Exploring Innovative Road Materials
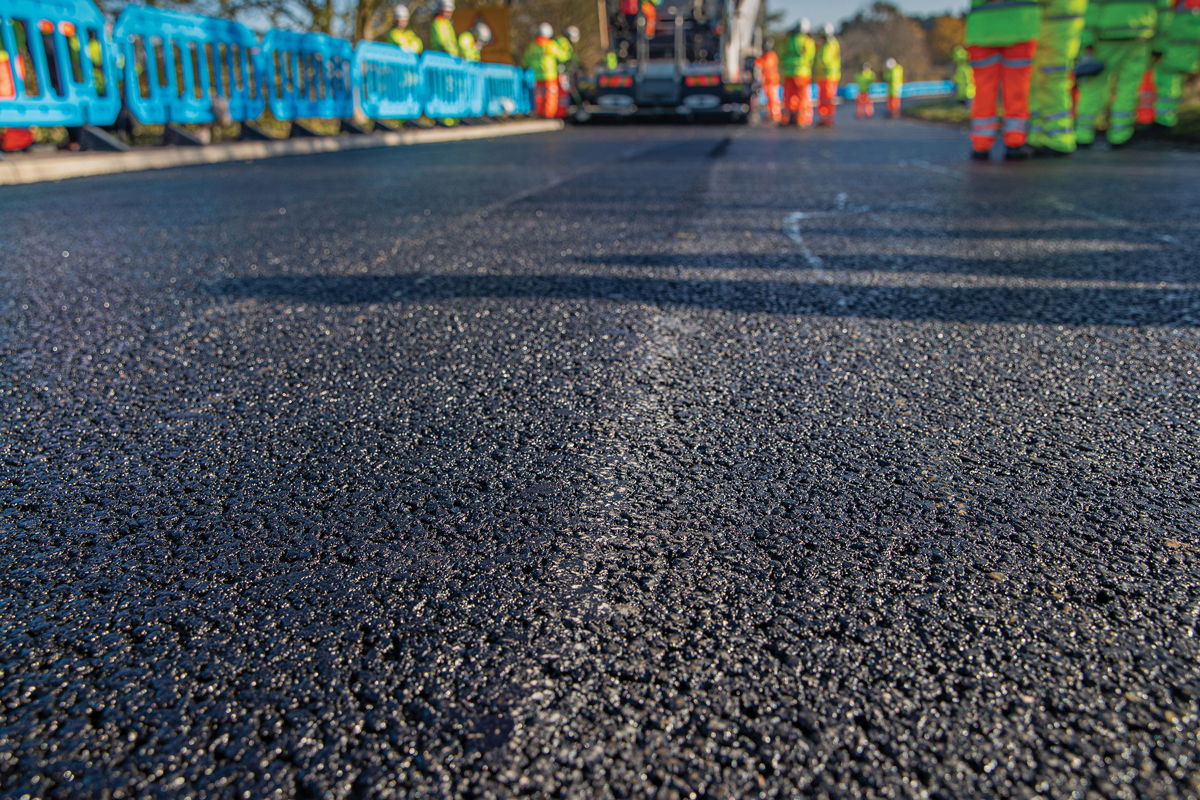
First published in the January 2020 issue of Quarry Management
Skanska are trialling new materials aimed at reducing potholes and carbon, to introduce greener, more durable road surfaces across the UK
In November last year, Skanska laid fully recyclable, graphene-enhanced asphalt on a busy main road in Curbridge for Oxfordshire County Council, in a trial that saw this material used on British roads for the first time. The works, which were delivered by subcontractors Aggregate Industries, involved the removal and reinstatement of the existing carriageway to a depth of 150mm over a 750m long section.
One lane was replaced using conventional materials, effectively acting as the control measure, while the opposite ‘trial’ lane was resurfaced using the asphalt enhanced by the innovative asphalt modifier developed by Iterchimica. If successful, this new graphene-enhanced material will significantly increase the durability of asphalt used in highways maintenance.
Meanwhile, in Essex, for the first time on the M25, Skanska laid an asphalt surface course between junctions 25 and 26 containing 50% recycled asphalt pavement – five times more recycled material than any other motorway surface, paving the way for greater use of reclaimed materials on UK’s roads.
