Launch of two new washing solutions from TWS at Hillhead 2014
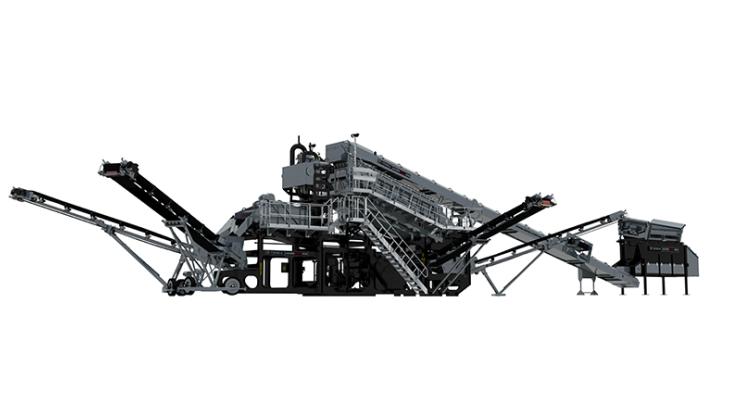
Terex Washing Systems to premiere new Aggresand and Aggrescrub washing plants at Hillhead 2014
PIT and quarry operators can look forward to more innovative ways to wash sand, gravel, aggregates, and C&D waste thanks to two new solutions from Terex Washing Systems (TWS), to be officially launched and showcased at Hillhead 2014.
Hillhead will provide the stage to showcase the Terex Aggresand range, which includes the 165 (up to 250 tonnes/h) and the latest addition, the new larger Terex Aggresand 206 (up to 400 tonnes/h), as well as the Terex Aggrescrub 150 (up to 150 tonnes/h) plant.
The Aggresand 206 wash plant (pictured) is the larger stablemate of the recently launched Aggresand 165 and comprises a 20ft x 6ft screen with two- and three-deck options. The Aggresand 206 plant incorporates modern modular design features and shares all the unique features of the Aggresand 165 wash plant.
Customers will benefit from the unique design which includes: full containerization of the machine for ease of transportation; rapid set-up time; pre-wired and pre-plumbed plug and play componentry; isolated spray bars; and a HMI control system, which have been delivering efficient, productive performance for current owners.
In addition, the level of serviceability within the Aggresand wash plant range is said to be unrivalled within the industry, with innovative features such as rolling chutes and rolling centrifugal pumps. TWS have also included sensors throughout the machine to provide the operator with information on water pressure, cyclone feed pressure, and electrical power consumption, making the operation and management of the machine highly efficient.
TWS director Sean Loughran said: ‘The market has really embraced the Aggresand wash plant concept with exceptional demand at the moment around the world. To date, TWS have installed multiple Aggresand 165 wash plants in Ireland, the UK, parts of Eastern Europe, the US, Canada, Australia and Austria.
‘Customers are also finding it easier to secure planning and finance for these modular plants as opposed to traditional static set-ups. We are constantly looking at innovative ways to further enhance and develop our existing products so we can continue to meet the individual needs of our customers.’
Quarry owner Humphrey Dowling, owner of the first ever Aggresand wash plant, commented: ‘The throughput currently being achieved on the plant is excellent and the quality of the aggregates and sands being produced is very impressive. The high-performance two-deck vibrating grid allows us to feed material directly from the face of the quarry at 200mm; large material is scalped off while the –50mm material goes straight into the wash plant. This eliminates the need for expensive pre-screening of the feed material.’
The second innovative new product to be unveiled at Hillhead 2014 is the new Aggrescrub 150 plant, which particularly suited to the C&D recycling market. Key benefits for customers include the improved wear characteristics, reduced costs, and the ability to effectively scrub aggregates and float out clays/silts/lights (wood/plastics) on one chassis.
In addition, there are also a number of paddle options available depending on customers’ needs, including the traditional hard wearing Hardox blades in 15m and 30mm variances, as well as a new high manganese steel option. It also shares many of the innovative features of the Aggresand range including modular design, quick and easy set-up, pre-plumbed pipework, pre-wired electrics, a HMI control panel and a web-frame chassis design.
The hull acts both as a scrubber and as a water bath. The Aggrescrub 150 model is fitted with a newly orientated DW062 (6ft x 2ft) trash dewatering screen which dewaters any floated-off trash including plastics and organics. The scrubbed aggregate is rinsed and sized on a DW125-2D (12ft x 5ft) two-deck screen, to produce three clean aggregates for stockpiling. Access and serviceability on the Aggrescrub plant is said to be second to none with full galvanized walkway access around the entire plant.
TWS say another unique benefit to customers is the ability of the Terex Aggresand wash plant and Terex Aggrescrub 150 to combine to provide an effective solution for recycling applications as well as for pit owners dealing with high agglomerations of clay. The innovative, intelligent and user-friendly control system on both plants allows full integration between the two systems through the connection of a single plug-and-play cable.
Through this pioneering control system, seamless communication allows the plants to work as a single entity with all interlocks, including start-up and shutdown sequences, automatically synchronizing, which further minimizes the amount of on-site installation and commissioning required.
Hillhead 2014 will provide the first opportunity for customers to see first-hand these innovative washing solution, and a team of skilled engineers, applications and sales technicians will be on hand to provide expert advice and guidance with specific requirements.