New TWS installation for Aggregate Industries at Shoreham
Terex Washing Systems wash plant optimizes processing of sea-dredged sand and gravel
WHEN Aggregate Industries embarked on a significant update aimed at enhancing the operational efficiency and environmental sustainability of their facility at Shoreham, West Sussex, the upgrade involved the installation of new equipment, including a Terex Washing Systems (TWS) wash plant, to optimize the processing of sea-dredged sand and gravel for concrete production.
Aggregate Industries are dedicated to driving decarbonization across the construction materials sector and committed to playing a vital role in the UK’s transition to net-zero emissions. The company’s focus on sustainability and innovation has led to the adoption of low-carbon solutions and a circular economy approach. The facility upgrade at Shoreham marks a milestone in this journey, aligning with Aggregate Industries’ goal of becoming the UK’s leading supplier of sustainable construction materials.
A new ready-mixed concrete plant, strategically located at the Hove end of Shoreham Harbour, replaced the existing facility in New Wharf, Brighton Road. The upgrade involved the implementation of state-of-the-art, environmentally friendly equipment to replace outdated machinery, reflecting Aggregate Industries’ commitment to innovation and eco-friendliness.
The decision to relocate and upgrade was made after meticulous planning spanning three years, with construction commencing in early 2023. The enhanced capabilities of the facility promise a significant boost in output potential and the ability to supply a broader spectrum of materials, providing a competitive advantage in the Brighton market.
The plant comprises the following items of Terex washing equipment, each offering specific benefits to the operation: an H Range feeder, an overband magnet, an MPS cone crusher, an FM120 compact sand washing plant, and a deep-cone thickener and flocculant-dosing unit.
The H Range feeder ensures a consistent and reliable feed of material into the processing system, with its robust design and precise control contributing to improved efficiency and reduced downtime.
The overband magnet is essential for removing ferrous metals from the material stream, ensuring the quality and purity of the final aggregates. This helps in meeting quality standards and reducing the risk of contamination.
The MPS cone crusher is instrumental in crushing any +40mm gravel from the process. Its high-performance crushing capabilities ensure the production of high-quality aggregates suitable for various construction applications.
The FM120 Compact is a compact sand washing plant designed to efficiently remove impurities and fines from the sand fraction. Its compact design saves space while delivering high-performance sand washing, essential for producing quality concrete.
The deep-cone thickener and flocculant-dosing unit work together to facilitate efficient water management and sludge treatment, the former unit aiding the settling of solids, whilst the latter ensures effective flocculation, leading to clearer water discharge and reduced environmental impact.
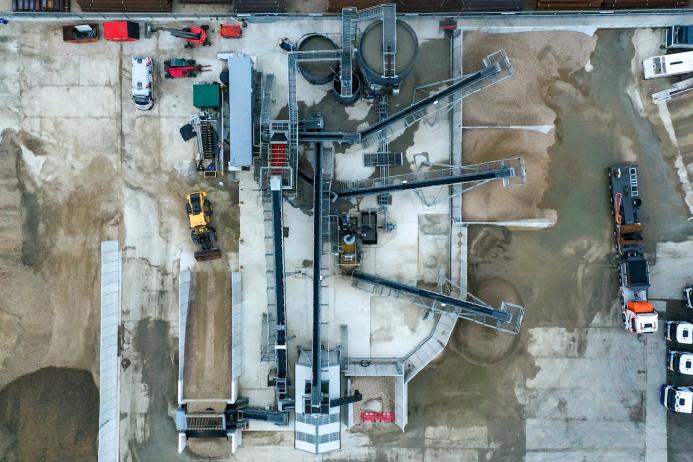
With the introduction of the TWS wash plant, the upgraded facility significantly elevates Aggregate Industries’ capacity and efficiency in the production and supply of concrete to Brighton and its neighbouring areas. With a two-fold increase concrete mixing speed, the company can meet growing demand effectively.
The modernized facility allows the production of diversified concrete types, catering to a wide range of construction needs. This includes the introduction of Cemfloor liquid screed product, positioning Aggregate Industries as the sole supplier of this product in Brighton.
A standout feature of the new plant is the addition of a wharf facility capable of accommodating large-scale aggregates supply via ship. This enhances overall efficiency and logistics of material transportation, reducing Aggregate Industries’ carbon footprint and costs.
The facility incorporates other sustainability initiatives too, such as on-site electric charging points for cars and the utilization of neighbouring solar panels, emphasizing Aggregate Industries’ commitment to a sustainable future.
The Shoreham facility upgrade, incorporating TWS equipment, signifies a significant step towards achieving operational excellence and environmental sustainability. By leveraging innovative technologies and sustainable practices, Aggregate Industries say they are continuing to lead the way in supplying high-quality construction materials while reducing their carbon footprint.