Two new cold planers from Cat
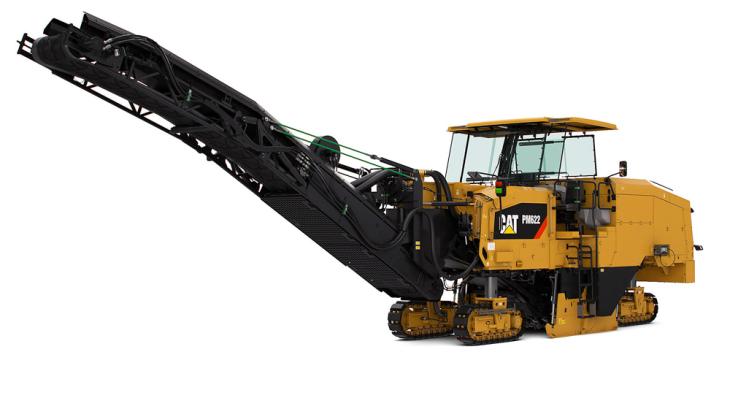
High-performance PM620 and PM622 milling machines offer full-depth removal in single pass
CATERPILLAR have introduced the PM620 and PM622 cold planers – two new high-production, highly manoeuvrable half-lane milling machines designed to perform controlled full-depth removal of asphalt and concrete pavements in a single pass.
The operating weight of the PM620 is approximately 33.3 tonnes while the PM622 weighs in at around 33.9 tonnes. Transport weights are approximately 29.4 tonnes and 30.0 tonnes respectively.
Both machines are powered by a Cat C18 ACERTengine – a turbocharged, 6-cylinder diesel unit that provides 470kW (630hp) of gross power and meets US EPA Tier 4 Final and EU Stage IV emission standards.
The machines are fully hydrostatically driven and four-mode steering is standard. In co-ordinated mode, inside turning radius is just 2.0m (6ft 5in), providing exceptional manoeuvrability in confined spaces. A true-tracking alignment function provides greater steering precision, smoother cornering and reduced track wear.
The operator’s station features dual operating controls, including joystick steering/propel lever, upper conveyor controls and rear track steering controls, and the ergonomic instrumentation layout has been designed for comfort and ease of use.
The touchscreen display provides easy-to-read gauges, function indicators and warning indicators to keep the operator informed of machine operation and vital systems. It also displays video from the optional front/rear remote cameras.
The cutting chamber has been designed to streamline material flow and reduce wear on the chamber, and has enhanced flush cutting capabilities. The rotor drive system features a dry clutch driving a planetary gear reducer, for efficient and reliable application of rotor power to the pavement.
The PM620 is equipped with a 2,010mm (79in) wide high-production rotor and the PM622 with a 2,235mm (88in) wide version. The maximum cutting depth is 330mm (13in). The rotor is equipped with durable three-piece, quick-release tool holders and carbide-tipped cutting bits. Optional Cat Diamond Bits are available for greater cutting performance in particular applications.
Both machines can be equipped with integrated Cat Grade Control. The 2D-capable/3D-ready grade and slope system automatically controls rotor depth and cross slope to a pre-set cutting depth, and can be enhanced for full 3D control with the addition of optional equipment.
The hydraulically driven, seamless, 850mm (33.5in) wide collecting conveyor features 32mm (1.25in) high cleats for effective clear-out of the cutter box, whilst a standard water spray system lubricates the conveyor belt and helps control dust, and an additional water spray system can be fitted as an option for greater lubrication, cooling and dust reduction in heavy-duty applications.
The hydraulically controlled, variable-speed front loading conveyor features height adjustment and 60°swing to the left and right of centre. It is equipped with upper aluminium covers for added protection against material spills and dust emissions. The loading conveyor can also be hydraulically folded downwards, reducing machine dimensions during transportation.
Optional equipment includes a self-powered canopy, a dust-abatement vacuum system, a high-pressure wash-down system and an electric refuelling pump.
For serviceability, large doors open wide to provide easy access to the engine, emissions package, air filter, hydraulic components and daily service points. The hydraulic rotor service door also opens wide for convenient access to the rotor for inspection and tool maintenance. An optional rotor-turning attachment is available to turn the rotor during cutter bit replacement.
Other features that simplify service include leak-resistant O-ring face seal hydraulic fittings, grouped quick-connect hydraulic test ports, scheduled oil-sampling ports, visual sight gauges and remote grease points.