New Delta II screen for Moons Hill Quarry
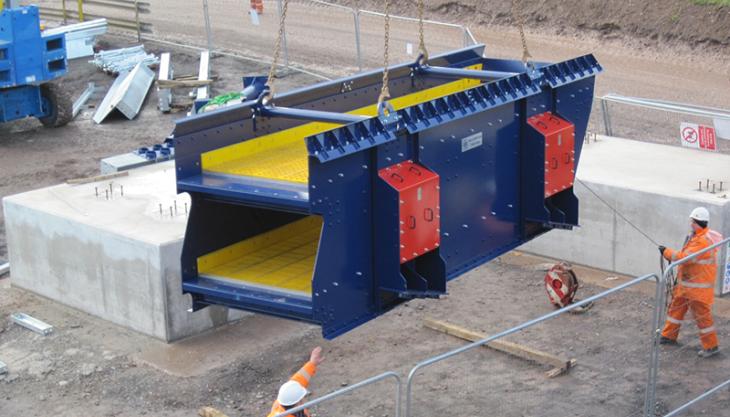
Tema Machinery supply John Wainwright & Co with high-energy screen for difficult basalt application
AS part of a recent major plant upgrade, Tema Machinery have supplied a Delta II intensive-action screen – manufactured by their German sister company Hein Lehmann – to John Wainwright & Co. Ltd’s Moons Hill Quarry, near Radstock, Somerset.
Last year saw Wainwright make their most significant investment in recent years, with some £3.5 million spent on new quarry processing plant at Moons Hill. This has taken the form of a new secondary-stage aggregate production plant to replace aging equipment, some of which had been in use since 1963, as well as bringing up to current standards the secondary and tertiary processing sections and linking them up with appropriate conveyors to the existing primary and final screening section.
Foundation works began in the Autumn of 2012, with the project completed and commissioned in October 2013. The new 20m high secondary plant, constructed by Devon-based Centristic, is said to be up to 60% more productive than the previous facility.
As part of this investment Tema Machinery supplied a new high-efficiency Delta II screen complete with WS85 polyurethane screen media. Prior to winning the order, Tema held numerous site visits to discuss the machine and its capabilities, and how it would cope with the site’s ‘difficult’ basalt raw material.
With anywhere up to 30% volcanic and clay fines within the basalt, when the material is in damp and poor condition it needs to be screened at a 40mm setting, but when the material is clean and fine there is a need to screen at 20mm, to optimize reclamation of the high-value stone and reduce the waste scalpings element.
Project engineer Peter Restorick commented: ‘We looked carefully at a number of options including the Tema machine concept as a high-resonance and high-action screen that would satisfy our needs. After supplying Tema Machinery engineers with test material (with positive results), two of our key personnel were invited to visit a similar application in Belgium and were very satisfied with the performance of the equipment.
‘It was obvious from the outset that the uniqueness of the computer-controlled synchronization of the two screen drives eradicates some of the traditional wear associated with trying to link two separate drive units together mechanically. The Delta II is certainly innovative and proved to us that it offered the best chance of recovering good material from the scalped element of the product.’
Mr Restorick continued: ‘The screen was installed by project contractors Centristic in a near-seamless operation. The machine is of excellent build quality and, after installation, initial operation was very straightforward. The German engineers were also very responsive when we needed assistance. Although we had some initial teething problems in setting up the software, these were quickly and easily resolved.
‘It was essential that we maximized the efficiency and output of the new plant. The main criterion behind the selection and purchase of the Delta II screen was recognition that we were losing an element of the product in the scalpings that could be recovered and put through the cone crushers, thereby maximizing the amount of reserve we were utilizing. The Delta II has provided us with the means to achieve this.’