Better Blasting
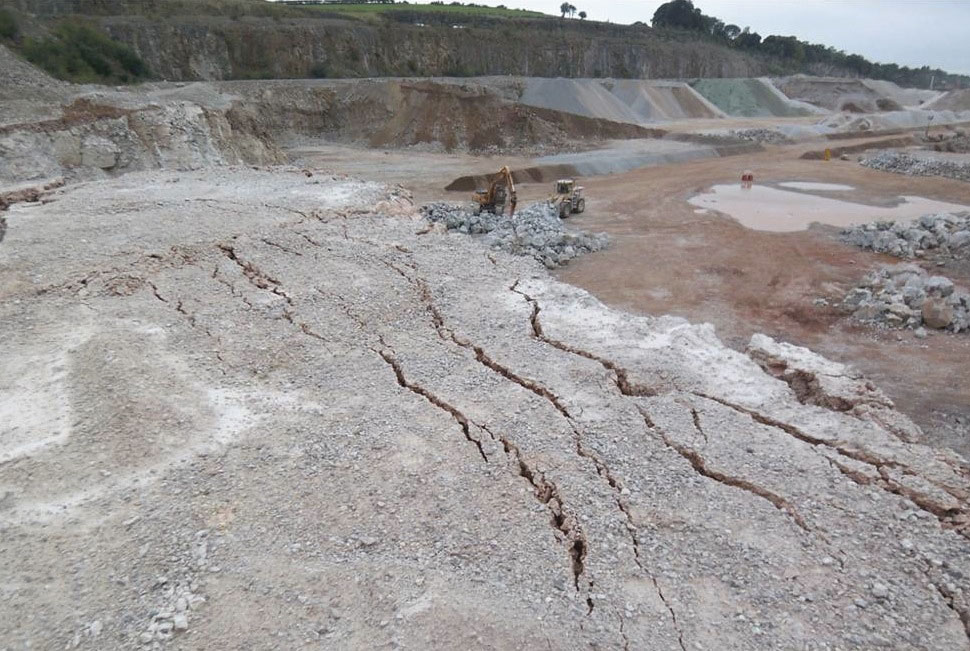
Efficient blasting to improve the geotechnical stability of quarry faces
By Ian Thomas, geotechnical manager, Aggregate Industries
Generally, blasting has four main objectives: to loosen the in-situ rock from a quarry face; to reduce the block size to allow it to be processed by crushers; to ensure the blast pile is easy to excavate and load; and to leave a stable face afterwards. Efficient blasting also reduces fines and oversize and has a holistic, mine-to-mill approach where the fragmentation of the blast pile is designed to match the loading equipment and crushers. The cheapest rock breakage is done using explosives in the correct quantities at the correct locations. This requires the geological conditions to be known, a stable rock face with minimal blast damage and consistency of blasting parameters. Once achieved by using a fragmentation model such as the Kuz-Ram and its derivatives, it is possible to predict fragmentation rather than leaving it to chance, and this improves production planning.
The current situation in blast engineering is neatly summarised by the modern father of rock engineering, Evert Hoek (1999): ‘…a handful of highly skilled and dedicated researchers, frequently working in association with explosives manufacturers, have developed techniques for producing optimum fragmentation and minimizing damage in blasts. At the other end of the spectrum are miners who have learned their blasting skills by traditional apprenticeship methods, and who are either not familiar with the specialist blasting control techniques or are not convinced that the results obtained from the use of these techniques justify the effort and expense. At fault in this system are owners and managers, who are more concerned with cost than with safety and design, or planning engineers who see both sides but are not prepared to get involved because they view blasting as a black art with the added threat of severe legal penalties for errors. The need to change the present system is not widely recognized because the impact of blasting damage upon the stability of structures in rock is not widely recognized or understood’.
While this was aimed as a criticism of mining engineers, it equally applies to the management of many UK and European aggregate quarries. As an industry, quarrying has been preoccupied by other issues, such as health and safety, environmental, and planning concerns. In addition, many of the experienced managers and engineers have retired or left the industry and the younger generation are less questioning about what they perceive as established blasting practices. Today, more powerful explosives are used in the same unscientific way that was prevalent in the 1970s, and local and senior management tend to focus on primary blasting costs. Drilling fewer holes may be cheaper, but is not usually best for either geotechnical stability or total production cost reductions. The firing of shots with more than two rows should also be closely monitored; it may be cheaper and require less manpower, but the consequential damage to the rock face can be extreme. The geotechnical specialists usually give optimum and maximum face heights but a four row blast can result in a blast pile higher than the face, which can be problematic for the excavator operator.
