Thompsons launch the Paymaster
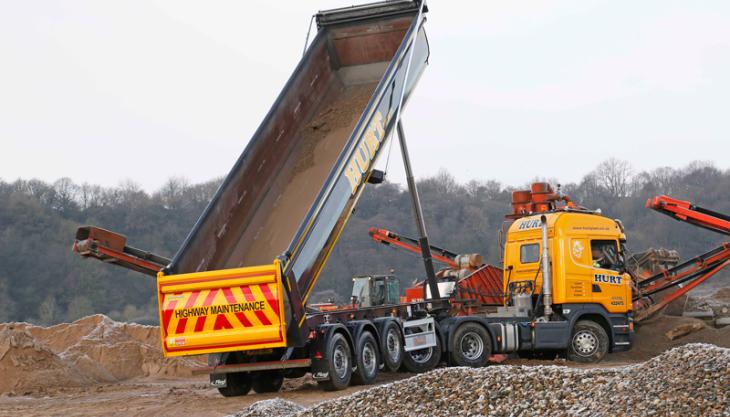
UK bodybuilding specialist kicks off 2016 with the introduction its first production tipping trailer
THOMPSONS, the UK’s leading tipper bodybuilders, have begun 2016 with their most significant new product for many years – their first production tipping trailer.
Called the Paymaster, the new trailer has been designed with one key objective – to allow tipper operators to carry up to 50% more payload than an equivalent 8x4 rigid. In practice, Paymaster will carry an additional 10 tonnes of product over an eight-wheeler.
Designed for full multi-purpose operation with a wide variety of payloads, Paymaster’s chassis and body are both made from steel. The chassis, an advanced lightweight design that is tapered towards the front, is built by Fliegl of Muhldorf, Germany.
The single-skinned body, made to Thompsons own design to complement the chassis, is made from Hardox 450 – the standard material for Thompsons’ market-leading Loadmaster Lite rigid bodies.
Together with its curved floor designed for the cleanest possible load ejection, other key features of Paymaster body include a 9.8m internal floor length, 1.3m high single-piece sides, automatic tailgate, front-to-back electric sheeting, on-board weighing and an Edbro CS17 tipping gear.
On the chassis, the SAF running gear comes with full air suspension, disc brakes and a lifting front axle.
Thompsons say Paymaster has been introduced with a particular focus on quarry operators and general hauliers wanting extra efficiency and productivity in moving large volumes of stone and aggregates, yet who could also use a tipping trailer for a variety of other uses.
Such built-in versatility, say Thompsons, can only come from a steel/steel chassis and body combination where strength, durability and long-term reliability are effectively built in from the outset.
Complete with sheet and ready to run, the new trailer weighs a competitive 7,380kg. Allowing for a 6x2 tractor weighing some 8,500kg, payload is comfortably over 28 tonnes, thereby achieving the required 50% bonus over an eight-wheeler.
Scott Burton of Thompsons commented: ‘Tipper operators have been asking us for some time whether or not we will do a trailer – and now we have. With Paymaster, we’re focusing on the mainstream market sector where Thompsons are already strong – general-purpose tipping with steel-bodied vehicles.
‘Paymaster simply adds to our existing product portfolio, allowing Thompsons to offer customers the broadest choice of bodywork in the industry. More and more, we see that tipper operators are wanting not just rigids or just trailers, but both. By introducing Paymaster, Thompsons can now meet their needs precisely.
‘With Paymaster, we have made particular effort to provide the most advanced and productive chassis and bodywork combination possible. And just like every Thompsons product, Paymaster is built to all our industry-leading standards of quality, fit and finish. As a result, minimal cost of ownership and long-term value are assured.’
The first Paymaster trailer has just been put into service by Hurt (Plant Hire) Ltd of Preston. Now part of a highly varied fleet, the new tipping trailer also allows Hurt’s tractor units to keep working when not delivering plant equipment on low-loaders.
As a long-established Thompsons customer, Hurt’s manager, Ian Coulton, commented: ‘Whilst our 8x4s with their Loadmaster bodies will remain at the core of the fleet, the Paymaster trailer will undoubtedly add to our overall operating versatility and efficiency. When both the loading point and delivery point are acceptable, it makes total sense to use a trailer that can carry an extra 10 tonnes of material.’
He added: ‘In every way, Paymaster is another top-quality Thompsons product and we are delighted to have the very first. We expect it to be a high performer for many years to come.
‘Another key point is that the operating cost of an artic tipper is very similar to an 8x4, as indeed is the capital cost to purchase it. So simple mathematics says that the Thompsons Paymaster is an ideal product for today’s difficult economic climate.’
Thompsons’ sales manager, Ian Chaplin, added: ‘Even making just two trips a day, Paymaster is carrying an extra 20 tonnes of product. So that’s at least 100 tonnes more per week, or an extra 5,000 tonnes per year. In the right operating environment, this is a simply enormous productivity bonus.’