Intelligent Integration
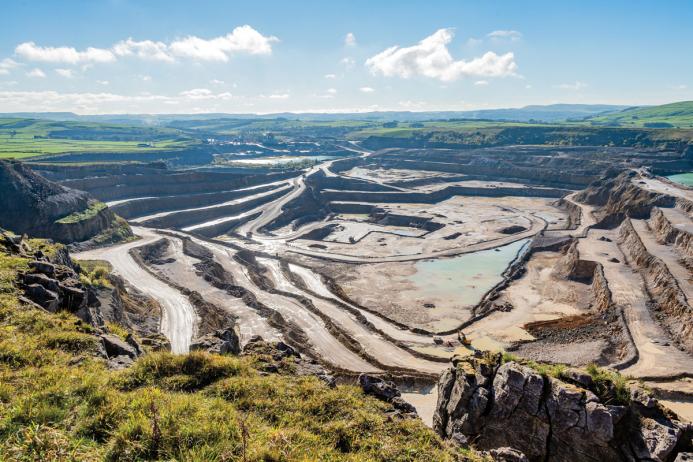
First published in the January 2024 issue of Quarry Management
An innovative platform to help businesses work smarter
Childhood friends Håkan Holmgren and Jonas Pålgård believed there had to be an easier way to handle different types of checks and procedures in heavy industry. Mr Holmgren’s upbringing in the quarrying industry is undeniable. He initially worked in a family business, eventually becoming its successful chief executive officer. Upon the company’s integration into the HeidelbergCement Group, his focus shifted to process development. Similarly, Jonas, from the Pålgårds family company, recognized the need for a streamlined system to monitor daily inspections and repairs on the machine park. With a background in interface and user experience (UX) design, he found these skills invaluable when co-founding CheckProof.
Their aim was simple: to create a system that was user-friendly for ease of reporting and monitoring combining tech with a simple interface, and in 2014 CheckProof was brought to market. It offers the ability to conduct daily checks and provide real-time reports.
Among the earliest adopters of this new system were Cemex, who use it primarily to conduct their health and safety and pre-start checks.
‘Prior to using CheckProof, most of our checks were paper based, which worked but we would end up with offices of filing cabinets and paper being passed from person to person. And when it came to reporting, there could be a slight lag with only the person holding the piece of paper knowing what happened,’ explained Kevin Cage, head of UK aggregate operations at Cemex. ‘We found that a lot of our managers were spending time on paperwork and this was keeping them from the tasks they needed to be doing. When we introduced the new system, we expected a little resistance but that didn’t happen – everyone adapted quickly.’
Implementing CheckProof was simple – Cemex employees were issued with a mobile phone or tablet to use the system wherever they were on site. These devices make the platform accessible for everyone and to keep workers safe, an internal security protocol limited access to other apps, ensuring staff were not distracted.
Mr Cage first discovered CheckProof at the bauma international trade fair, in Munich, just before the pandemic hit. He was hoping to find a new digital system to implement at Cemex. ‘We considered four other systems that provided really good analytical data but were hard to use,’ he explained, ‘but when I went to see CheckProof and was given a demonstration, it just ticked all the boxes. What we wanted was something easy for the operator to use. We worked on principle that if it’s easy for them to use, we’re likely to get good information.’
CheckProof offers application programme interfaces (APIs) and integrations with key manufacturers (there are pre-built integrations with Caterpillar, Liebherr, Scania, Terex and Volvo – among others), allowing users to connect existing systems and their fleet, stream telematics data in real time, and get a full overview of their assets. This allows their assets to ‘talk to each other’ and to stream data such as location, operating time, and fuel levels directly from the fleet into the platform. This information can be translated into insights and trends, and suggest potential areas of improvement. It is presented in a way that is easy to view and digest and can also be used to manage maintenance tasks such as servicing.
The convenience of the system is one of its key attributes, giving the user the ability to report deviations on machinery or vehicles simply by inputting basic information and, if necessary, a photo to support the entry. The manager will be able to see this information immediately and then acknowledge and reply with a note and a deadline for follow-up, if required.

Across Cemex UK, aggregates, asphalt, logistics, building products, ready-mixed concrete, and marine are all integrated into CheckProof, including all the service departments that feed into them. Keeping workers safe is always the priority and with so many parts of the business using CheckProof, it has made it easier to share learnings and simplify the lines of communication.
Would Kevin recommend CheckProof to other businesses in the industry? ‘Yes, it’s just a very versatile platform and the beauty of it is you can make it work the way you want it to work.’
CheckProof Key Features
Checklists and audits
Incident and case management
Deviations
Planning tool
API and Integrations
Fleet optimization
RFID
For more information, visit: www.checkproof.com
Subscribe to Quarry Management, the monthly journal for the mineral products industry, to read articles before they appear on Agg-Net.com