Delivering Carbon Reduction in Concrete
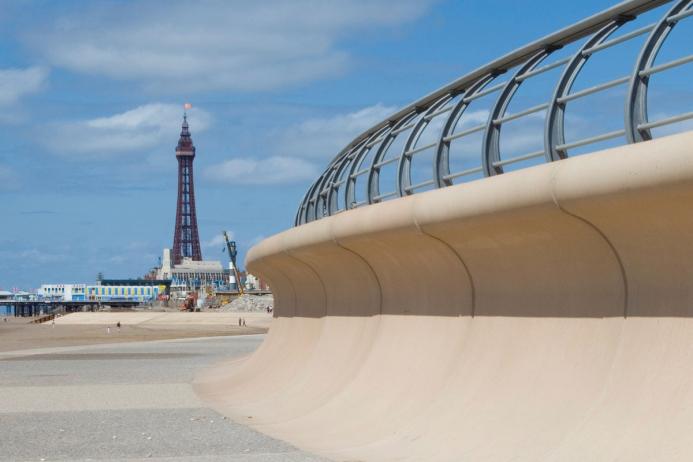
First published in the July 2025 issue of Quarry Management
By Phil Matthew, national commercial director (bulk cement), Heidelberg Materials UK
The world needs smart, sustainable, and resilient infrastructure, but challenges like climate change and limited resources mean that the production and use of heavy building materials needs to evolve.
Ready-mixed concrete is the most widely used building material in the world and is essential to society as a cornerstone of our built environment. It is flexible, versatile, durable, and strong, and is used in a wide variety of applications including housing, commercial and high rise buildings, road construction, and major infrastructure projects such as bridges, tunnels, airports, and sea defences, as well as energy and water plants.
It also absorbs CO2 throughout its life and is 100% recyclable, contributing significantly to the circular economy and providing materials with lower embodied carbon.
However, it is no secret that the production of CEM I Portland cement (PC), which is a vital ingredient in concrete, is energy intensive and produces CO2 due to the calcination of limestone and the fuels used to heat the kiln.
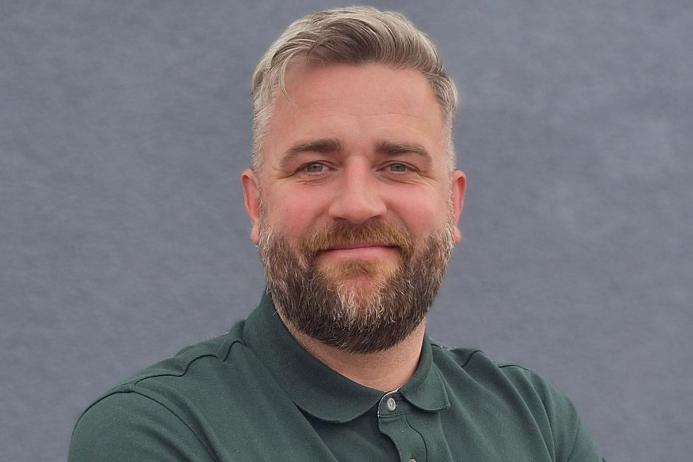
Heidelberg Materials UK have invested heavily to reduce process emissions through improved efficiencies and increasing the amount of alternative fuels used to 80%. But almost 70% of the CO2 emissions produced arise from the chemical reactions that take place during manufacture, so cannot be avoided by using low-carbon or renewable energy sources.
That is why the company is also leading the way in developing carbon capture and storage facilities that will prevent these emissions from entering the atmosphere in the first place. However, until this technology is widely available, developing and using supplementary cementitious materials (SCMs), which reduce the CO2 impact of concrete by replacing some of the cement content, remains vital to minimizing carbon emissions.
Best-known and most effective SCM
Ground granulated blast-furnace slag (GGBS) – a by-product of iron and steel making – is one of the best known and most effective SCMs and has been used for more than a century, with the first British Standard for Portland blast-furnace cement published in 1923[1].
GGBS can be used almost anywhere concrete is needed – from sustainable housing development and soil stabilization to wind farms and road building – and is typically used in major construction projects such as bridges and sea defences. It can replace a substantial part of the PC content in concrete – up to around 70%, but can be even higher in special applications.