The author’s research indicates that general blasting practices, in relation to designing blasts with the underlying geology in mind, have not progressed in the past 20 years and UK quarries are lagging behind other countries and industries. Blast designers often do not know the properties of the explosives they use (VOD, gas volume produced etc) and therefore sometimes use the wrong explosives for the geological conditions encountered. In some cases shothole sizes are too large for pumped bulk explosives and the only option is to charge or stem, which cannot be the most efficient method of blasting.
The main problem, however, is shothole geometry, which is often inconsistent and does not follow published guidance; in particular, the main culprit is the spacing-to-burden ratio, which should be no less than 1 and up to 1.4, depending on rock strength. Most rock breakage is caused by the reflection of the compressive shockwaves, thereby breaking the rock in tension. If the burdens are too great the shock waves have to travel too far and attenuate before optimum breakage can occur. If the spacing is too small the effective free face, which is often not the face itself in a multi-row blast, does not allow the blast pile to be effectively displaced. This, in turn, can cause excessive back break (fig. 1) and ‘tight’ blast piles which increase face dangers and slow down loading.
The Health and Safety Executive (HSE) has rightly highlighted the lack of geological input into blast designs and realizes that, in many cases, the design cannot be correlated to any of the geotechnical or geological features in the quarry. The case is even more complicated in reality; when considering the material that requires blasting, designers should consider the rock mass rather than just the rock itself. Terzaghi (1946) was one of the first to point out that knowledge of the ‘type and intensity of the rock defects (discontinuities) will be much more important than the type of rock which will be encountered’. A discontinuity is defined by Edelbro (2004) as a ‘significant mechanical fracture that has low shear strength, negligible tensile strength, and high fluid conductivity compared with the rest of the rock material’.
Rock mass is rarely continuous, homogenous or isotropic, and is usually composed of intact blocks of rock separated by discontinuities such as faults, cleavages, fissures, fractures, joints, bedding planes, shear zones etc. The behaviour of the rock mass is, therefore, dependant on the nature and frequency of these discontinuities, the shape of the intact rock defined by the discontinuities and the properties of the intact rock. From a geotechnical engineering point of view, in most cases it is the discontinuities that control the engineering performance of a rock mass and not the intact rock material. Therefore, the more angular shaped the rock pieces are, with clean, rough discontinuity surfaces, the stronger the rock mass will be. The behaviour of a rock mass is also influenced by the external conditions it is subjected to, generally the in-situ stress state and groundwater, although these issues are not too important when considering blasting. Hoek and Karzulovic (2000) studied the effects of blasting on discontinuities and presented the results as shown in figure 2.
If the figures are studied it can be seen that the blast-induced damaged area can extend to twice the face height and is thought to be the main reason why pre-split blasting fails if this is undertaken too close to an existing face. Often this damage is seen in extreme cases as ‘back break’ and can usually be avoided by re-orientating the faces, altering the design and, in particular, altering the timings.
If figures 2 and 3 are compared it can be seen that there are similarities. Figure 3 is a blast-damaged face excavated with a 360° excavator where the digging was halted when it became harder. This situation takes many blasts to rectify, mainly because the subsequent hole may have a large burden and little explosive in the upper regions and the damage can extend many metres back into the face.
In order to improve blasting, it is necessary to go back to basics and concentrate on the blasting parameters used. The Government, in its report ‘Reclamation of limestone quarries by landform simulation’, by Cripps et al., (1999), has calculated that only 15% of the energy from the blast is utilized in breaking the rock and just 4% in displacing it; the rest is effectively wasted as noise, vibration and fines production. Thus, only a small decrease in the blast ratio will only produce more unwanted vibration.
Figure 4 shows how a sedimentary rock with closely spaced joints can appear in a blast pile. Close examination shows iron staining on the joints and indicates that there is very little breakage of the rock, it has only been displaced. This indicates how accurately the explosives should be used; too much only increases fines because once there is sufficient explosives to break the rock the rest of the energy is wasted.
