Sandvik VSI aids manufactured sand production
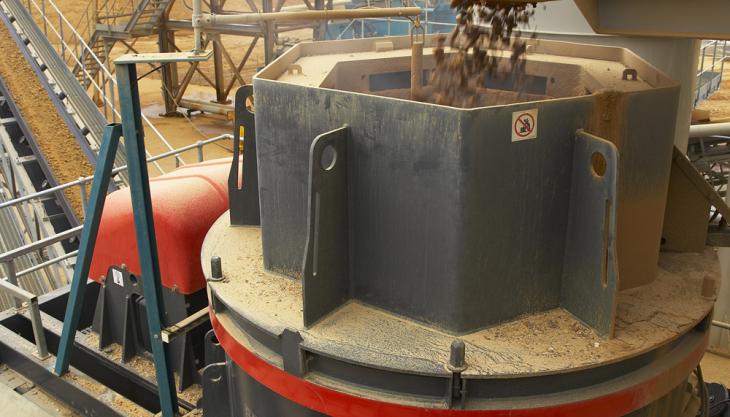
Tarmac benefit from installation of new CV216 vertical-shaft impact crusher at Blashford Quarry
TARMAC have taken delivery of one of the latest vertical-shaft impact crushers from Sandvik Mining and Construction for use in the production of high-quality manufactured sand products at Blashford Quarry, in Hampshire.
The CV216 crusher, which is part of Sandvik’s six-model CV200 series, has been primarily designed to operate as a third- or fourth-stage crusher, making it to be ideal for Tarmac’s manufactured sand application.
The CV200-series machines have been developed to ensure consistent product shape and size, while offering reduced power consumption, increased capacities and reduced maintenance costs.
Sandvik’s patented autogenous ‘rock-on-rock’ crushing technique is said to result in several major advantages in the production of manufactured sand, with perhaps the most important for Tarmac being the consistently cubical product shape.
Moreover, the application of rock-on-rock action for breakage means the CV216 uses fewer wear parts, which in turn means fewer spares need to be bought during the operational life time of the machine, thereby maximizing Tarmac’s investment.
The CV216 has seamlessly fitted into the production process at Blashford Quarry, where the gravel feed material is initially screened after primary and secondary crushing in order to eliminate –10mm and +70mm materials. The remaining –70mm +10mm material is then washed to remove any existing contaminants, such as clay or lignite, before being fed into the CV216.
The end result is a sand product that not only possesses the desired cubical shape for use in the manufacture of concrete, but is also very clean and contaminant-free.
An additional benefit of Tarmac’s new VSI is its low environmental impact. Like all CV200-series machines, the CV216 utilizes Sandvik’s patented Bi-Flow system and high-performance rotors. These are used in conjunction with second-generation wear parts that result in significant power reductions, yet are capable of producing higher tonnage throughputs.
As a result, up to 20% of the maximum crusher throughput can be effectively handled through the Bi-Flow system, producing significant savings in electricity costs and reducing Tarmac’s CO2 emissions per tonne.