Latest Developments in Electrification
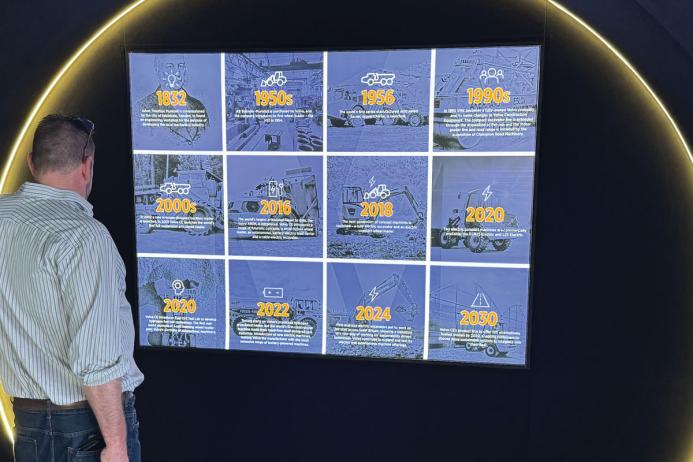
First published in the July 2024 issue of Quarry Management as Electrification
The ongoing drive towards net zero at Hillhead 2024
Dan Gilkes reports on some of the latest developments in electrification at this year’s show
One of the major takeaway themes from Hillhead 2024 was the continued move towards decarbonization of the equipment that is used within the quarry and aggregate industries. In line with other sectors, manufacturers and dealers have been launching an increasingly wide range of machinery powered by electricity to meet this requirement. This focus on battery and cable-powered plant will not only change individual machines, it looks set to completely overhaul that way in which the industry works.
The electrification of the plant business will even require a seismic shift in the way that events like Hillhead are run. While a team of diesel tankers currently travels around the site refilling demonstration machines each day, manufacturers and exhibitors will instead have to manage a refuelling process that calls for electricity or a hydrogen supply.
Will the bund surrounding the top of the quarry be covered in solar panels over the coming years, or will a dedicated wind farm spring up on nearby hillsides to power the equipment on show? Or will there be banks of batteries on each stand, to replenish supplies through the night?
Of course, not everyone is looking forward to this energy transformation with anything even approaching enthusiasm. If Bell’s autonomous dumptruck divided opinion among the more conservative members of the quarrying audience at this year’s event, then electric machines will prove equally contentious.
Yet, even a quick walk across the car parks above the quarry revealed that a rapidly growing number of quarry industry professionals relied on battery power for their journey to Buxton. Among the inevitable pick-ups and 4x4s, there were plenty of cars and SUVs with a green flash on their number plates, indicating their zero-emission status.
Of course, the quarry industry is no stranger to electrification. Companies have been using electric crushing and screening plants, electric conveyor systems, even electric face shovels, for many years. For stationary applications, that usually means utilizing mains grid power, with companies running cables to equipment working within the extractive process.
Looking ahead, the demand will be for electric power to be mobile, which requires both a renewable method of production and a way of storing energy within the equipment. For now, at least, that means using batteries. Hydrogen will offer an alternative, whether burnt in an engine or used a fuel cell, but the necessary infrastructure for the production of green hydrogen is not yet at a viable capacity for general adoption.
However, from the smallest mini-excavator to the largest asphalt and concrete production plants, an electric driveline is no longer something that manufacturers might offer in the future. It has become an essential part of today’s equipment line-up.
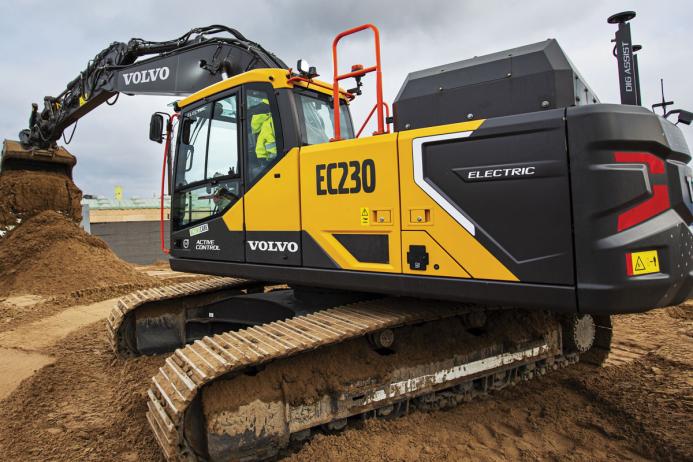
Digging and loading
Volvo CE distributors SMT are increasingly focused on electric drive, with the manufacturer recently launching a 23-tonne EC230 Electric excavator, its first mid-size battery-powered crawler machine. Powered by a 264kWh battery pack and running a 600V electrical system, the machine boasts a 4–5h running time, depending on the operation.
