Screening upgrade at Norton Bottoms Quarry
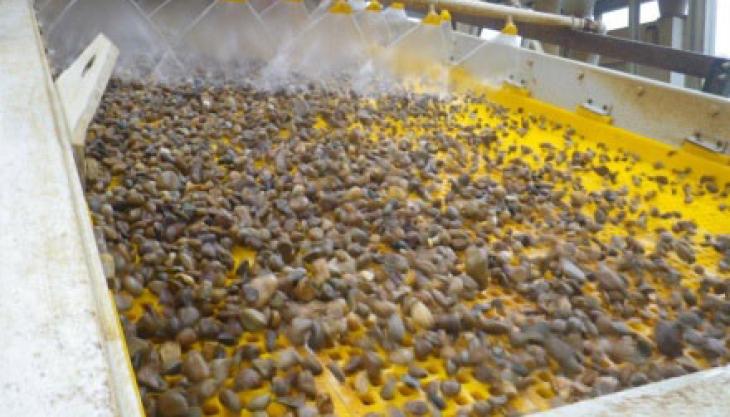
Tema Isenmann increase efficiency of screening processes at key Lincolnshire sand and gravel site
OPERATIONAL for the last 30 years, Norton Bottoms Quarry, close to the village of Norton Disney in Lincolnshire, has been owned and operated by Breedon Aggregates since 2011.
The quarry supplies high-quality sand and gravel with the majority of its production going to Breedon’s concrete plants in North and South Lincolnshire, and the rest to local markets.
Due to its age and Breedon’s desire to improve process efficiency at the site, the plant has recently been upgraded. As part of this upgrade, Measham-based Hewitt Robins supplied two screens which were installed by Roltech Engineering of Newcastle-under-Lyme.
A new 2.5m x 6.0m long inclined double-deck washing screen (pictured) gives a separation of 20mm and 4mm through WS85 polyurethane modules supplied by Tema Isenmann. Rated at 350 tonnes/h, the screen utilizes 120 cubic metres of water per hour and is fitted with spray bars featuring a combination of Tema Isenmann standard mini fan sprays and mini flood sprays.
The second new screen is a 1.8m x 4.8m long low-angle dewatering model fitted with Tema Isenmann WS85 polyurethane screen media with 0.5mm x 12mm slots. This screen is rated at 200 tonnes/h and processes –4mm sand, achieving a final moisture content of 7–10%.
Operations manager Carl Ashurst commented: ‘With a 30-year-old plant and obvious limitations, we decided to completely replace the processing element and subsequently installed a main conveyor, double-deck washing screen, dewatering screen and removed the old barrel. All the material is now processed in an MEP sand plant, which allows us to pick and choose whether we make concrete sand or mortar sand.’
Mr Ashurst added: ‘The washing screen was designed to take 350 tonnes/h, which includes raw material that comes up from the field as well as any recirculation that comes through the two crushers, giving us anything between 200–250 tonnes/h of finished product.’
Installed during a transition period whilst still operating the old plant, the new equipment was then interfaced during a two-and-a-half week shutdown to complete the installation.