New Superior tooth jaw plates add value for G.F. Job
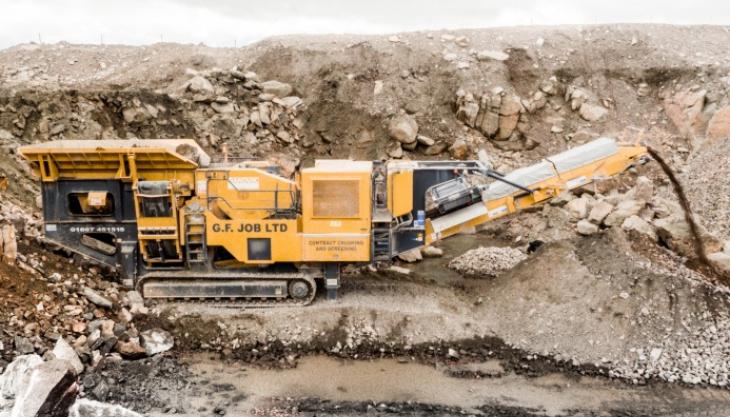
Scottish contract crusher benefits from new Sandvik designed and manufactured jaw plates
BASED in the Scottish Highlands, G.F. Job Ltd are one of the first companies to have trialled the new Superior tooth jaw plates designed and manufactured by Sandvik.
Formed in 1990, G.F Job currently employ 90 people and offer a comprehensive range of services ranging from earthmoving, civil engineering and heavy haulage to recycling and contract crushing.
Based in Nairn, near Inverness, the company owns five quarries and has a wide range of Sandvik mobile crushing and screening equipment, including four tracked jaw crushers.
One of the crushers, a Sandvik QJ341, is employed at a granite quarry for the majority of the year producing 500,000 tonnes of 5in crusher run to feed an aggregate processing plant.
With a keen interest in business efficiency and running the operation cost-effectively, G.F. Job have previously used a variety of different jaws to test their durability and performance.
On this application, both heavy-duty 20% square tooth jaws and conventional 14% corrugated jaws have been used, and a history of the tonnages produced by each jaw has been recorded to give an accurate account of performance in relation to costs. It was for this reason the company decided to trial the new Superior tooth jaw plates on this machine.
Based on customer feedback, Sandvik have developed a new profile of jaw plate, designed not only to increase durability and productivity, but also to decrease operating costs and service time.
The new Superior tooth jaw plate profile allows for a higher percentage of the jaw to be worn, which results in longer wear life and less manganese waste. The improved tooth profile also allows for better breakage and improved material flow, resulting in a more cubical product and a higher-quality product shape.
Following the trial at G.F. Job, Sandvik say the initial test data have been extremely encouraging. The average output increased from 200 tonnes/h to 250 tonnes/h, while wear rates increased by more than 30%.
G.F. Job’s plant manager, Graeme Watt, was delighted with the outcome. He commented: ‘In this particular granite application, previous jaw plates have been ranging between 20,000–30,000 tonnes of crushed material – and that’s the life of the jaws. Since we went on to this new jaw we’re up 50,000–55,000 tonnes for the life of the jaw. If you go into a limestone quarry, you’ll get double, but this is a hard abrasive material.’
In addition to the increased wear performance, G.F. Job have also seen benefits in fuel economy and improved product shape.
‘The new jaw plates are creating a better shape of product, but they are also crushing far more economically as well. By reducing the load on the crusher, we’re creating better fuel economy while also reducing the physical hardship on the machine,’ said Mr Watt. ‘Their unique design also makes the plates easier to turn over or replace, saving us time and money.
‘They benefit us all round: we are crushing far more, getting better fuel economy, producing a better product and they are lasting a lot longer. We will be looking to order additional sets for our other jaw crushers,’ he concluded.