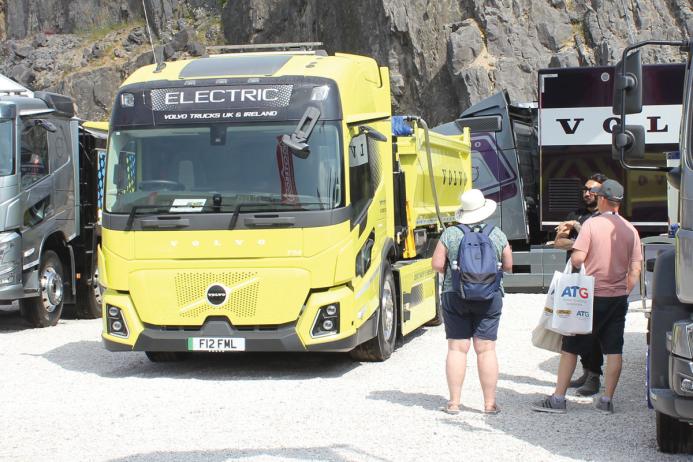
Volvo already have a range of electric mini-excavators and compact, battery-powered, wheel loaders. The company has also announced the upcoming launch of the EWR150 electric wheeled excavator and the full-size L90 Electric and L120 Electric wheeled shovels. Sister company Volvo Trucks also offer a range of electric rigid trucks and tractor units for road haulage, providing customers with both an on- and off-highway zero-carbon solution.
To meet the needs of customers recharging on site, Volvo have launched the PU40, a mobile power unit with a capacity of 40kWh that can be used to charge electric machines that are working off grid. The PU40 is charged from the grid while machinery is working, using a 6kW AC connection or, where possible, a 17kW DC fast charger. This then provides battery storage for equipment to charge from during lunch breaks or overnight.
‘At SMT we are committed to helping our customers work towards and achieve net zero and we believe that journey starts today,’ said John Lawrence, SMT’s Site Solutions product manager. ‘By targeting key areas that affect cost and emission output, we can help customers to reduce their carbon footprint and help achieve their sustainability targets.’
Case Construction Equipment have been building their full-electric range of equipment, with the 12EV compact electric wheel loader joining two battery-powered mini-excavators. The 3.8-tonne loader boasts more power than its diesel counterpart and its 23kWh battery provides 3–6h of operating autonomy between charging stops. The machine comes with a 230V on-board charger that can be used to top up the batteries overnight, or a 400V fast charger, that will take the battery from 20% to 80% in just one hour.
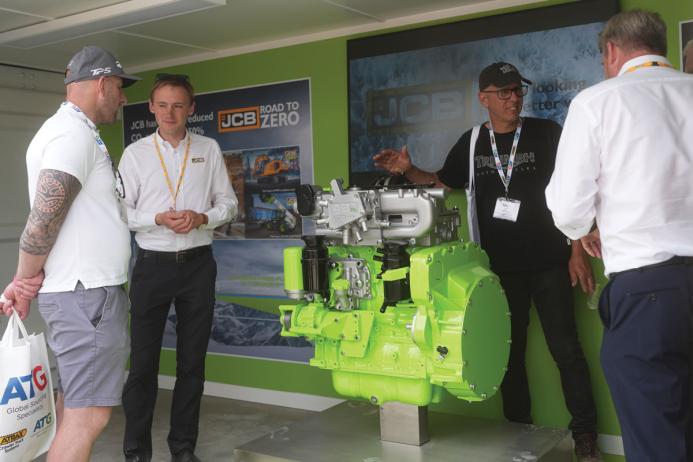
JCB have been at the forefront of both the battery-electric and the hydrogen revolutions. The company offers a growing range of E-Tech electric machinery, from mini-excavators to telescopic handlers, and has shown prototype hydrogen-powered versions of its popular backhoe loaders and Loadall telescopics.
