Lets Talk!
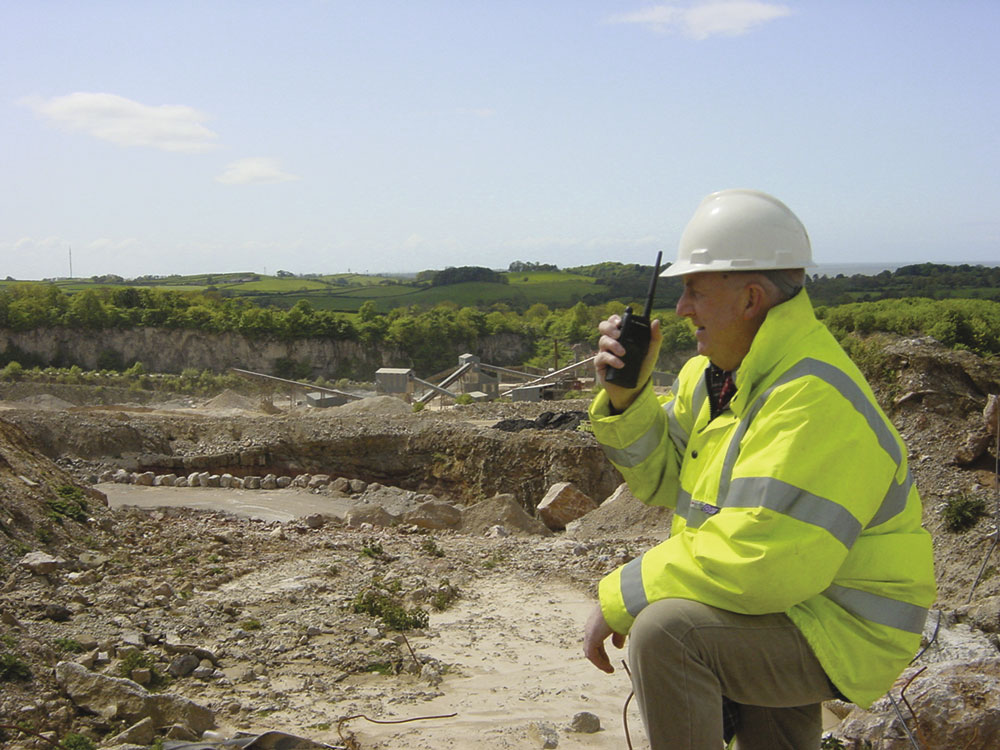
The author, Bill Rowlandson, is business manager with InTouch Ltd
Choosing the correct radio-communication system
Those who have been in the quarrying business for a number of years will remember the procedures for ensuring the safety of employees and the public during blasting operations. This was no more sophisticated than dispatching trustworthy employees to the furthest (and indeed the nearest) points of the quarry with various coloured flags, along with the sounding of what was probably an ex-wartime air-raid siren to warn that blasting was imminent.
This was a suitable procedure in its day. With the increasing emphasis on health and safety of employees, however, today’s quarry manager relies heavily on a good radio-communications system with complete coverage throughout the site and without any interference that could lead to confusion and danger.
Communications between foreman, manager and workforce are also essential in ensuring that operational problems are speedily reported and dealt with in a cost-effective manner in order to keep the plant at maximum efficiency, with fitters being summoned quickly to deal with problems. It is advisable that fitters have access to a second frequency on their radios so that they can start and stop machinery without being interrupted and distracted by the general chatter on the radio.
At most sites there are groups of people who have particular messages to pass on as well as information to receive. An example of this is the almost continuous dialogue between the weighbridge operator and the stockyard wheel loader driver, about which lorry needs to be loaded with what and where. This is a vast improvement on the old situation of lorry drivers getting out of their vehicles and wandering around stockpiles looking for the wheel loader driver, which carried a high risk of accident and injury. CB radios are often used between weighbridge operator, wheel loader driver and lorry driver, but this is often seen as a gossip channel and can lead to information from within the quarry being picked up by external parties many miles away. This leaking of information can be, and often is, detrimental to the quarry and could lead to loss of business. It should be noted that the use of CBs is prohibited in many quarries, as is the use of mobile phones, and that the legislation relating to the use of hand-held mobile phones does not apply to two-way radio systems.
