Talking About Our Generation
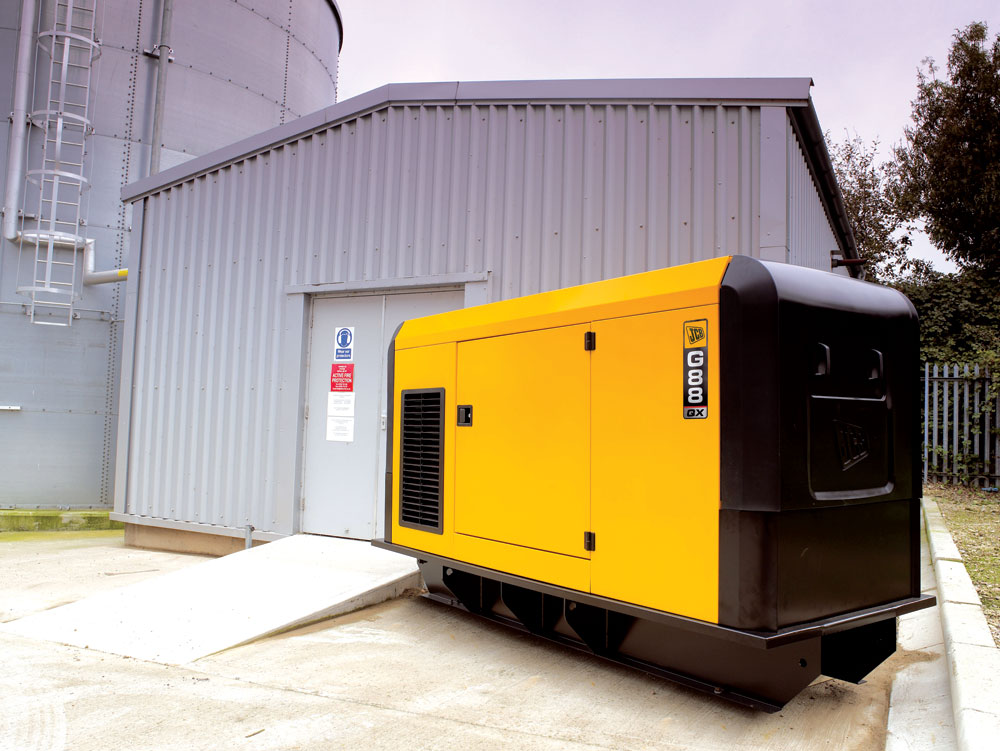
JCB Power Products Ltd have made great strides since entering the power-generation market in 2006 and now boast a range of 44 models with major sales into the quarrying, construction and waste and recycling sectors. Richard Butler, sales director with JCB Power Products Ltd, examines the key factors to consider when selecting a generator for powering quarry equipment
Generators are the most effective method of providing temporary or permanent power to sites that have limited-current supplies or do not have access to mains power. A generator can provide the exact voltage and frequency required for the site set-up, whether for buildings, site equipment or machinery.
When selecting a generator, therefore, the first step is to establish certain key criteria, such as: what voltage will be needed? Will it be single phase or three phase? What type of motor or conveyor starting is required and what is the start-up load?
Most general equipment, such as household appliances, heaters, lights etc, typically operate at single phase. The key benefit of three phase, however, is that more pieces of equipment can be supplied. Importantly, it will also supply industrial equipment specifically geared to a three-phase supply, such as motors and conveyors.
The size of a generator is measured in kVA (kilovolt amps), which has a direct correlation with kilowatts. With three-phase systems the actual power output is dependant on the power factor. Most common is a 0.8 lagging power factor, and generator performances are generally calculated on this basis. If the power factor is less than this the generator’s kVA rating decreases and a larger unit may be required to power the equipment. Single-phase equipment is at a unity power factor, shown as the number 1.
Voltages and frequencies vary around the world. Frequency relates to the speed the alternator is being turned by the engine. It is normally set to 50Hz in European locations and 60Hz in the Middle East and America. To achieve 50Hz the engine operates at 1,500 rev/min and for 60Hz it is at 1,800 rev/min on a four-pole alternator. The variance in voltage can be much greater – from 110V to 480V dependant on location. This is easily adjusted by the configuration of the alternator and its AVR (automatic voltage regulator).
Manufacturers will be able to provide readings for the equipment that a site needs to provide power to, and with this information the generator provider will be able to calculate the size of the unit required. With complicated installations it is worth requesting that a technical representative visits the site, to ensure the correct power provision is specified.
In terms of their structure, most generators are very similar, consisting of an engine, alternator and control panel. The engine provides the power, the alternator provides the electricity and the panel starts, stops and controls the unit.