It is easy to reduce blasting costs by using fewer explosives, but the challenge is to use the optimum amount of explosives to produce effective fragmentation for the crushing plant. One simple method to predict blast fragmentation from the drilling and explosives used is to use the Kuz-Ram blasting model, or its updated derivatives, which has been around since the early 1980s. It has never been fully taken up by the quarrying industry but is widely used by the larger mining companies. An additional benefit of blasting efficiently is the reduction in power required to crush rock. There has been a major drive in the extractives industry to reduce power consumption and improve efficiency for the whole of the quarry operation. The EU-funded research project ‘Less fines in aggregate and industrial minerals industry’ has been working since 2000, and in the UK sustainability research has been funded by the Minerals Industry Sustainable Technology (MIST) research programme, which lasted until 2006. From the latter research came the paper by Lowndes and Jeffrey (2007), which has highlighted to the industry the importance of a holistic mine-to-mill approach to optimize the production of primary aggregates. They stated that the project aimed to ‘utilize a combined blast fragmentation and comminution optimization to maximize desired product and minimize fines and energy consumption’.
One of the modifications the author of this article has made to the Kuz-Ram model, as shown in figure 5, is to include an efficiency factor and to relate the rock factors to the geological strength index (GSI). The GSI is a system for estimating the reduction in rock mass strength for different geological conditions, and tables can be found in Rock Slope Engineering (2001) by Wyllie and Mah. The GSI indicates the frequency of the joints and their surface conditions, which dictate the breakage that will be achieved.
The efficiency factors include the burden-to-spacing ratio, optimum stemming lengths, timings, row patterns and number of rows. For instance, the fragmentation for a well designed staggered row with correct digital timings (following testing and evaluation) can be up to 30%. The measurement of fragmentation has always been difficult to achieve. Ultimately, the author used the power consumption from the primary crusher. Bond’s theory of comminution, developed in 1952, shows that the energy requirement to reduce fragments reduces as the feed size reduces. Thus, fragmentation can be estimated over a period of months (to take out variances in moisture, ambient temperature and crusher maintenance). A more accurate method used since the original study is to digitally scan blast piles using a LiDAR (light-detection and ranging) laser scanner (fig. 6).
The block size distribution in the blast pile was analysed by Adrian Wilkinson of Quarry Design Ltd using SplitFX software, which triangulates LiDAR point clouds and then creates polygons around groups of triangles within a user-defined similar orientation. A series of ‘polygons’ was produced upon a scan of just the blast pile, with the area of each polygon being exported as a CSV file into Excel, allowing the average polygon area to be determined. Based upon the polygon size (being one side of a roughly cubic block), the block volumes were calculated.
In conclusion, by using explosives efficiently, instabilities in quarry faces can be reduced. The more stable a face is the more it allows fragmentation to be consistent and eventually to be predicted using models such as the Kuz-Ram. Blasting costs, along with wear and downstream power consumption in the plant, is reduced while production increases.
This paper won the 2011 Marston Award – an annual prize for the best paper presented to an Institute of Quarrying branch meeting by a member, of any grade, employed within the quarrying industry. The paper stems from an MSc project entitled ‘An investigation to determine if an updated, geologically based Kuz-Ram blasting model can reduce blast ratios while maintaining blast-pile fragmentation’.
Bibliography
- BOND, F.C.: ‘The third theory of comminution’, Transactions of the American Institute of Mechanical Engineers, 1952, vol. 193, pp. 484-494.
- CRIPPS, J.C., CZEREWKO, M.A., JOHNSON, D., and T. WILTON: ‘Reclamation of limestone quarries by landform simulation’, BRADLEY, P., and P. BRASHAW (Eds), Office of the Deputy Prime Minister (ODPM) now transferred to the Department for Communities and Local Government (DCLG), 1999.
- EDELBRO, C.: ‘Evaluation of rock mass strength criteria’, Technical Report, 2004, Luleå University of Technology, ISSN:1402-1757.
- HOEK, E.: ‘Putting numbers to geology – an engineer’s viewpoint’, Quarterly Journal of Engineering Geology, 1999, 32, pp. 1-19.
- HOEK, E., and A. KARZULOVIC: ‘Rock mass properties for surface mines’, in: Slope Stability in Surface Mining, HUSTRALID, W.A., McCARTER, M.K. and D.JA. VAN ZYL (Eds), Society for Mining, Metallurgical and Exploration, 2000, pp. 59-70.
- LOWNDES, I.S., and K. JEFFREY: ‘Sustainable provision of aggregates: Optimizing the efficiency of primary aggregate production’, 2007, DEFRA, Aggregates Levy Sustainability Fund.
- TERZAGHI, K.: ‘Rock defects and loads on tunnel supports’, in: Rock Tunnelling with Steel Supports, PROCTOR, R.V., and T. WHITE (Eds), pub. by Commercial Shearing and Stamping Co., 1946, pp. 15-99.
- WYLLIE, D.C., and C.W. MAH: Rock Slope Engineering, 4th edition, 2007, Spon Press, ISBN 0-415 28001-X.