GEOVIA's four step approach to improved quarry productivity
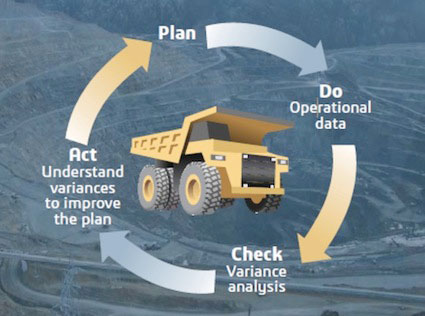
First published in the September 2013 issue of Quarry Management as Gaining an InSite
Increased control leads to increased productivity and efficiency in quarry operations
‘Productivity’ and ‘efficiency’ are two words that are often overused in today’s quarrying and mining industry. How often do quarry and plant managers drive productivity and efficiency by implementing new methodologies? In an industry where cost savings are imperative and margins are tight, the best operations require real control over what actually happens in both the quarry and the plant.
One way to stimulate productivity and efficiency in quarrying operations is to have real control and understanding of the production versus the plan. Operations can analyse trends to justify process changes and understand the best working practises for every activity from quarry to plant to final product. This process of reconciliation allows management to make the right decisions at the right time.
By adopting a Plan > Do > Check > Act > Plan cycle, operations will naturally increase in performance as they foster a cycle of continuous improvement. The cycle starts with the planning data, known as the ‘Plan’ stage. This planning data could be the grade/quality that was planned in the geological model, or the number of tonnes which were planned to be hauled during a shift. This plan is then executed during the ‘Do’ phase. Data are recorded during the activity, for example, on the Plod sheet in the trucks. This actual data can then be compared against the planning data to establish the variance, known as the ‘Check’ stage, which is discussed further below. Once any variance has been established, acting on the discrepancy will ensure that it does not happen again. This approach allows continuous improvement to be adopted and leads to a reduction in variance over time.
Many in the industry often struggle at the end of every month to compile and validate production data when reconciling. Often the figures between quarry production and the plant production do not match, and one or both departments are required to make adjustments. Typically, this involves multiple spreadsheets with little data validation and disparate data sharing. The fact that spreadsheets are used so widely throughout the industry often results in lack of data integrity or security, human errors, a slow end-of-month process and bottlenecks. There is a large amount of time spent preparing data in which, ultimately, there is little confidence. Also, the management of the discrepancies between claimed and actual is difficult. Operations must then understand where, why and what causes the differences.
Leveraging technology to drive efficiency
Technology exists to provide managers at both the quarry and corporate levels with better visibility of the operations. Technology systems give operations the tools they need to drive productivity and efficiency. Dassault Systèmes’ GEOVIA brand reconciliation advisor for Europe, George Long, says there are four simple steps operations should follow when looking to have better control in the short term.
Step 1 – Consolidate your data
To have visibility of actual production versus plan, all data need to be in one place. Data should be captured either manually or automatically through interfaces with existing third-party systems, such as geological databases or automatic data capture from machinery through fleet-management systems or SCADA systems. Budget and forecast information should be uploaded and kept up to date as appropriate.
Step 2 – Validate the data
Ensure the quality of the information entered. Reject erroneous data and have a workflow sign-off of the previous raw data. When poor-quality data is accepted, it will impact all subsequent downstream processes and analytics which utilize it.
Step 3 – Report regularly
Daily production, stockpile balances, monthly production, equipment performance, costings, employee activities, and other key measures should all be reported on a regular basis. Reports should be generated and distributed automatically, allowing employees to analyse and react to the findings faster.
Step 4 – Capture more data
By capturing more data, and more details about your operation, you will have more intelligence with which to make decisions to improve productivity and efficiencies. The more you know, the better control you have.
Reconciliation – where next?
The definition of reconciliation can vary considerably from country to country, site to site and role to role. The process can be used for material balance across the operation, distributing discrepancies in tonnages and grades/qualities back to certain movements or activities in the operation. Other operations use the term reconciliation for their production accounting. However, it is most commonly used to compare planned and actual data. When it comes to reconciliation, there are two important questions to ask. Why is the process undertaken? And, what is done with the results?
Traditional reconciliation involves a retrospective analysis of the performance of the operation. This analysis often leads the quarry to impose certain corrective factors, which are taken forward to improve future plans. The typical reconciliation procedure for a quarrying operation is a month-end process which validates and approves the production figures for the month against what was planned during that period. The quarry and the plant usually follow a similar procedure and the quarry reports are compared to the plant results. The main purpose is to achieve consistency between the quarry and the plant; validate assumptions; check factors such as truck factors and call factors; and assign ‘credits’ to certain parts of the value chain, where necessary.
These factors are usually established over a long period of time and are often refined over the life of the quarry. The performance of the quarry is indicated by these factors and in an ideal situation the planned values would equal actual values. However, the number of variables across the process chain makes this unreasonable.
The actual process of reconciliation involves redistributing the discrepancy between the planned and the actual across the quarrying value chain. It is up to the individual operation how this material balance is managed. The value chain and discrepancies can be split into individual business units or reconciliation envelopes and distributed across the entire chain. Inputs and outputs from these reconciliation envelopes can be measured and any discrepancies can be manually or automatically distributed across the attributes within that envelope. Reconciliation can be undertaken at any level in a quarry operation, including quarry production and plant production, at the finest level of detail.
Variance analysis
The analysis of the variance data is the most important stage of the reconciliation process. By understanding the reason behind the discrepancy, changes can be made to operational processes to reduce the variance next time. As previously discussed, many operations simply calculate the variance and use factors to establish equilibrium in the planned and actual data in an operation.
Simply knowing this variance is not conducive to improvement. The important point is to understand where, why and how this variance occurred and then make adjustments to the figures and to the operations to ensure that these discrepancies do not continue. The understanding of the cause of the variance is the key to improving the operational efficiency and reducing the variance next time. This kind of analysis of data is invaluable to quarrying operations.
The industry must analyse the trends to understand the cause of the greatest variance. For example, the operator may notice that a certain piece of equipment consistently has a variance of –20%. Once the operator notices this pattern he or she will begin to look at the different parameters that are associated with that piece of equipment. The operator then orders a change in the load factor that is used for the machinery, as this parameter was last updated three years ago when the equipment was originally purchased. Immediately, there is an improvement in the variance between the planned and the actual associated with that piece of equipment.
Closer analyses of variances are a key part of the continuous improvement culture in a quarry operation – something that drives productivity and efficiency in an operation. Technology can aid in gaining control of operations whether it be operational reporting at quarry level or corporate visibility from head office.
GEOVIA, known as Gemcom Software prior to their acquisition in 2012, are now a part of Dassault Systèmes, who provide business and people with virtual universes to imagine sustainable innovations. Offering world-leading solutions that transform the way people work, the group brings value to more than 170,000 customers of all sizes, in all industries, in more than 140 countries. As part of Dassault Systèmes, GEOVIA are a leader in the delivery of innovations in 3D modelling and simulation for mining and quarrying, and are home to world-renowned solutions such as Surpac, GEMS, Minex, Whittle, MineSched, PCBC, Hub, and their reconciliation solution, InSite.
For further information visit: www.3ds.com/GEOVIA.
- Subscribe to Quarry Management, the monthly journal for the mineral products industry, to read articles before they appear on Agg-Net