Unlike many manufacturers that have looked at hydrogen as a solution, who have used fuel-cell technology from the automotive world, JCB have developed hydrogen versions of their own engine range. By using spark ignition heads and new turbocharging technology, the company has successfully developed a hydrogen engine that delivers the same power and torque as its own diesel models.
Critically, JCB have also developed a means of transporting hydrogen to individual machines on site, having converted a Fastrac tractor to carry bottles of the liquified gas to provide a refuelling solution. Though the hydrogen machinery is not yet for sale, it can only be a matter of time before the company makes the technology commercially available.
HD Hyundai is another company that has put as much research into hydrogen as into batteries, though in the case of the Korean firm that focus has been on hydrogen fuel-cell technology. The manufacturer has shown a prototype hydrogen excavator and will have more news at next year’s Bauma exhibition in Germany.
Before that, Hyundai have announced that they will show their first battery-electric mini-excavators later this year, with two models believed to be ready for launch later in 2024.
Perhaps unsurprisingly, Develon, who are now owned by HD Hyundai’s parent company, have also been investing in hydrogen fuel-cell and battery-electric research. The company has shown a prototype DL250 FCEV hydrogen-powered wheel loader that can also be transformed into a full electric model, by replacing the fuel cell and hydrogen storage tanks with a battery pack.
The company also shown a concept electric wheeled excavator, the 14W-EREV, that uses a 120kWh battery pack to provide 3h of continuous driving. As an option, the machine can be supplied with a second 120kWh battery, or as a hybrid driveline, using a 55kW diesel engine. Rather than using the electric motor to drive a conventional hydraulic system, the 14W-EREV uses electric travel motors, with a regenerative eDrive and eSwing hydraulic system powered by a second, independent electric motor.
With much of the early development of electric machinery focused on compact models, Develon also offer the SX7 electric skid-steer and the E19e electric mini-excavator.
Distributors Marubeni-Komatsu provided direct competition at Hillhead for Volvo this year, with Komatsu’s PC210LCE-11 crawler excavator. This 21-tonne machine is powered by a 451kWh battery pack, delivering up to 8h of operating autonomy. With zero-emissions and low noise levels, this tracked machine will spearhead Komatsu’s entry into the mainstream electric market.
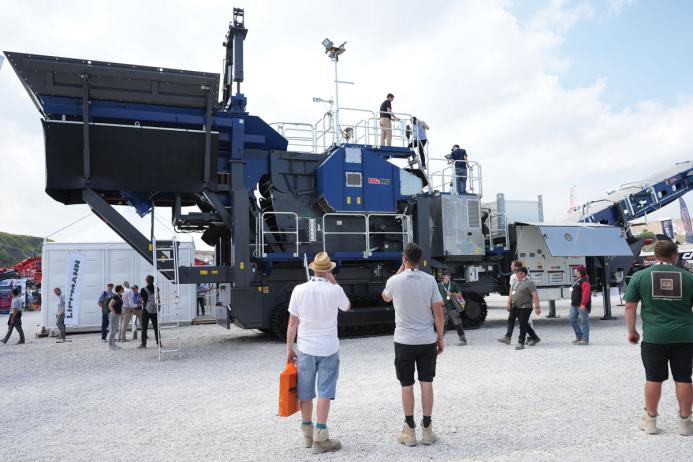
Crushing and screening
Crushing equipment supplier Agg-Pro recently added Swedish equipment manufacturer Jonsson’s L130 jaw crusher to their line-up. This 108-tonne crawler machine is powered by a 400kVA on-board generator but can easily be set to run from a mains electrical supply. Equipped with a Nordberg C130 jaw crusher and Jonsson’s own JF1250 feeder, the machine is powered by a 185kW electric motor.
The dealer has also introduced the 700ie Hybrid jaw crusher from Tesab. Producing up to 350 tonnes/h, the 700ie Hybrid matches the performance of the equivalent diesel-powered model. It is equipped with a 225kW removable diesel generator set with an uprated alternator. This is said to make the machine up to 33% more fuel efficient, with a 70% reduction in operating costs for the customer.
