A Hard Rock to Crack
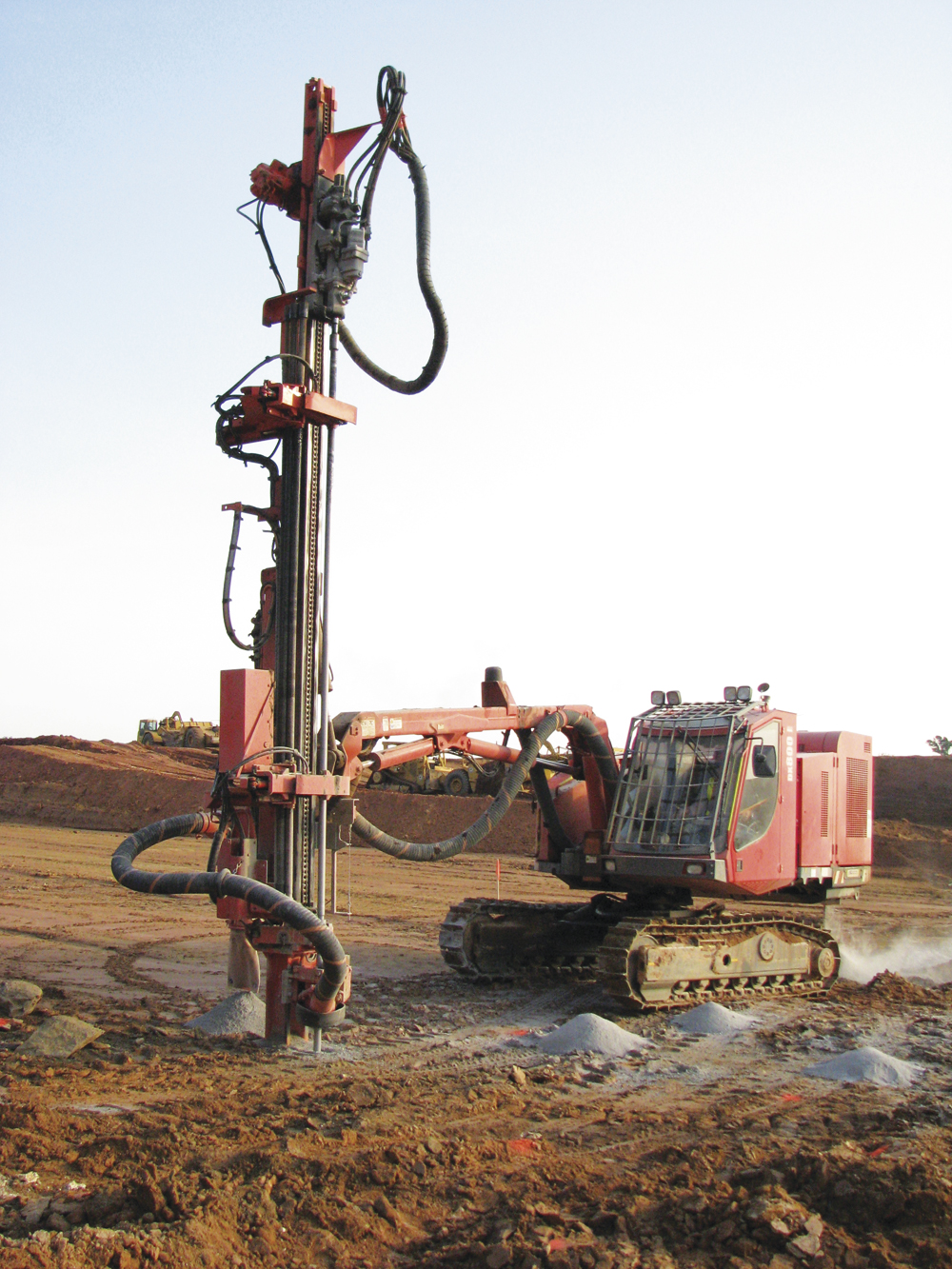
Sandvik DX800 meets Plateau Excavation’s drilling needs on US intermodal airport development
Located within the boundaries of Charlotte Douglas International Airport (CDIA), in the US, lies a granite formation that is set squarely in the path of development work for the new Norfolk Southern Intermodal site. It is here that Plateau Excavation of Austell, Georgia, are constructing the US$92 million intermodal project, and playing a key role in this work are three Sandvik DX800 top-hammer hydraulic drills that are proving themselves day after day, no matter what the conditions.
