New higher capacity split roller bearing
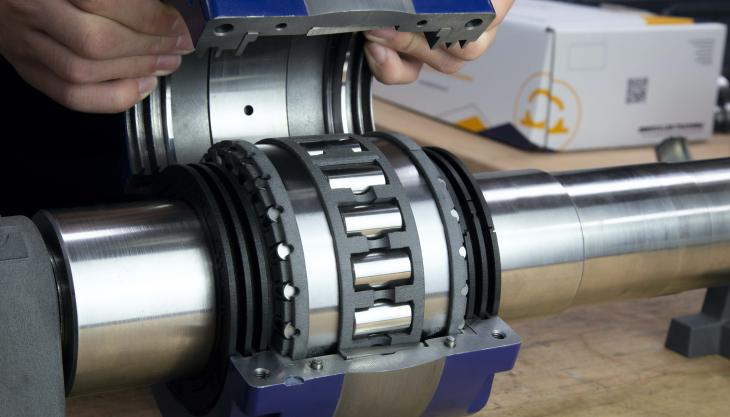
Bowman International say new Advanced Split Roller Bearing set to transform industry
GLOBAL bearings innovators Bowman International have launched a split roller bearing with substantially higher radial and axial load capacities than any other split roller bearing currently on the market.
Well suited to applications such as conveyor drives, head pulleys, take-ups and bend and snub drums, the new Bowman Advanced Split Roller Bearing is said to offer up to 75% higher radial load capacity and up to a 1,000% increase in axial load capacity in both directions.
Commenting on the significance of this innovation, Bowman’s technical director, Ian Breeze, said: ‘For the first time, plant manufacturers and maintenance engineers in the mining and quarrying sector can specify a split roller bearing that does not rely on race lips alone to accommodate axial force in high-load applications.
‘The new Bowman Advanced Split Roller Bearing comprises two independent 3D-printed axial bearings designed to accommodate greater loads, improving system performance with less maintenance and reduced unplanned machine failure.
‘In fact, compared with other market-leading split bearings, the Bowman Advanced Split Roller Bearing increases bearing L10 life by up to 500%.’
Further enhancing the performance of the new split roller bearing is a patented triple labyrinth extended seal which not only offers a tighter seal than other split bearings, but also reduces the need for costly removal, machining or replacement of worn shafts. Instead, engineers can simply fit an extended seal on to an undamaged part of the shaft, without compromising performance and without the need for extended downtime.
Thanks to its high thrust capacity and increased radial load capacity, this bearing can be specified to replace solid spherical roller bearings in rotating machinery, delivering up to 10 times faster bearing change times than previously possible for these applications.
‘When space is limited, engineers often need to disconnect the coupling and move other equipment, such as motors, gearboxes or pumps, out of the way before they can slide solid bearings off the shaft for replacement or maintenance,’ explained Mr Breeze.
‘Split roller bearings can be assembled radially around the shaft, eliminating these additional logistical challenges and making maintenance and replacement a lot faster and more cost-effective. To further enhance time and cost savings, the Bowman Advanced Split Roller Bearing uses the rollers to lock the two cage halves together, eradicating the use of small and easy-to-lose clips and other locking components.’
Alongside the significant increase in radial and axial load capacity, this new bearing design offers a range of additional installation and performance benefits, such as larger diameter screw sizes to accommodate increased capabilities for the clamp rings, cartridges and pedestals, and roller pockets with cavities to hold the grease against the rollers.
As part of the Advanced Split Roller Bearing portfolio, Bowman offer a range of dimensionally interchangeable retrofit products that fit directly into existing bearing housings, including those from competing bearing brands, to quickly and cost-effectively improve radial and axial load capacities. There is a choice of additional IoT-specific functionalities available and bespoke adaptations can be accommodated within fast lead times.
Mr Breeze concluded: ‘As proud innovators of bearing solutions that solve real industry issues, we are the first manufacturer to create a split roller bearing capable of increasing the lifespan and performance of high-axial systems and, thanks to the production benefits of 3D printing, we have been able to deliver this product to market at a price point up to 20% lower than other leading split bearings.’