New fee-based service initiative from SKF
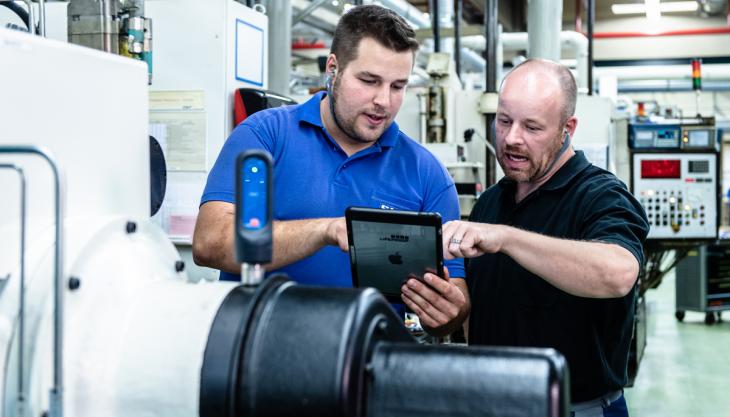
SKF urge users of rotating equipment to rethink the way they pay for bearings and related components
BEARINGS specialists SKF have introduced a new fee-based rotating equipment performance (REP) service that helps reduce waste in the supply chain and minimizes environmental impacts.
The after-sales initiative is said to contribute to the circular economy through the remanufacturing/recycling of bearings and the filtration and regeneration of lubricants. It also reduces material and energy consumption, thanks to longer-lasting components and increased machinery uptime.
According to SKF, in the traditional transaction-based model, suppliers’ profits depend on numbers of parts sold and not on improvements in machine performance. There is a fundamental conflict of interest, as longer component life means fewer sales for the OEM/supplier.
SKF have developed their forward-thinking, fee-based REP service approach to optimize the working life of a machine and ensure key measures are taken to reduce costly downtime, especially when unplanned plant equipment failure occurs. This, they say, is a step in the right direction, as both SKF (as a supplier) and their customers are benefiting from optimum machinery productivity, reliability and efficiency.
Under a REP contract, the customer pays a fixed monthly or quarterly fee dependent on SKF meeting agreed targets for machine production level, uptime or other KPIs. The all-inclusive fee covers provision of bearings, seals, lubrication and condition monitoring.
The company’s engineering expertise in this specialized area ensures the ideal specification and application of all elements, which is important as 90% of industrial bearings fail because they are wrongly specified, installed, lubricated or used.
REP can be applied to both long-established and modern equipment, including conveyor belts, pumps, crushers, railway bogies etc, and SKF experts are on hand to discuss the needs of the machinery and the business before proposing a solution. Importantly, the REP service initiative helps to bring the customer’s maintenance and production departments together, with a strong focus on uptime and output.
SKF say the scope for performance improvement through fee-based business models has been enhanced by digitalization. The company can provide inexpensive, easy-to-use condition-monitoring units and fully integrated automatic lubrication systems.
These connect with the SKF Cloud and the customer’s existing production management system to generate useful real-time data that can be acted upon remotely.
Entry-level hardware and software make it simple for any company to adopt a digital approach and solutions are scalable to suit all sizes of operation. If businesses lack the analytical expertise to make use of the data generated, SKF can provide the necessary job site or remote support. All systems are connected to SKF REP Centres, where data analysts and application engineers monitor 5 million bearings in real time.