The Norfolk Southern Intermodal project encompasses nearly 81ha of land, with the granite rock formation lying within just a few hundred feet of a very active runway, of a very busy airport. The 81ha area will be turned into an ‘intermodal yard’, meaning that cargo carried there on Norfolk Southern railroad cars will be off-loaded for further transport on tractor-trailers and vice versa. It is estimated that more than 200,000 cargo containers will be transferred in the yard each year, replacing a smaller operation in Charlotte.
Playing a key part in the project are Plateau Excavation, who, over the past three decades, have grown into a major site infrastructure contractor, with their area of work comprising the entire south-eastern region of the US – the intermodal rail yards in Charlotte being the latest, and one of the most prestigious, of numerous site-preparation projects the company has successfully completed since 1983. On this particular project, which began in early May 2012, Plateau are acting as subcontractor to Illinois-based construction and management firm, Milord Company.
In order to deliver their part of the project, Plateau Excavation are utilizing more than 50 items of heavy equipment on the scheme, including three Sandvik DX800 hydraulic drills that are used to bore directly into the granite shelf. The drills themselves are owned and operated by Plateau Excavation subcontractors LK Gregory Construction Inc, who are headquartered in Crossville, Tennessee. The DX800s were supplied and are serviced by the Buford, Georgia, dealership of Charlotte-based ASC Construction Equipment USA Inc.
The Sandvik drill rigs are a new product line for ASC, who are primarily known as the largest Volvo dealership in the world. Until January 2012 Sandvik distributed their machines directly in this region, but following the company’s customer-focused reorganization ASC were appointed as Sandvik Construction’s distributor for the area. When LK Gregory expressed interest in procuring two more DX800s (they already owned a 2007 machine), ASC’s Buford dealership were able to supply the 16-tonne tracked machines in order to help Plateau Excavation with their project in Charlotte. This proved to be particularly pertinent, as the Charlotte dealership is located within 15 miles of the project, thereby ensuring service and parts are readily available.
‘Although Sandvik were fairly new to us, we knew there was an excellent opportunity with Plateau Excavation,’ commented Jack Evans, ASC’s general manager of the Buford location. ‘So we ramped up with the Sandvik line pretty quickly and worked very closely with Sandvik personnel to provide the necessary service and support on site for Plateau Excavation and LK Gregory in their drilling and blasting efforts.’
Considering the stringent production standards required by the project, Plateau Excavation’s owner and chief executive officer, Greg Rogers, sought the advice of LK Gregory vice-president Danny Camp when considering the drilling requirements. Mr Rogers’ first priority was to maintain the tight production schedules set out by Milord and Norfolk Southern, and Mr Camp, who had previous experience of Sandvik Ranger drills, had no hesitation
in recommending the new generation of Sandvik DX Series drills. ‘They [DX Series drills] seem to outperform the other makes in a construction environment,’ he said – an endorsement that is well backed up by his team of three operators, who between them possess more than 32 years’ combined experience operating surface drill rigs in a construction drilling environment.
The DX800 itself is a crawler-based surface drilling rig that is notably proficient in several critical areas: it pivots 180° on a turntable, thereby allowing the operator to drill more production holes while spending less time having to turn the rig around. By the end of a working day this means that more time has been spent drilling, and less time has been spent manoeuvring, which translates into greater productivity.
