Metso introduce the Nordberg NP13
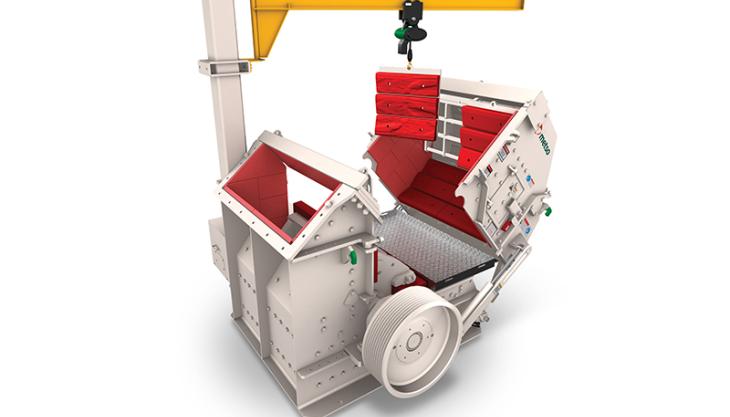
New impact crusher offers increased efficiency and safer and easier maintenance
METSO have introduced the new Nordberg NP13 impact crusher – the newest addition to their field-proven range of NP-Series impact crushers. Designed for increased safety and performance, Metso say the NP13 is well suited to secondary and tertiary applications and features the same design as the recently launched NP15, but for smaller capacity requirements.
‘Performance, profitability and maintenance of the crushing plant are at the heart of this new crusher,’ commented Vincent Schmitt, Metso’s product manager for NP-Series impact crushers.
To improve crushing efficiency and produce more end products with less recirculation load, the NP13 features a steeper feed angle. This increases material penetration into the rotor and makes the discharge curve less sensitive to blow bar wear, ensuring more consistent end products over time without having to change blow bars.
The NP13 accepts feed material up to 350mm (14in) and can be equipped with a 315kW (400hp) motor on a single drive. Its maximum throughput capacity is up to 20% more than that of the existing NP1213, and it can be installed on a lighter steel structure.
Moreover, the number of different side liners has been cut by nearly half compared with the NP1213. The new machine only requires seven different liners thanks to a clever wear part arrangement means more flexibility in the use of the side liners and less need for parts in stock.
Also, thanks to Metso IC crusher automation, which provides accurate control of the crusher parameters, the NP13’s product quality is said to be both predictable and consistent, resulting in improved plant profitability.
A wide selection of blow bars ensures that customers always have the right tool, regardless of the abrasiveness of the crushed material. Metso say their triple-wedge blow bar attachment system is the easiest on the market and provides a very rigid assembly that allows the use of blow bars with ceramic inserts, even with coarse feed material.
To make maintenance safer and easier, the NP13 has a new two-part rear frame that combines safety with easy, wide access. The operator can choose which way to open the frame, depending on where access is required.
In addition, the removable breaker plate cassette on the NP13 ensures the safe replacement of breaker plate liners. This patented innovation consists of a removable assembly that allows the breaker plate liners to be changed in a safe place outside the crusher. An additional spare cassette can be prepared in advance to further ease and speed up liner changes.
The NP13 maintenance bridge is an innovative and professional solution that provides safe and easy access to both the highest side liners and the rotor, ensuring that the operator performing the maintenance is always working under safe conditions.
The patented Self-Rotation Rotor (SRR) system is the centralized point for the setting adjustment and blow bar change, and further increases safety during maintenance operations. Thanks to its automated turning, the rotor provides a safe environment for changing the blow bars without any risk of injury for the operator.
In addition to these benefits, NP13 offers numerous customization options to help customers fit the crusher to their specific technical and business needs. These include a fully hydraulic setting adjustment, third breaker plate, drive equipment, sensors and automatic greasing, among others.