Removing a tunnel step-by-step with Kemroc attachments
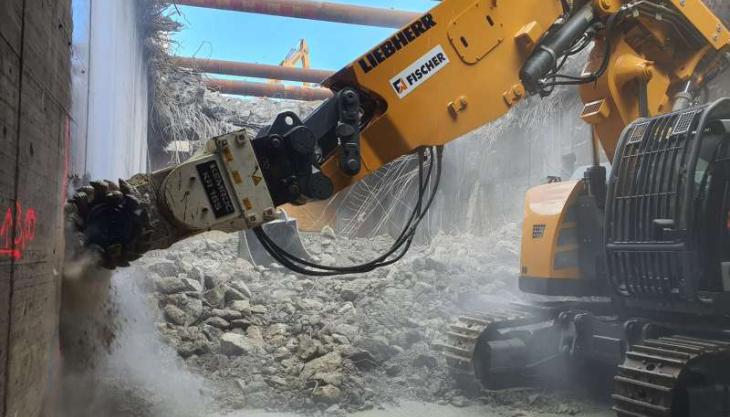
Tunnel demolition project in Stuttgart presented unique engineering challenge for Fischer Weilheim GmbH
A CIVIL engineering team at Fischer Weilheim GmbH has developed a new, economical step-by-step methodology for the removal of thick concrete tunnel lining in a tram tunnel in Stuttgart, Germany.
As a part of the city’s Stuttgart 21 railway redevelopment project, numerous tunnels have been earmarked for excavation, while several other existing tunnels will be modified, including Schillerstrasse, where a passageway connecting the new Staatsgalerie tram stop and Klettpassage (Hauptbahnhof station) is being rebuilt.
One of the most challenging aspects of the new redevelopment was modifying a 120m stretch of the existing tunnel. The initial phase was to gradually remove the crown of the tunnel and take out the lining at floor level while, at the same time, supporting the opening with the installation of ironwork.
Demolition work proceeded by removing material from the top and bottom of the tunnel; achieved via a hydraulic excavator equipped with breaker and shear cutter attachments. However, progress was made difficult than usual when the engineering team had to remove the wall lining of the tunnel, which had a bituminous sealing layer and brickwork between the concrete lining and outer soil.
Using the conventional method of an excavator and breaker attachment, Fischer Weilheim found that it was impossible to prevent the three layers becoming mixed together. During this demolition phase, the contractor approached Kemroc to help develop an innovative method to remove the tunnel walls into segments.
The engineering team at Fischer Weilheim decided to use a rental Liebherr R950 tunnel excavator equipped with a breaker, a shear and two Kemroc cutting attachments as the strategic choice of equipment for reliability and productivity in this tunnelling application. With these tools and attachments, the walls were divided into single 4m to 6m wide sections which were later torn down and processed.
In removing the concrete tunnel lining, the first step was to reduce the thickness of the tunnel lining to around 100cm using a Kemroc KR 165 rotary drum cutter. A Kemroc DMW 220 1000 cutter wheel was then used to cut through the last 100cm of the wall. In some sections, the heavily reinforced concrete tunnel lining was up to 160cm thick and these had to be grinded back to the cutting depth of the cutter wheel attachment.
These two steps were repeated for cutting a number of horizontal slots, ultimately dividing the tunnel lining into various segments. The next stage was to use a breaker to weaken the segment of the wall before pulling it down using the excavator-mounted bucket.
According to Christoph Fischer, a fourth-generation partner at Fischer Weilheim, removing the tunnel lining in segments step-by-step was crucial in delivering the required increased productivity on the tunnel demolition project. ‘It was clear that this was the most effective and economical method for the demolition and separation of material in the tunnel lining,’ he commented.
‘We doubled the expected production rate when compared with the single use of hydraulic hammers, since it is logistically challenging to gain full productivity from an excavator with breaker in a confined space of a tunnel. Once each segment was torn down to the tunnel base, it was much easier to break them down using the hydraulic breaker.’