Finning first-time fix rates soar
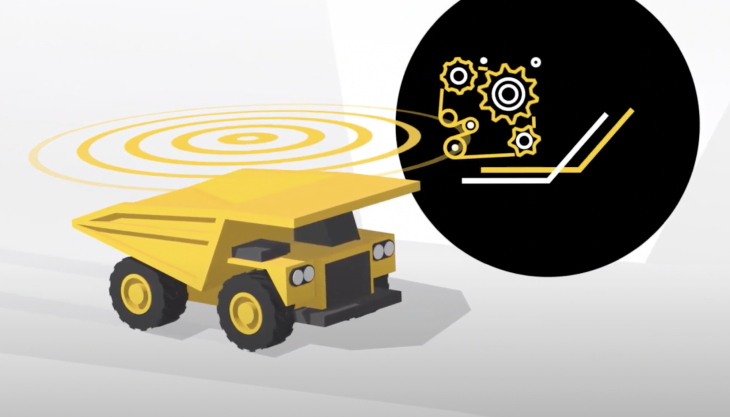
Sharp rise in engineers’ first-time fix rates following successful remote diagnostics trial
Finning UK & Ireland are rolling out a remote diagnostics programme after a successful trial saw a sharp rise in engineers’ first-time fix rates – cutting customer downtime and saving more than 2,500 man hours.
Finning have 14,000 connected machine assets operating across the UK, and during the 12-week trial the remote services team used diagnostics data to identify operational issues with the machines before any problems occurred.
Because Finning engineers can see what is going on within a machine and run a diagnosis remotely, they are able to ensure they have the correct parts to complete work during their first site visit. In some cases, this advanced technology meant a visit to a customer site was not necessary, because the remote service team was able to fix the problem remotely.
The result is minimal downtime for the customer, safeguarding their bottom line, and a reduction in the carbon footprint at Finning due to fewer engineer journeys, together with an increase in engineer capacity meaning faster response times for customers.
Finning technology and remote services manager Nikolaos Kakoudakis said: ‘This advanced technology is transforming the way customers access our service expertise, providing us with the data to take our offering to another level.
‘Eighty percent first-time fix rate is considered best in class and is the figure automotive breakdown companies quote for their roadside repairs, though in our case customers may not even be aware of all the work being done in the background to keep their machines running. The challenge is in providing this across such a diverse product range.
‘Our advanced technology can signal the condition of machines, allowing us to prep the parts needed and organize an engineer site visit before the customer even makes a call. In some cases, if it’s a software or configuration problem, we may not even need to visit the customer at all and can get them up and running by sharing the screen and updating the software.
‘This level of service, which is available to all customers regardless of warranty or maintenance agreements, and to customers of both new or used machinery, saving them from costly failures and unplanned interruptions, forms part of our global roadmap for service transformation through knowledge sharing across the group.’