However, on a project of the size of the Norfolk intermodal yard, productivity comes second to safety. Fortunately, the DX800 is as safe as it is productive, which has proved to be vital as much of the site surface comprises a mix of rutted rock beds with rubble left over from previous site work, constituting a somewhat unreliable work platform. Nevertheless, the DX800s have risen to the task at hand, demonstrating their versatility by moving across the area with ease and drilling more holes at each station thanks to their turntable design.
An added benefit has been the functionality of the DX800, which is able to drill into rock vertically, horizontally, or at virtually any angle in between. With the boom of its high-rotation torque drill mounted on the turntable, the machine’s operator has unusually precise placement control of the drill. Use of the machine’s joysticks allows the drill to be swivelled, tilted and manoeuvred into place, regardless of how fractured or imposing the drilling surface might be.
However, according to Danny Camp, the most conspicuous advantage the Sandvik drill is its stability, which is an overriding concern for an item of equipment that mostly works on hard, irregular surfaces near steep drop-offs. The Sandvik cab’s robustly engineered and certified roll-over and falling object protection (ROPS/FOPS) is another key feature, as Mr Camp explained: ‘The work can be precarious, and that is one of the reasons why we chose the DX800. It’s widely regarded as a stable machine. You can put it just about anywhere and it will generate production.’
The DX800’s ability to remain stable while it drills is partly the result of its cantilevered design; the machine’s Caterpillar C7 Tier IV engine, along with a gearbox that regulates hydraulic and air-compression tasks, is mounted at the rear of superstructure. The weight of the power pack thus offsets the boom and drill at the other end, and because this is mounted on the turntable, stability is not compromised when the boom is moved from hole to hole. Furthermore, the DX800s are the first to be equipped with a Tier IV Re-Gen system, which equates to lower emissions and a reduction in environmental impact.
On the Plateau Excavation project, the trio of DX800 rigs is averaging 700 to 900 borehole feet per day, with the routine being to have the drills bore for one or two days with the grades of the project spanning from 0.3–0.6m in slopes to holes running 15.2–18.3m in the center line of the future rail line. When the blast site is ready, LK Gregory work side by side with Plateau Excavation, Milord Company, STV (representatives for Norfolk Southern) and operations at CDIA to ensure site safety is the top priority. Averaging between 6,858 and 9,144m3 of blasted rock per blast continually allows LK Gregory to stay in line with Plateau’s production standards. An estimated 229,366m3 of rock will be removed before the path of the rail line is cleared. Commenting on this performance, Plateau’s Greg Rogers said: ‘We have been pleased with the performance and production of the Sandvik rigs on the Norfolk Southern project.’
What has made the project even more demanding is the fact that the granite formation systematically being taken apart by Plateau comprises ‘some of the hardest rock we’ve worked with’, according to Mr Camp. It is hard, closely crystallized granite and nothing less than blasting will dislodge it. Although high-density rock such as granite is hard on a drill unit, conversely it is the best type of rock for blasting. ‘This is because of its density,’ explained Mr Camp. ‘It absorbs more of a blast’s concussion and thus the rock is severely impacted by it, fragmenting and displacing a targeted mass while keeping the seismic vibrations contained within the rock and not transmitting them to outlying areas.’ Conversely, blasting a softer rock is likely to produce more precarious situations and broader seismic activity.
Although the granite on this particular project is very hard, this is of little consequence to the DX800, which has been designed to penetrate any density of rock. This is particularly pertinent because, during a day’s drilling, density variations do occur. ‘When you are moving across any job, some rock will be a little bit softer in certain places than others. You can literally move just a few feet and the density can change,’ commented Mr Camp.
The density of rock aside, the hydraulic battering action of the drill against the rock always takes a toll on a machine. Fortunately, this is not the case with regard to the operators, as the DX800 possesses an air-conditioned and filtered cab, which protects the operator from noise and other emissions emanating from outside.