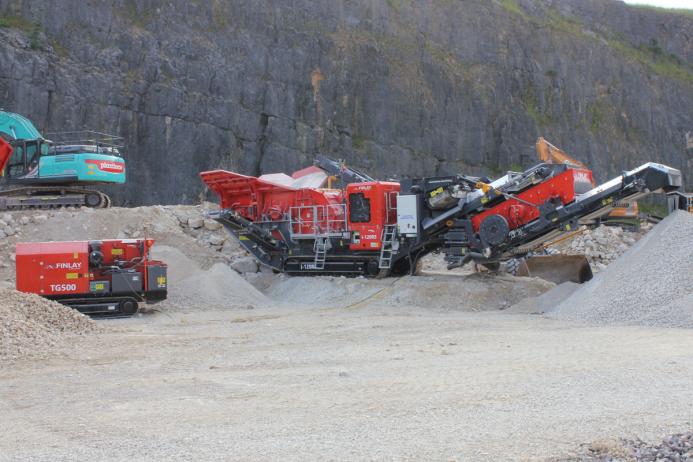
Finlay have unveiled electric variants of their I-120RS impact crusher and the 883+ scalping screen. The two machines can take their power directly from the mains, or from a secondary source such as a generator set. The company has taken input from dealers and customers to retain operational familiarity, allowing companies to move to electrified machines without having to radically change their operations.
The electric I-120RS provides the flexibility of a mobile crusher and a screening plant in a single machine, while a quick-detach two-deck screen delivers a quality product. The heavy-duty 883+ scalper can be used in primary or secondary screening applications in quarrying and mining, or in construction, demolition, and waste sites.
Finlay have also introduced their own range of generator sets, capable of providing power for its crushing and screening equipment when not in reach of mains electricity.
‘By adopting electric-powered mobile crushing and screening equipment, customers not only achieve environmental benefits, but also gain financial and operational advantages as well,’ said Finlay business line director Matt Dickson. ‘It also future-proofs their investments, as the industry moves towards more sustainable practices.’
Terex brand EvoQuip are taking a hybrid route to reducing emissions. The company offers both its Bison 160 jaw crusher and the Colt 1600 mobile screen in hybrid form. Both machines are electrically driven, with customers using site grid power to run the equipment. The Bison 160 is also equipped with an on-board generator, allowing the operator to move the machine and set it up ready for work when there is no mains electrical supply.
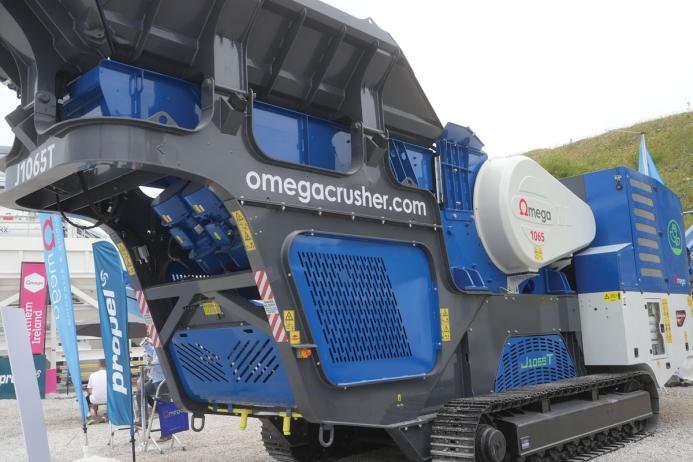
The latest advancement from Omega Crushing and Screening, a company which specializes in the production of zero-emission mobile crushers and screens, is the J1065T tracked jaw crusher. Specifically designed for the rigorous demands of quarrying, mining, and recycling applications, one of the standout features of the Omega J1065T is its dual-power capability with a Deutz power pack and efficient all-electric drive system. Omega say what sets it apart from other tracked crushers on the market is its ease of operation. With no complicated controls or systems to worry about, even novice operators can quickly get to grips with the machine.
