CEMEX keep new Tilbury plant ship shape with CompVAC
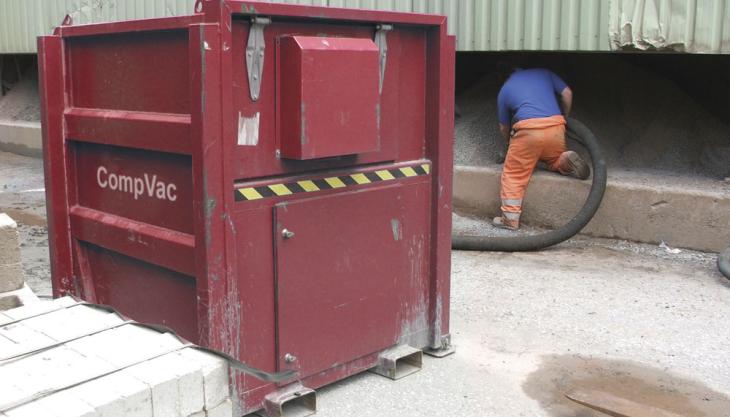
In September 2009 CEMEX opened a new 1.2 million tonne cement grinding and blending plant at the Port of Tilbury in Essex. The £49 million investment underlined the company’s commitment to sustainable construction and has increased CEMEX UK’s cement capacity by 20%.
The new plant is a showcase for high-tech cement manufacture so it receives a lot of visitors, and that means keeping everything as clean as possible. The man responsible for achieving the highest standards of housekeeping at the Tilbury site is Tony Drake.
‘Making cement by grinding clinker inevitably produces a fair amount of dust, and while spillages are relatively small, they still happen and need to be dealt with, explained Mr Drake. ‘We found that the best cleaning solution was a Gotland CompVAC.’
Les Thomas, who is responsible for purchasing at CEMEX Tilbury, was involved in the decision to hire the Gotland machine. He said: ‘The CompVAC is really good. We initially hired it for one month back in January to see what it could do. It proved to be exactly what we needed so we hired it out for another six months, and since then we’ve decided to hire it to the end of the year with a view to purchasing one.’
Tony Drake continued: ‘The main aim with the CompVAC is to remove and recycle as much dust as possible, but cement powder is a bit like water in its behaviour when loose. It doesn’t need a lot of imagination to see that the old way of cleaning up and removing the cement powder with brooms, shovels and brushes was not only very inefficient, but involved all sorts of manual handling issues which we were very keen to avoid wherever possible.
‘That’s why we like the Gotland CompVAC. It’s ideal for vacuuming up all the spillages, and as we’ve got 32-amp welding sockets all around the plant, it’s easy to move it with a forklift to wherever we want to clean up any dust build-up. It’s a fully enclosed system, so there’s no risk of dust escaping, and once the waste dust is in the hopper, it’s then very easy to recycle it into the reject pile and put it all back into the manufacturing process.
‘The operatives on site love using the CompVAC compared to brooms, brushes and barrows. It’s much easier and faster, and using it is virtually dust-free so there are no dust-inhalation issues either. It’s simply a case of pointing the nozzle at the loose dust or powder and job done,’ said Mr Drake.
‘Because it’s a new site and the only vertical mill of its kind in the UK, we get a lot of visitors. Having the CompVAC on site as part of our cleaning resources makes it easy for us to keep on top of things and make sure the whole plant is as clean as possible. We get a lot of positive feedback about the cleanliness of the plant.’