New Asphalt Mixing Plants from Ammann
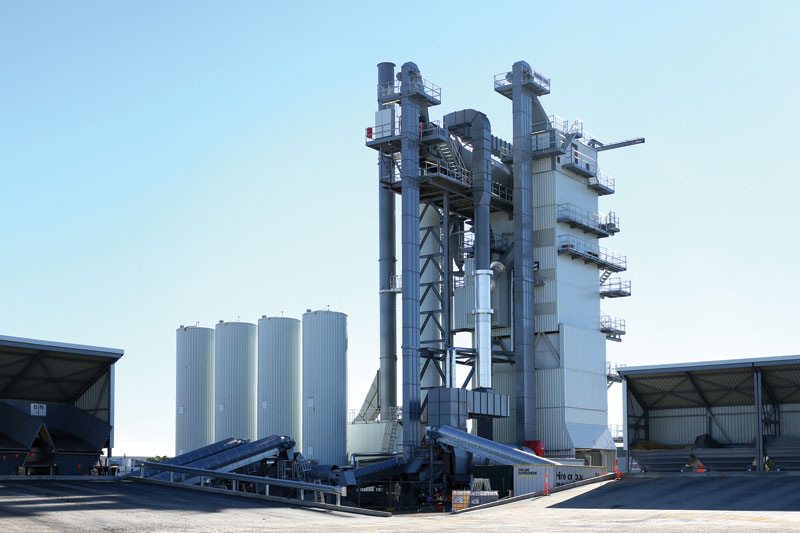
First published in the January 2014 issue of Quarry Management as Ammann Universal HRT
Latest innovative design from Ammann sets benchmark for asphalt mixing plants
In the last decade the world has been heavily focused on the environment, energy efficiency, improving safety in the workplace and reducing operating costs. In the asphalt industry, these initiatives have motivated manufacturers such as Ammann to develop new products and features to accommodate the latest requirements from authorities and consumers, and also to invest heavily in research and development to stay ahead of the game and implement new innovations and technologies.
Recently, key staff from Australia’s asphalt industry have travelled to Europe to learn more about the latest developments in sustainable asphalt production and high-percentage recycling technology. During technology tours that Ammann conducted with the Australian delegates, the company’s latest concept – the HRT (High Recycling Technology) series – was presented for feedback to see if the Australian market was ready for such a plant.
A delegation from Downer, the New South Wales-based providers of engineering and infrastructure management services, saw this concept as the way forward and quickly identified the advantages such an investment would have on their local business, with regard to efficiency, productivity and the ability to service almost any customer, regardless of their asphalt needs. Downer’s staff also contributed to the discussions and made suggestions, based on past operational experiences, which were considered very useful and, in turn, included by Ammann in the plant design.
Not only does the plant fit the mould for the changing asphalt landscape in Australia, with a move towards higher RAP content and warm mixes, the latest design also now allows for more room on each level of the plant, meaning the ergonomics, access and working areas fit with workplace health safety regulations in Australia. The construction design and enlarged work spaces at each level also allow for the plant to be fully clad, which helps to reduce noise.
The Universal HRT plant for Downer’s Bayswater facility was manufactured in April and put on display at the Bauma exhibition in Munich to show the global industry the latest in technology and innovations. ‘For those people who attended the exhibition, it would be fair to say that the Ammann stand was a highlight and the amount of people who inspected the plant from top to bottom was beyond our expectations,’ said Paul Vandersluis, managing director of Ammann Australia. ’The amount of positive feedback we received, especially from the Europeans, was astounding; and so to was the level of surprise and reaction from them when they were told that the plant was going to Australia.’
With this new plant concept, Australia is now seen as a global leader in asphalt production. This latest technology has been so well received that, since Bauma, a number of these plants have been sold into Europe, some of them even with the 100% recycling dryer.
Difference between latest innovations and a conventional asphalt plant
The Universal HRT brings a fundamental change in recipe composition and asphalt plant design. In the past, the question was how much recycled material could be added. Now the question is how much virgin aggregate needs to be added to the recycled material. This revolutionary change in the production process is reflected in the design of the Universal HRT and offers much more flexibility. Recycling can now be a mainstream part of the production process (and no longer a maintenance-intensive attachment) for those producers who have markets that can optimize RAP, as well as those who need retain mainstream virgin materials, but who need the flexibility to make various RAP mixes.
The Universal HRT allows the use of up to 70% preheated recycled material via a dedicated RAP dryer, which is positioned directly above the mixer. Cold recycled material can also be added into the mix or a combination of both can be used together. This change in the production process provides a solution to the future challenges in road construction. The HRT plant is equipped for the production of hot-mix asphalt, low-temperature asphalt as well as cold asphalt, all of which form part of the concepts of sustainability and flexibility. The plant is also recognized for its environmental features, which are incorporated into the standard design, including live energy consumption data, a ducted vacuum system throughout the plant, full cladding, and air extraction from the load-out area to the filter.
The Universal HRT has many other features to make life easier for the operator. The Ammann as1 control system, which is fully equipped with energy monitoring, peak load management and fully automated loadout modules, makes the plant very user-friendly.
The first of the Downer Universal HRT plants has been operating in Wingfield, South Australia, since June 2013 and was producing asphalt with up to 70% RAP content within its first week of operation. Laboratory tests have shown that the asphalt complies with all specifications and that there is no difference between virgin asphalt and high-percentage RAP mixes. Paving crews were extremely impressed with the 70% recycled asphalt and said it was the same as paving virgin asphalt. Rosco Whitcombe, a Downer asphalt roller operator for some 40 years, commented: ’I am very impressed with the way which this high-RAP mix rolls up.’
Steve Ainscow, surfacing manger for Downer South Australia, said: ’As expected, the new Ammann HRT plant provided us with a significant improvement in capability and we have already noticed increased productivity being achieved without compromising our flexibility. This flexibility allows us to provide the full range of RAP content mixes (0% to >75%) catering for the varying individual needs of our clients.’
Many highway authorities and other customers of Downer who have visited the plant during full operation have been impressed with its capabilities and level of control when using high percentages of RAP in the mix designs. End-users such as the City of Salisbury, in South Australia, are starting to use the high-RAP mixes from the plant as part of their day-to-day business.
Peter Levett, capital works officer with the City of Salisbury (CoS), said Downer had now supplied 20%, 50% and 70% RAP-content asphalt as well as warm-mix asphalt to CoS. ’The high-RAP asphalt appears no different to traditional virgin asphalt,’ he said, adding that the use of high-RAP asphalt on CoS road-rehabilitation projects had made a significant contribution towards the achievement of Salisbury’s carbon-reduction targets.
- Subscribe to Quarry Management, the monthly journal for the mineral products industry, to read articles before they appear on Agg-Net