In addition to the key factors of power, frequency and phase, the specifics of an individual application will determine any additional features and performance benefits that may be required. Health and safety, service support, location and environment, controllability and the nature of the power required are all key considerations.
An effective control panel should incorporate devices to allow the user to monitor the performance of the engine and alternator. Further to this control element, there are protection switches that cover all health and safety aspects of the system. These include oil and temperature for the engine, and ‘overvolt’ and ‘undervolt’ for the alternator. A main circuit breaker protects the outgoing current from overload. These are standard features on most generators but further options can be added specific to a particular application, eg earth leakage protection, low coolant levels, low fuel levels, where monitoring would be beneficial. It is essential that generating sets have emergency stops; canopied units must have two – one located internally and one externally.
All control-panel functions can be operated directly on the generator or via remote monitoring using a GSM system, allowing generator control from any location worldwide.
Diesel-, petrol- and gas-fuelled generators are all available. Most small units up to 5kVA are petrol driven, while diesel units range from around 5kVA up to 2,500kVA or more. Gas units are very rare and normally only used in specialist markets, such as waste sites. Within the quarrying sector diesel powered generators are by far the most common but, with recent environmental concerns, biofuels are becoming more widely used.
Owing to their robust build and ease of maintenance, diesel generators are well suited to the day-to-day rigours of the quarry environment, with units regularly used for powering crushing plant, conveyors and on-site offices. Most generators in a quarry will be canopied and fitted with heavy-duty air filters. The canopies are constructed from heavy-duty galvanized steel. With regular servicing, diesel-engine generators can provide reliable continuous or standby power in extreme conditions.
To power larger equipment on site, generators boast impressive torque for starting motors. The main types of motor starting are direct-online and star delta. To start these motors, considerations relating to the size of unit required differ greatly. Direct-online motors require up to seven times their rating in kilowatts to start, whereas star deltas require around two-and-half times their rating. With the addition of electronic fuel governing they provide excellent control for crushing equipment.
To aid the starting and running of quarry-based or large industrial equipment, further optional equipment can be added. For large direct loads, a PMG (permanent magnet generator) can be fitted to the rear of the alternator along with an uprated AVR. The PMG delivers more current into the alternator windings to allow increased power output direct from start-up. This also helps to increase the initial load percentage demand of the generator. The PMG option optimizes fluctuating voltages applied by constantly differing load demands. The uprated AVR controls this extra current so that it does not damage the main alternator.
An ATP (automatic transfer panel) monitors the incoming mains supply in a stand-by application and is linked to the generator control panel. If mains power becomes unstable or there is a power cut, it will automatically start the generator and take on the functions of the mains. When mains power comes back on, the generator will disengage and return load to the mains supply. In a quarry setting, it is advisable to add a water jacket heater and a battery charger to the stand-by generator to ensure efficient start-up after prolonged periods of non use.
Another key way of optimizing performance is synchronization. This allows the user to run two or more generators in parallel. Its main use is for applications demanding uninterrupted power, so if one unit fails the other automatically picks up the load to ensure a continuous supply. While they are running together they will share the load equally (load sharing). If the load drops very low one will shut itself down until the load picks up again. This ensures optimum fuel economy and efficient output from the set.
Other aspects of equipment selection will be governed by the likely conditions and environment in which the generator is to be installed and operated. All diesel generating units with canopies are also sound attenuated. This allows optimum cooling at set dBA levels, so the unit will be below the rated noise levels demanded by local authorities without affecting cooling or power levels. If the unit is to be stored within a building, it may not necessarily be canopied but noise levels, cooling, the safe removal of exhaust gases and service access must all be considered.
It is also critical that generators should comply with local environmental requirements relating to engine emissions and the bunding of fuel tanks. This information should be readily available from the manufacturer and precise environmental specifications should be submitted as part of the user’s requirement options.
Taking into consideration all these industry requirements, JCB have developed a range of 44 models covering 18 power nodes from 15kVA to 500kVA. The range is split into three types: 18 open generators, 18 canopy generators and eight rental models. All power nodes are available at 50Hz or 60Hz, and all units are supported by high-quality service and parts back-up.
Moreover, while many competitors still use analogue control systems, JCB fit digital control panels as standard across their range. The digital panel’s features include an event log, alarm list, real-time clock, maintenance call and engine ‘ECU–CAN’ support, including fault-code diagnosis. It can be operated remotely via a GSM modem connection – allowing the owner to monitor use and performance of the generator anywhere in the world, and protecting their investment against possible abuse and potential downtime.
In addition, the models from 50kVA to 110kVA output use the record-breaking JCB Dieselmax engine as their platform and can operate on 20% biofuel. JCB say this commitment to high-quality componentry is continued throughout the entire range with the company’s engineering hallmarks of build quality, design innovation and structural durability all integral to the overall design.