A supplier who can provide a full radio system, undertake site surveys, give advice and assistance, deal with initial licensing and subsequent renewals, together with any dealings with OFCOM, is recommended. Until 31 December 2003 all radio licensing issues were dealt with by the Radiocommunications Agency, which was part of the Department for Trade and Industry. Since then, all the functions of radio and telecommunications, including mobile phones and television, have been dealt with by OFCOM (The Office of Communications). On inception, OFCOM gave Scotland and Wales their own national offices, in Glasgow and Cardiff respectively. England was divided into two, with offices in Haydock, Lancashire, covering the north, and Whyteleafe in Surrey covering the south; offices in Belfast cover Northern Ireland and the Isle of Man. From its inception, OFCOM reduced the number of administration staff but kept field technical engineers at their former strength.
OFCOM have radical plans for radio licensing in the future and are introducing ‘spectrum trading’ where licences now have a value in the marketplace. This enforces the need for licences to be dealt with as part of a radio system, so that suppliers can keep customers up-to-date at all times with OFCOM’s plans and proposals.
In the extractive and added-value industries, it is essential that systems are simple and effective. They need to give interference free total site coverage, with add-ons provided where necessary. The whole package must also be cost-effective and flexible for all users. Without these parameters being met, the whole issue of radio communications can become ineffectual and expensive. With flexibility, service and customer satisfaction in mind, along with the radio system being paid for as earnings continue, it is clear that renting a radio system can be the best option. By renting customers receive total commitment from suppliers who can resolve issues that customers might not have the time or expertize to deal with. This is a huge benefit for customers compared to a supplier who is only interested in selling radios, isn’t bothered about follow-up service and who only wants to sell more units when the original radios have become inefficient.
Suppliers who offer a complete package, starting with a site survey, followed by licensing, supply and subsequent back-up, will provide peace of mind, along with a flexible system where radios can be added, or reduced, as business dictates.
Customers should be advised by a supplier at the time of their initial visit, particularly at a greenfield site, whether a system will operate back to back, or whether a talk-through system would be advantageous, particularly where there is a geographically difficult area and where a much wider area of coverage is required. A battery back-up for a talk-through base should be provided so that if mains electricity is lost it will continue to work for a period of time. This is important both from a health and safety point of view and also operationally. The length of time the battery will work for is down to the level of use of the system and battery capacity — the larger the battery, the longer the ability to talk. Suppliers will calculate the battery capacity necessary in order to comply with a customer’s requirements. They will also advise on whether hand-held radios, fixed-base radios in buildings or fixed mobile radios in mobile plant are the most cost-effective method relative to health, safety and operational issues. For instance, it may be better to provide a primary crusher operator with a hand-held radio rather than a fixed radio in the cab as this will allow him to remain in contact with the rest of the workforce at all times, even if he has to leave the cab to attend to a problem.
Lone-worker systems are designed to protect employees or contractors working away from the rest of the workforce. They range from a simple audible warning that is transmitted to all radios on site, indicating that a worker is in difficulties, to radios with LCD displays that immediately identify the worker in trouble and their location; these are particularly useful on larger sites where workers are spread over a wide area.
Drivers of mobile plant (wheel loaders, dumptrucks etc) are usually provided with radios that have a fixed microphone that they have to disconnect from a clip and then have to re-clip after use. As an alternative, fixed radios provide drivers with a microphone at sun visor height along with a press-to-talk button that can be placed on the armrest or near the bucket controls. It is important to give drivers an input into the location of the button so that they are happy that it will not interfere with, but will be beneficial to, their control of the machine. Increasingly, sites are taking advantage of this type of equipment, which will fit any radio and can be quickly and simply installed by relatively unskilled labour.
Second, third and even fourth frequencies may be necessary at some locations, perhaps where rail loading or off-loading is being undertaken or where there is a need for groups of users to talk to each other away from the main frequency. This can prove to be very cost-effective because instead of applying for a separate on-site licence for each frequency at a cost of £75 a year, use can be made of a UK general licence that is held by the company at a cost of just £60 for three years. This provides frequencies that can be used anywhere within the UK, provided that no radio on that frequency is fixed in a static location. Additional equipment such as carrying cases, earpieces and lapel speaker microphones can also be provided by suppliers who will give advice on what is new on the market to help companies and their employees to work better, safer, and more comfortably.
The best option available is a flexible rental package with hand-held radios being replaced, in general, every two years, as they are the one piece of equipment that suffers the worst wear and the greatest deterioration in performance. Systems should be provided to suit the customer’s requirements at the lowest possible cost, while providing the highest possible back-up when needed. Suppliers should also be able to manage any licence problems and deal with coverage issues as sites expand and increase in depth.
Radio systems from the right supplier and with the right package can offer great benefits to all aspects of the extractive industry. The right supplier will also keep a client up to date with upcoming developments to keep them at the forefront of their business.