at any time, when using the associated cloud solution.
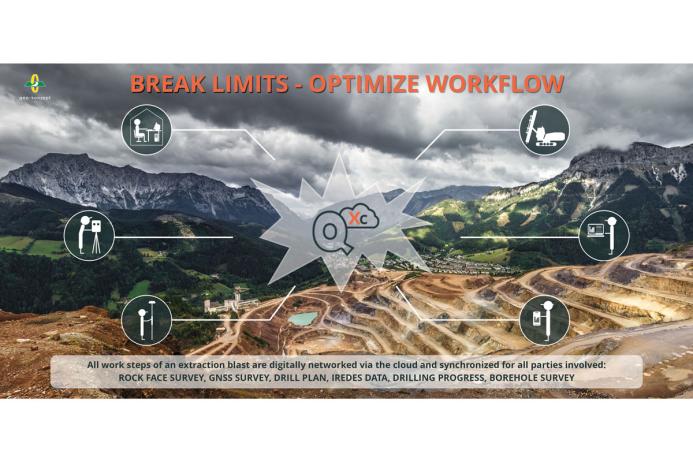
Data highway quarry
By using digital solutions, the user collects all relevant drilling and blasting data in a database, which allows structured and seamless evaluation and documentation. A main player for a reliable data flow is geo-konzept’s cloud solution, QuarryX Connect.
‘This software solution is designed to connect all those involved in the drilling and blasting process,’ said Mr Kutschera. ‘There is a smooth digital data exchange; any information that is collected for a blasting project is always available to all those involved, both in the operational and management teams. This naturally supports the flow of information considerably.’
This is particularly practical for quarries that work with external service providers. Such a division of work can also be mapped digitally with the cloud solution, whereby the user structure can be set hierarchically: the blaster sees his own projects, the operations manager only sees projects in his quarry, the regional manager sees the projects of all quarries in his area, while the chief executive officer has an overview of all projects.
In addition to this networking of people, the networking of machines is, another of the major advantages. Oliver Weigel, a product specialist at geo-konzept, has more than 30 years’ experience in the quarry and appreciates these benefits.
‘The best thing is that you save a lot of travel time and manual work steps,’ he explained. ‘For example, the drill pattern can be sent directly to the drill rig or – if there is no digital borehole navigation – directly to the app. The drilling progress can be tracked virtually in real time after each hole, which facilitates further planning such as ordering explosives or moving the drill rig.’
The overview and analysis options are also optimized with QuarryX Connect: from the evaluation of key performance indicators (KPIs) in the web app, to the utilization and performance of the drilling machines, to the overview of all costs incurred, those involved always have everything in view.
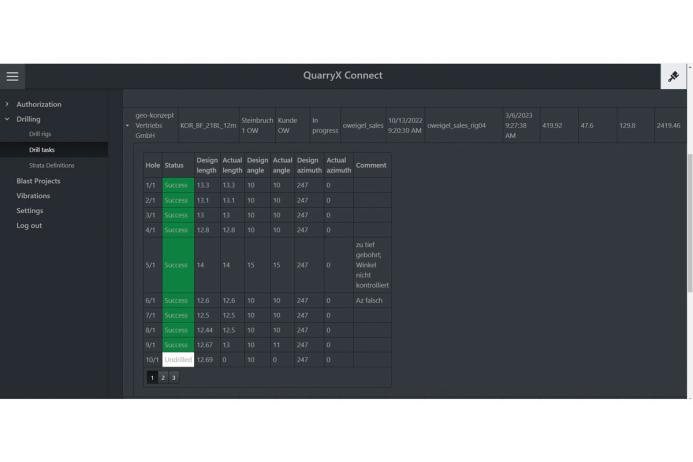
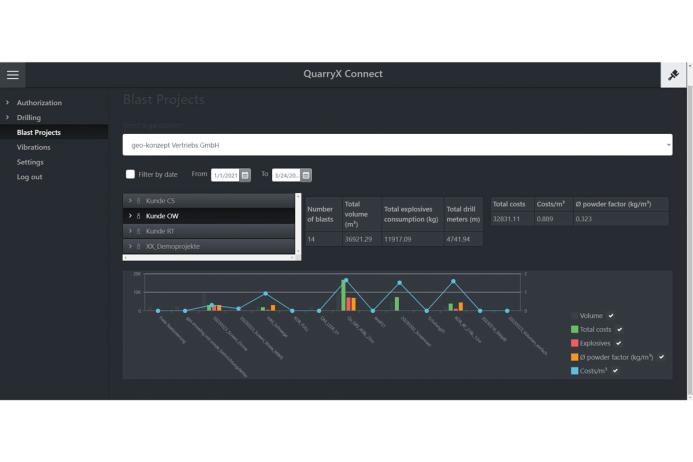
Digitization in a modular system
Cost-effectiveness not only means carrying out efficient blasting, but also using your investment wisely and making it work for you. According to Johannes Kutschera, this is not only possible for large quarries, but also for small ones too.
‘Every quarry that carries out blasting works will benefit from these solutions in several areas,’ he said. ‘The increase in efficiency naturally has a greater impact on larger quarries than on smaller ones, but at least as important is the safety aspect, which has to be taken into account for each individual blast. Reducing fly-rock, for example, is an issue for every quarry, which is why this technology is an absolute must for all quarries.
‘The overall solution is based on a modular concept that covers the entire workflow of drilling and blasting with different systems. You can also start with a small system and grow with the tasks,’ explained Mr Kutschera. ‘Every investment made in a geo-konzept product today is future-proof, because this modularity means that the systems can always be expanded as required.’
At geo-konzept, a team of experts not only takes care of the development and optimization of the systems, but also deals with customer concerns and support requests. ‘We constantly receive very positive feedback regarding the quality of our support and the team’s high level of expertise. All of our sales representatives have many years of experience in the field of drilling and blasting, as shotfirers, drillers, production managers, and blasting engineers, so they really know what they are talking about.’
High-tech you can touch
As long-standing experts in the field, geo-konzept also regularly attend the most important trade fairs and conferences and seek contact with customers and users with their own annual training courses and workshops. ‘We always look forward to events where we can showcase all our individual products, from scanners to borehole probes and GNSS surveying, to drones and all related software,’ said Mr Kutschera, ‘but direct contact and exchange with long-standing users of our systems and software is also important to us, as we can not only show innovations and explain updates, but also receive valuable feedback that often has an influence on further development. Digitalization in quarries is nothing new for us; we have been involved in it since we started working in the field of drilling and blasting more than 15 years ago. In this respect, it is an incentive for us to highlight digitalization in the quarry and make it accessible to everyone – from the smallest quarry to the largest corporation.’
Subscribe to Quarry Management, the monthly journal for the mineral products industry, to read articles before they appear on Agg-Net.com