Top-hammer efficiency in the Highlands
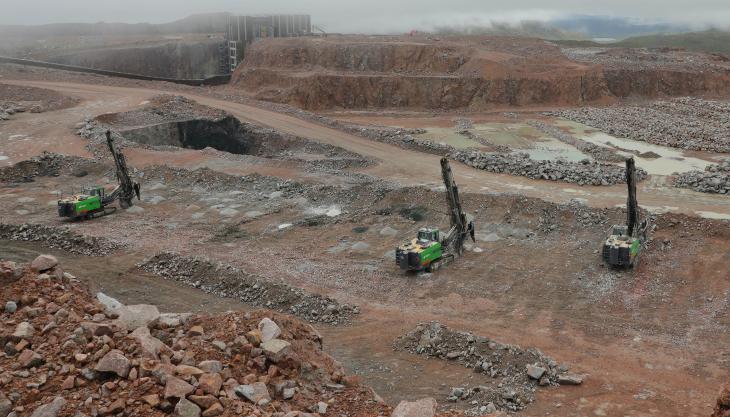
Epiroc drilling and blasting technology helps BAM Ritchies boost productivity and efficiency at Glensanda
SWITCHING to the SmartROC C50 top-hammer drill rig has increased productivity and made drilling accuracy much easier at Glensanda – the largest granite quarry in Europe.
Situated in the Scottish Highlands on a mountain rising from the shore of Loch Linnhe, the quarry is perched 520m above sea level and around 1km inland to minimize its visual impact. It has been in operation since 1986 and produces around 7 million tonnes of aggregate per year, with reserves that are expected to last at least until the year 2100.
Glensanda is owned by Aggregate Industries but the drilling and blasting operations are subcontracted to BAM Ritchies. ‘We’re nine people in the quarry and produce about 130,000 tonnes per week working one shift per week-day,’ said Jonathan Will, blasting engineer with BAM Ritchies.
‘A few years ago, we switched over to SmartROC C50 and T40 top-hammer drill rigs. Switching to modern, technically advanced rigs with a high degree of automation and GPS capabilities has made a world of difference.
‘Take the C50, for example – it’s far more efficient than the old L7 we used to have. We’re saving 47% on fuel compared with the former rigs and Epiroc have increased the service life of the hammer by 50%.
‘It’s easier to adjust the airflow, which saves the drill bits and has measurably increased the lifespan of the consumables. The C50 has achieved a 40% increase to the lifespan of the outer steels which reach around 20,000m, and a nearly four-fold increase to 90,000m for the inner steels,’ said Mr Will.
Gary Stewart, an operator of the SmartROC for BAM Ritchies at Glensanda, commented: ‘The C50 is far better on fuel and on the drill steels, and it’s a lot comfier. It’s a nice environment in the cabin, which is good since I spend the majority of the working day inside it.
‘The RCS4 screen is a lot bigger and easier to use and gives you much more information. I can control more from the cab rather than having to walk round trying to find problems. I start the top of the hole manually. When I’m satisfied it’s going well, the automatic drill control will drill the rest of the hole.
‘When, for some reason or another, we can’t drill at the marked location, the machine will calculate a new angle, azimuth and depth. The bottom of the hole will be in the proper position, even if the top is a couple of meters to the side.’
The drill plan for the drilling and blasting operations at Glensanda is created by scanning the rockface, marking the planned holes, then saving the data to a memory stick which is plugged in and uploaded to the SmartROC rig. The rig then drills the holes at correct angles, azimuths and depths, and saves all drill data so it can be used when planning the charges for the blast.
‘The rig collects a lot of data about, for example, rock quality when drilling,’ said Mr Will. ‘This is a huge benefit to us when we plan future blasts.’
GPS functionality has also made a great difference to the efficiency of the shots. Not having to manually estimate where to drill or make corrections has helped BAM Ritchies to maximize the burdens and spacings on shots, increasing production.
‘We’re high up on a mountain above the sea. About 30–40% of the time we have really bad mists with visibility of 3–4m. Previously, we lost a lot more time due to the weather conditions and surveying but now we can do everything from the cab without putting the operator at risk,’ explained Mr Will.
‘In the winter there’s lots of snow, and this is when the GPS really comes into its own by letting us drill at the proper location right through the snow cover. This has made a huge difference in productivity,’ he added.