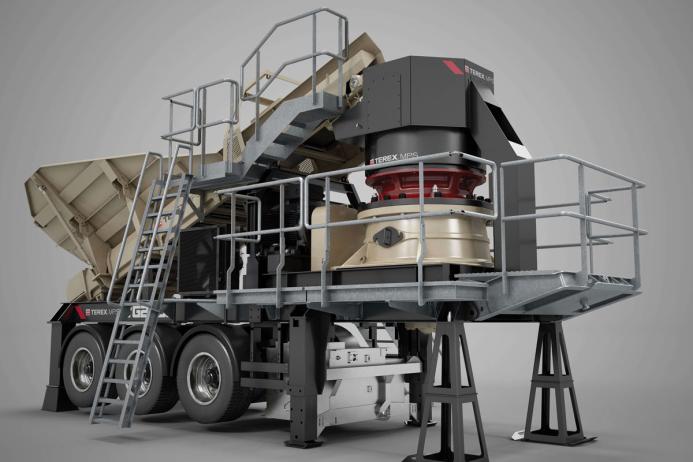
Terex MPS are pushing forward with electric machinery, with the launch of the WG220E portable cone crusher and the WV1400E mobile vertical shaft impact crusher. Targeted at mid-size users, the two machines are mounted on wheeled chassis that can be towed to site by a conventional truck. They are built to crush oversize material from wash plants and secondary/tertiary crushers and are fully electrically driven. This can be from mains grid power or from a generator.
Both models have a 5m3 feed hopper volume with a conveyor to feed the crusher and a foldable discharge conveyor for material stockpiling. The machines can be easily integrated with a company’s existing mobile crushing trains, whether tracked or on wheels.
‘There is a growing demand for crushing machines that offer a lower cost per tonne compared with traditional tracked diesel crushers, especially for mid-to-long-term contractors,’ said sales director Paul Lilley. ‘Electric machines are more efficient and have a lower capital cost, due to the absence of engine and track components.’
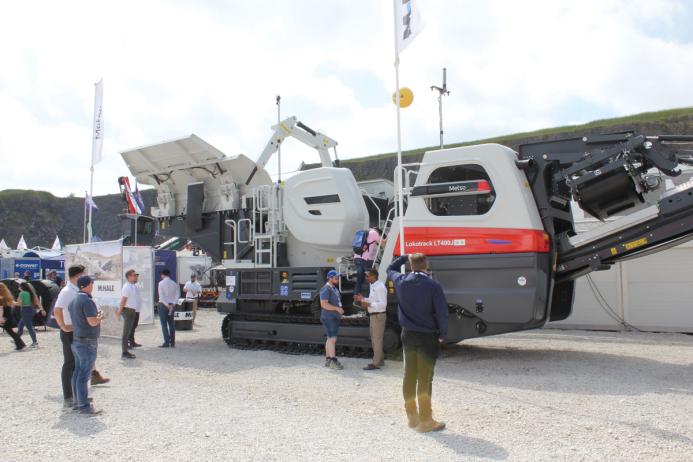
Metso Corporation, through their dealer McHale Plant Sales, are also making inroads into the hybrid diesel-electric market with their Lokotrack EC range of crushers. The EC range of machines can all be powered using an external electric supply, with on-board diesel generators for when mains electricity is not available.
The first two products in this line-up are the 68-tonne Lokotrack LT400J jaw crusher and the 50-tonne Lokotrack LT350C mobile cone crusher. The LT400J is designed for primary crushing of hard rock and recycled aggregates, while the cone crusher is intended for secondary and tertiary crushing in a range of industry sectors.
‘When external electricity is available, the new electric power transmission provides high capacity with minimized operational cost and CO2 emissions,’ said Jarmo Vuorenpaa, director of the new Lokotrack offering at Metso. ‘When not available, the on-board diesel gensets allow maximum independent operation time. Also, auxiliary units, such as mobile screens and stackers, can be powered from the same gensets, which will further reduce the need for power to run the complete plant.’
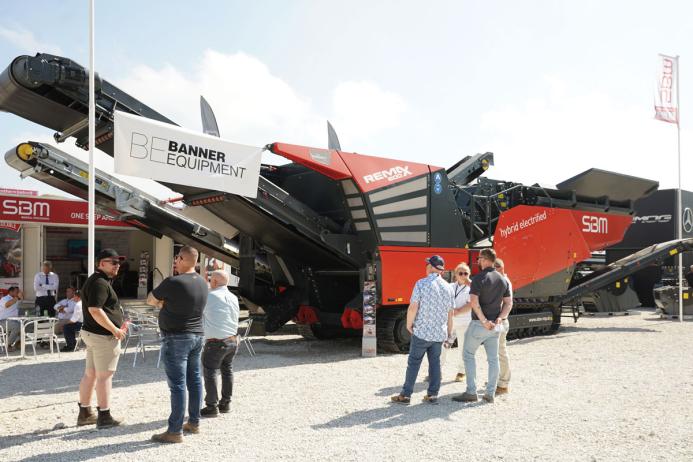
Austrian firm SBM Mineral Processing specialize in hybrid track-mounted crushing equipment. The company offers 12 models of Jawmax jaw crushers and Remax impact crushers, with operating weights from 23 to 160 tonnes. All use a diesel-electric driveline, with the option to use a full electric plug-in power supply from the grid.
