Volvo CE now using low-carbon material in serial production
Company implements use of low-carbon-emission steel in serial production of articulated haulers
AS part of efforts to reduce carbon emissions across every area of their business, Volvo Construction Equipment are now, for the first time, implementing low-carbon-emission steel into serial production of all their articulated haulers built in Braås, Sweden.
The announcement was made as part of the company’s biggest articulated hauler launch to date, delivering a new range that will help customers reduce emissions through an improved product carbon emission footprint, enhanced fuel efficiency, and smart solutions.
The introduction of low-carbon-emission steel is part of the company’s holistic approach to ongoing carbon emission reduction, addressing both a machine’s operation and the materials it is made from. With steel being a major component in their products, the gradual shift will be contributing to Volvo CE’s ambition to reach net-zero greenhouse gas emissions by 2040.
Conventional steel is a heavy emitter – and, as one of the main components in Volvo CE’s products, critical to reducing carbon emissions. Steel makes up approximately 60% of Volvo articulated haulers’ total mass and accounts for more than 50% of the machine’s total carbon footprint in the cradle-to-gate scope*.
As part of this transformation, Volvo CE were the first in the world to showcase a concept hauler built using pilot deliveries of fossil-free steel and a type of carbon-emission-reduced steel, in partnership with Swedish steel manufacturers SSAB in 2021. The following year, Volvo CE became the first to hand over a construction machine built using fossil-free steel to a customer, demonstrating the fast-tracking of innovation into real-world solutions, as companies across the value chain come together to drive change.
And now Volvo CE has entered the next phase of their continued exploration into low-carbon materials by implementing low-carbon-emission steel into the serial production of their full range of articulated haulers in Braås, Sweden.
While the two steel alternatives are produced with close to zero fossil carbon emissions, with production powered by fossil-free electricity and biogas, the key difference is that the fossil-free version is based on iron ore, whereas the low-carbon-emission steel is produced using recycled steel.
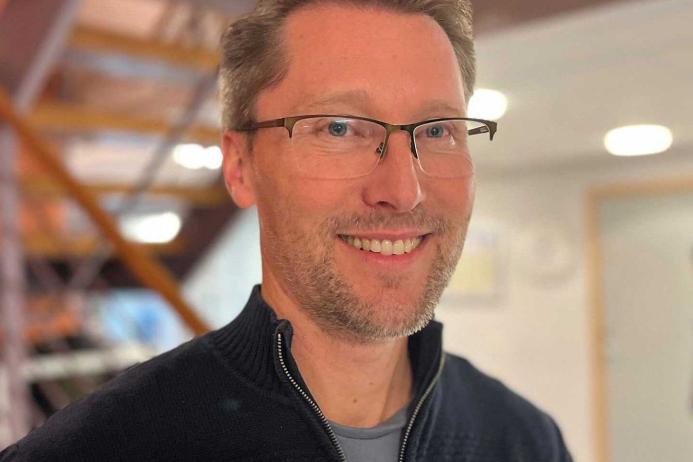
Rickard Alm, head of Volvo CE’s Life Cycle Assessment (LCA) programme, said: ‘We are proud to lead the way in the industry and move forward towards minimizing our climate footprint across the entire lifecycle of our products. While emissions from product use represent the vast majority of carbon output in our industry, it is important to also act to cut emissions in the production phase, including materials like steel, in close collaboration with our global supply partners.’
In the initial phase, around 13% of the total mass of steel in all articulated haulers manufactured in Braås is now replaced with the low-carbon-emission steel – a number that is set to increase as availability of the low-carbon material increases in collaboration with the company’s supply chain.
With this change, Volvo CE is able to reduce total CO2 emissions by around 13,000 tonnes annually, or more than 5%, in the cradle-to-gate scope. As an example, for an A40, this represents a reduction of nearly six tonnes of CO2 emissions.
No stranger to pioneering new ways of working for the benefit of the environment, Volvo CE Braås was also recently the first of the company’s facilities to reach Climate Efficient Site status. And in 2014, it became the company’s first carbon-neutral premises, as well as the first construction equipment production facility in the world to be powered entirely by renewable energy.
*Cradle-to-gate describes the environmental impact of a product from raw material extraction to the point it leaves the manufacturing site.