This work, carried out in partnership with client Connect Plus and suppliers Toppesfield and FM Conway on behalf of Highways England, is significant as until now, standard practice has been to limit the recycled content of surface courses for motorways and A-roads to around 10%. The introduction of 50% recycled content marks a step change in the use of recycled material on UK roads that could result in huge environmental benefits if adopted across the network (see item below).
Jim Daughton, Skanska’s operations director, commented: ‘Exploring these new materials is about taking a new approach to tackling two of the biggest issues facing the highways industry and UK drivers – reducing potholes and improving the quality of our infrastructure for the future while driving down carbon.
‘We’re always looking for new ways to provide best value and our innovative approach enables us to deliver better and more effective projects for our customers and their communities, so we’re delighted to be the first to trial graphene asphalt in the UK and increase use of recycled materials.
‘If successful, these innovative products could transform highways maintenance in the UK, extensively extending the life of key highways infrastructure affected by significant traffic loads, while reducing carbon, which is key as we work with our supply chain to achieve net-zero carbon emissions by 2045.’
Jason Russell, Oxfordshire County Council’s interim director of community operations, said: ‘Oxfordshire County Council is always keen to explore new products and processes to not only improve the network for our residents, visitors and businesses, but more importantly, to make sure that we maximize the resources we have and deliver as many improvements as we can.
‘Working with Skanska, we recognized the opportunity to be at the forefront of developing new materials which will enhance the roads in the UK. We have taken the approach that trials are an important factor in pushing the boundaries, and without the forward thinking we have adopted we would be behind the development curve and not offering our residents the best we could offer in terms of spending public funds wisely.’
Paddy Murphy, managing director of contracting at Aggregate Industries, commented: ‘Working collaboratively with Skanska and the other parties involved has enabled us to successfully supply and lay this innovative material, which incorporates Gipave into our SuperCurve high-performance asphalt formula. We hope this trial will go on to prove that this asphalt is more durable and can be used across the UK to improve the lifespan of our roads.’
Andy Dean, chief executive officer of Connect Plus, said: ‘At Connect Plus, we are committed to reducing environmental impact and to creating a sustainable and durable road network. We are always looking to identify ways of improving roads users’ journeys so we welcome Skanska’s trial of recycled asphalt on one of the UK’s busiest motorways.’
Both new materials will now be monitored and assessed, and Skanska have already begun discussions with Connect Plus to trial graphene-enhanced asphalt on the M25 DBFO network, which could influence the Highways England network, paving the way for more widespread trials across the UK.
Step change in RAP usage on UK roads
FM Conway’s expertise in recycled materials has allowed an asphalt surface course containing 50% recycled content (RAP) to be laid for the first time on the UK’s strategic road network. The material was laid on a section of the M25 between Junctions 25 and 26 during an overnight closure in September 2019.
The surfacing material was made by mixing the RAP with virgin aggregate and FM Conway’s in-house designed and manufactured polymer-modified binder (PMB). The RAP for the project came from two ‘donor’ sites within the Connect Plus area, where Skanska were required to plane off the existing surface course for remedial works. Prior to planing, FM Conway took 24 core samples from the two sites and tested them in their laboratory to ensure the material would be suitable.
Mark Flint, technical manager at FM Conway, said: ‘Extensive core sampling and testing was imperative as we were looking for the correct grade of aggregate as well as the right polished stone value. Being able to carry out the research and development at our technology centre and engineer a bespoke polymer-modified binder at our PMB plant was beneficial to the success of the mix.’
In collaboration with Toppesfield, FM Conway designed the mix specifically for the project and Skanska applied successfully to Highways England for permission to depart from its standards, which only allow for 10% RAP content.
Paul Phillips, technical director at Toppesfield, said: ‘Our collaborative process of research and development is to ensure that the resulting material is at least as good as the generic. The core sampling was an important part of the process as was the engineering of a complementary PMB to provide a mix composition fit for its intended purpose. This collaborative approach by Toppesfield and FM Conway demonstrates support of the circular-economy ethos and upholds the three pillars of sustainability.’
The planings from the donor sites were taken to FM Conway’s Colthrop recycling plant, near Thatcham, in Berkshire, where they were crushed, screened, tested, segregated and stored. The day before the material was due to be laid, the planings were transported to the company’s Heathrow recycling and asphalt plant for mixing. On the night of the road closure, the mixed surfacing material was taken by truck for laying by Toppesfield. A total of 260 tonnes was laid as surface course on a section of lane one (the inside lane) of the anticlockwise carriageway of the motorway, to a depth of 45mm.