The latest addition to this line-up is the Remax 600 impact crusher. This 80-tonne machine is powered by a Cummins Stage V diesel engine and a 520kVA generator. Alternatively, it can be powered using mains electricity, with plug-in switching and all system functions managed through the SBM Crush Control system.
‘Economic efficiency and environmental sustainability are playing an increasingly important role in operations, especially in the UK market,’ said SBM area sales manager Norbert Dieplinger. ‘Our diesel-electric drives are inherently much more efficient than fully hydraulic or partially electrified system concepts. On average, we use up to 40% less diesel for an even better output. Thanks to the various fixed speeds of our engines and of course fully electric operation, the immediate environment also benefits from significantly lower noise levels.’
Attachments and technology
With a growing number of battery-powered machines coming to the market, there will inevitably be concerns around the use of power-hungry attachments, such as hydraulic breakers. While the carrier machine will power the hydraulic system, the use of a high-flow attachment such as a breaker will have an effect on overall operating use.
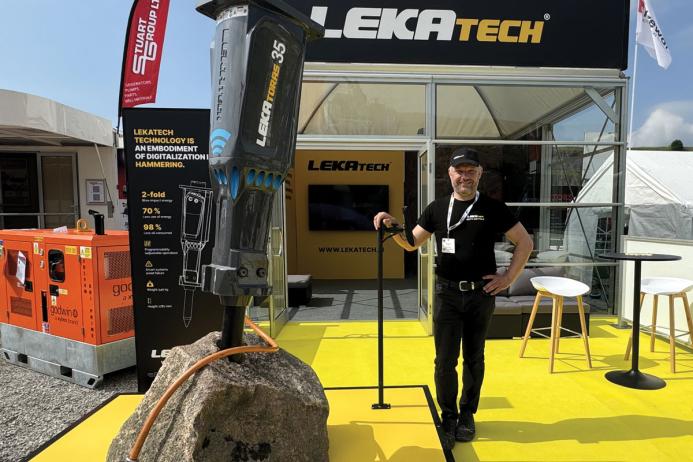
Lekatech aim to minimize the effect on the carrier machine’s batteries, by offering electric drive for the hammer, rather than using a hydraulic circuit from the machine. Built with a power-to-weight ratio that is similar to a conventional hydraulic breaker, the Lekatech Electric Hammer uses linear electric motor technology, producing high impact forces with minimal vibration.
The company claims that the Electric Hammer can deliver up to a 70% energy saving when compared with a hydraulic unit, while providing up to two times the blow impact energy of a hydraulic breaker of the same size.
Finding efficiencies and cutting energy use is not always about having the latest machinery. Mitsubishi Electric’s Automation Systems division prefers to take a more holistic view of a complete site’s energy use. The company’s ICONICS Suite is a software solution that organizes critical operational information to provide a range of dynamic dashboards that allow customers to analyse and visualize aggregate plant processes. By being able to see the complete picture, customers can identify targeted opportunities for energy reduction.
‘The aggregates industry uses many energy-hungry processes, so inefficiency can have a significant impact on overall profitability and sustainability,’ said Trever Herbert, business development manager. ‘Deploying the right energy-management solutions can help companies maximize uptime, achieve peak efficiency and improve competitiveness.’
JJ Loughran are another company capable of providing a complete engineering solution across a mining or quarrying operation. Using electric motor technology from ABB, variable-speed drives from Danfoss, and gear reducers from Motovario & Rossi, the company can reduce energy consumption and operational costs on site, while optimizing machine performance.
Whether converting from diesel to electric power, helping to increase output, optimizing motor performance or improving overall energy management, the company’s application engineers can advise quarry operators on the benefits of electrification and guide them through to unlock the potential of the plant.
Subscribe to Quarry Management, the monthly journal for the mineral products industry, to read articles before they appear on Agg-Net.com