Meeting the changing needs of the waste-management sector
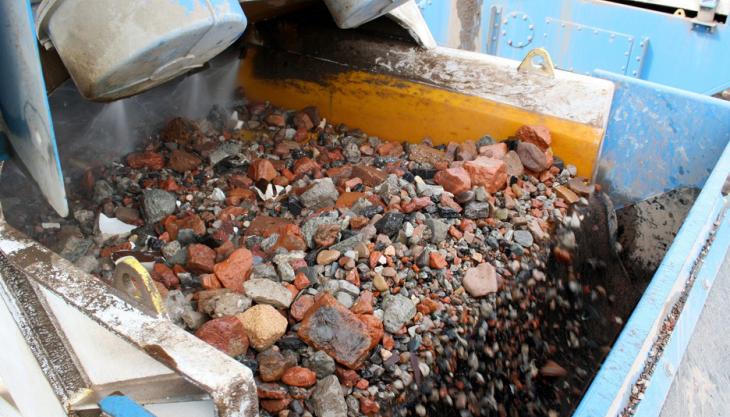
ERIKS discuss the importance of designing and adapting systems and solutions to meet the changing recycling industry
IN 2010, the UK had in the region of 140 landfill sites throughout the UK but by the end of the decade, numbers are expected to dwindle to a third of that. While there are a number of factors at play, perhaps one of the biggest is the reduction in business waste and the effect that landfill taxes have had on companies.
As the number of landfill sites continues to fall, the waste and recycling sector, according to ERIKS, is changing beyond recognition. There remains, however, a number of fundamental principles around the transfer and transportation of waste, whether it is energy from a waste plant, recycling facility or landfill.
Mike Gregson, corporate account manager for ERIKS, said he believes manufacturers and OEM contractors now have an increasingly important role in designing and adapting innovative solutions to meet the changing needs of the sector.
‘Striving to do more with less has become a widely used mantra throughout business as well as in the consumer world – as a means of controlling costs and driving efficiencies,’ he commented.
‘For many businesses, the hike in landfill taxes increased by nearly 12 fold per tonne in just under 10 years and this has led to major changes. In the manufacturing world the concept is also growing – known collectively as ‘ephemeralization’ or, in other words, advancements in technology that allows us to do more with less.’
Mr Gregson added while the future of the waste and recycling sector is not entirely clear, what is certain is that there will always be some form of waste stream that requires disposal, removal and conveyance, and businesses are continually striving to improve efficiencies and costs.
From specialist conveyors to sorting and handling equipment, the role of OEM manufacturers and the supply chain has never been so important, ensuring recycling operators maintain productivity and efficiency at all times.
ERIKS recommend to ensure the day-to-day running of equipment and to maintain productivity, constant monitoring and maintenance is crucial. From vibration analysis to thermal imaging for the detection of overheating, stresses and leaks, there are numerous processes and maintenance methods that businesses can take either as part of a regular maintenance programme or a continual monitoring process.
As operations alter, it is worth considering the demands on equipment and how these might affect the productivity of plant. For example, extra load or a different load may demand more advanced drive and belt solutions.
Automation can offer a welcome support in this aspect. Sensor technology, connected to a PLC or telemetry system, can provide maintenance teams with remote access to vital monitoring data via a secure transparent communication channel.
Cloud-based services, such as ERIKS’ Asset Guard Plus, have the capability to take continual readings of equipment performance; flag any incidents that occur; and identify any key trends. With such a detailed overview of key mechanical functions, operators can detect and rectify minor/major faults as soon as they arise, instead of being left unchecked.
Another increasingly popular maintenance concept is ‘root cause analysis’ which is designed to get to the root of a problem, rather than simply repairing or replacing what seems to be the troublesome component. Implementation of such programmes can be complex and time consuming but in the long term can help operators to reduce maintenance costs thanks to the ability to tackle the root cause.