It is this high replacement level that means GGBS is the most effective SCM in terms of delivering carbon reduction as others, such as fly ash (FA), calcined clays, and limestone fines, can only be used to lower replacement levels without impacting on the performance of the concrete.
In addition to the environmental benefits to be gained from its use in both its production and throughout the life of the structure, GGBS does not require the quarrying of new materials and the resulting concrete is 100% recyclable at end of life.
Clarity on the environmental performance of Heidelberg Materials UK’s GGBS – evoBuild low-carbon GGBS (previously known as Regen GGBS) – has been provided with a new Environmental Product Declaration (EPD). Published by leading EPD programme operators EPD-Norge, in accordance with EN 15804, it confirms that the Global Warming Potential (GWP) of evoBuild low-carbon GGBS, including an economic allocation for the granulate and the emissions from transport of imported granulate, is 155kg CO2e/tonne. This compares with 840kg CO2e/tonne for the average GWP for CEM I in the UK[2].
Added strength and durability
The use of GGBS is also proven to increase the long-term durability of concrete, further cutting a project’s environmental impact by reducing the amount of repair and maintenance needed and extending the service life of concrete structures.
The heat generated by concrete as it hydrates – particularly in large or deep pours, can affect a structure’s overall strength and durability. Concrete containing GGBS generates a lower heat of hydration compared with cement-only concretes, minimizing the generation of heat and reducing the risk of thermal cracking. The greater the proportion of GGBS in the mix; the greater the reduction in temperature rise and the rate at which heat is developed.
GGBS also:
Enhances resistance to both the ettringite and thaumasite forms of sulfate attack
Lowers ingress of chlorides into a structure
Minimizes the risk of alkali silica reaction
Provides better resistance to acid attack
Lowers propensity to delayed ettringite formation.
Secure long-term supply
In recent years the UK’s domestic iron- and steel-making industries have diminished and now just one steel works with blast-furnace operations remains in Scunthorpe. As a result, Heidelberg Materials need to import granulated blast-furnace slags from other countries.
Yet, despite the CO2 emissions associated with transportation, importing into the UK is still a very efficient use of the granulate, which is a traded commodity that benefits the UK economy.
This is because the UK has several deep-sea ports which can accommodate large, 40,000-tonne ships, to efficiently import granulate to grinding facilities which are all based in coastal regions. The UK also tends to have shorter inland transport distances than other countries, helping to keep transport-related CO2 emissions to a minimum.
Heidelberg Materials UK have been importing granulate for decades and have wide experience of producing GGBS from a variety of sources. Through their parent company, they have access to the global granulate market for both long-term contracts and spot requirements.
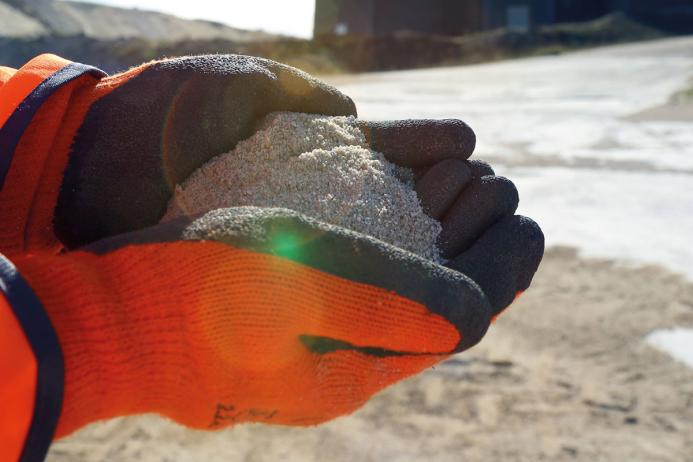
The anticipated long-term trend of a reduction in global blast-furnace steel making cannot be ignored. However, Heidelberg Materials UK have a safe and secure supply for their anticipated granulate demand for at least the next decade. To satisfy the changing demand for lower-carbon concrete solutions, Heidelberg Materials are also proactively assessing and developing future SCM options, which include calcined clays and natural pozzolans.
REFERENCES
CLEAR, C.: ‘UK Procedures for the Use of Additions as Part of Cement in Concrete’, 2015, XVII ERMCO Congress, Istanbul.
MPA Fact Sheet 18, Embodied CO2e of UK cements.
Subscribe to Quarry Management, the monthly journal for the mineral products industry, to read articles before they appear on Agg-Net.com