High-capacity screening with Niagara XL-Class
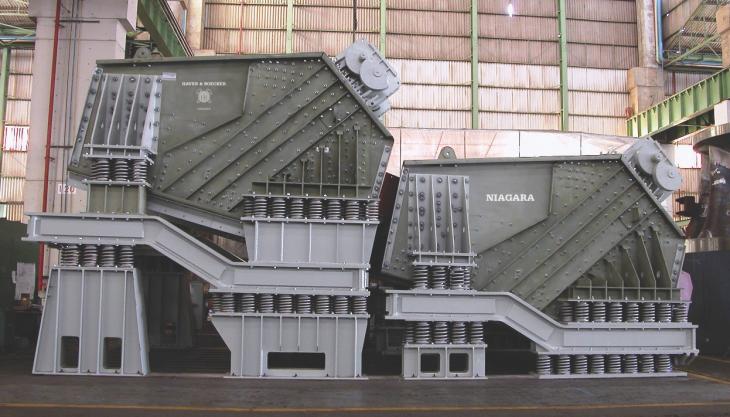
Niagara XL-Class vibrating screens capable of production rates up to 15,000 tons per hour
THE Niagara XL-Class vibrating screen from Haver & Boecker Niagara combines advanced exciter-drive technology with a wide body to offer producers high-capacity screening action at rates up to 15,000 tons/h.
The XL-Class is the largest exciter-driven machine in the industry and each one is custom-designed to suit its specific application using finite element analysis (FEA).
With more than 15 years of FEA and experimental measurement experience – and nearly 400 high-capacity vibrating screens supplied to the global market – Haver & Boecker Niagara say they are able to provide state-of-the-art, high-capacity vibrating screens that offer easy operation, low maintenance and maximum reliability.
‘Haver & Boecker Niagara are dedicated to using innovative technological solutions to enhance customers’ daily processes,’ said Eduardo Iizuka, chief engineer of product development. ‘Our ability to optimize the XL-Class to perform at peak efficiency, according to exact application requirements, provides a reliable, low-maintenance screening solution for our customers.’
Haver & Boecker Niagara strategically engineer XL-Class vibrating screens using FEA, which predicts high-stress areas and natural frequencies. The analysis equips engineers with the appropriate information to understand the machine’s expected performance, determine where to reinforce critical areas of the vibrating screen and reduce the weight of oversized components, resulting in an optimized vibrating screen.
The company then customizes each XL-Class to perform at maximum productivity according to a producer’s specific application requirements.
The vibrating screen features a robust, maintenance-friendly design, with the fully bolted, non-welded construction of XL-Class side plates eliminating the possibility of stress concentrations from welding.
The machine’s large deck size maximizes feed rates, allowing it to effectively handle production rates up to 15,000 tons/h and cut sizes from 48 mesh up to 10in. The overhead bridge-mounted drive system does not interfere with the material flow path, reducing the wear potential that shaft-driven machines experience.
In addition, the XL-Class is sloped from –3° to 10°, offering operations further flexibility. The negative angle allows the horizontal screen to be used in dewatering applications – the declined installation angle using the force of gravity to keep water back, while the linear action throws the material forward down the deck.
The decline also allows a material bed to build up, which acts like a filter cake to capture the fines and allow the water to pass through. Additionally, the inclination option increases the material velocity to decrease layer depths and allow for a more efficient separation of fines from the coarse material, resulting in increased material flow and maximum production.
Unlike other manufacturers, Haver & Boecker Niagara manufacture their own brand of Niagara exciters, which come as standard on all new XL-Class vibrating screens. The bridge-mounted exciters are available in four models to improve screening performance and are said to offer the largest static moment range on the market.
Owing to their strength and advanced sealing system, Niagara exciters offer producers minimal maintenance and an extended service life of up to 50,000 hours. Producers can also purchase Niagara exciters for use on any other brand of exciter-driven vibrating screen.
All Haver & Boecker Niagara vibrating screens undergo extensive testing, inspection and the company’s Pulse vibration analysis prior to shipping, to ensure correct balance and smooth operation.
For added security, new XL-Class purchases are eligible for the industry’s only three-year Uptime warranty. This includes Haver & Boecker Niagara’s signature PROcheck consultation and offers customers a full-service approach to prevent unscheduled maintenance and extend the life of the vibrating screen. It includes parts inspection, equipment assessment and a screen media evaluation, resulting in a fully optimized screening operation.