Revolvo manufacture special undersize bore bearing
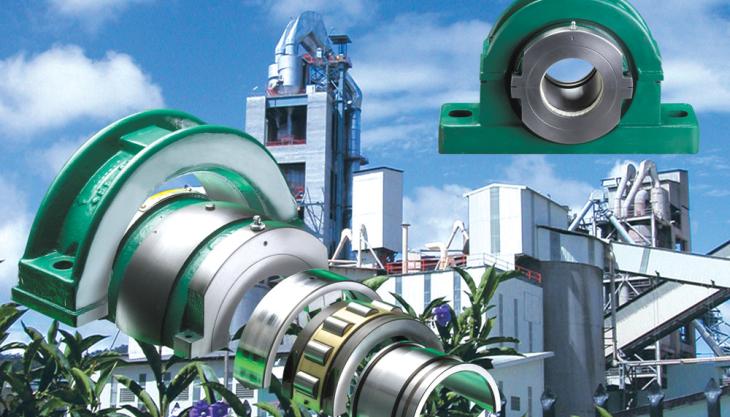
Continuing their recent success in providing large split roller bearings for use in ball mills, Revolvo have won an order from a cement plant in Thailand to supply two large split roller bearings worth a total of £40,000. One is a standard 850mm bore unit and the second is a special 849mm bore bearing to cope with an undersize shaft.
Revolvo won the order because of their willingness to manufacture the special size bearing, and due to the overall design of their SRB unit featuring a brass cage instead of an aluminium cage, which was considered more durable in the demanding conditions.
The two SRB bearings, which are being used in a ball mill to crush limestone (the rock actually being fed through the bore of the bearings), are replacement units for aluminium-caged split roller bearings that have been failing for some time. The problem with replacing these units has been the issue of an undersized shaft. Both bearing shafts should be 850mm but, due to wear and tear, one shaft is now 1mm undersize at 849mm. This meant that the user either had to replace the shaft completely – a time-consuming and costly undertaking – or find a supplier to manufacture a special replacement bearing.
It was a chance visit to the Revolvo website that brought the solution, as in addition to their standard sizes, Revolvo manufacture non-catalogue bearings in sizes up to 1,500mm. These ‘special’ bearings are used extensively in process and extraction industries worldwide.
In common with all Revolvo’s SRB bearings, the Thailand units are being supplied with machined brass cages. Revolvo’s cage design has CNC-bored pockets that are optimized to give very accurate roller guidance, which prevents skewing – a condition that can lead to edge loading on the bearing and reduced bearing life.
In addition to providing accurate roller guidance, the brass cage allows operation at higher temperatures (up to 140°C) without problems, and up to 25% higher operating speeds, as long as thrust loads are within design limits. Overall, brass is said to be one of the best cage materials, as it absorbs lubricant and performs well in aggressive environments where lubrication is marginal.
The ability of SRB split roller bearings to perform reliably in aggressive cement applications is enhanced by the performance of the sealing systems available to protect the cartridge bearing units. Revolvo have developed a special labyrinth seal to exclude fine, abrasive and hygroscopic cement dust, which is a major problem for equipment, such as screw conveyors, in cement plants. This solution provides much improved bearing reliability and longer life with greatly reduced levels of maintenance.