A BRAVE new world for bearings
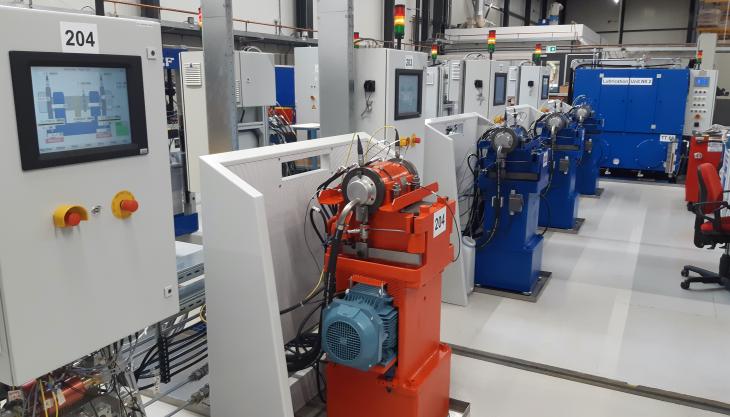
SKF building experimental verification facility to study mechanisms behind bearing failures
AN experimental verification facility that will provide unprecedented insights into the mechanisms behind bearing failures and performance prediction is currently being built by SKF.
According to SKF, some 10 billion bearings are manufactured each year and, given the harsh conditions to which they are often subjected, the vast majority prove incredibly reliable. Indeed, approximately 90% of these bearings will actually outlive the equipment to which they are fitted.
Only 0.5% of bearings actually fail in service, but this still means that some 50 million have to be replaced due to damage or failure every year, and each of these failures will likely have financial implications for their operators in terms of lost production, damage to adjacent parts and the cost of repairs.
There are numerous reasons why bearings become damaged or fail. Generally, around one third fail due to fatigue, while another third fail due to issues with lubrication. Contamination causes a sixth of bearing failures, whilst the balance is accounted for by other factors, such as improper handling and mounting, heavier or different loading than was anticipated, and poor fitting.
When attempting to predict how, and perhaps more importantly when, a bearing will fail, a huge number of variables must be taken into account, including the application for which it will be used, the environment in which it will operate, the lubricants used, the loads to which it will be subjected etc. As such, when developing new bearings, verifying their performance and how long they will last can be a slow, expensive and complex process.
SKF are looking to solve this problem at their Research and Technology Development (RTD) centre in Houten, The Netherlands, where the company has started work on the construction of an experimental verification facility that it will use to increase its knowledge of the mechanisms that cause bearings to fail. It will also use the facility, which will be called Bearing Rigs for Accelerated Verification Experiments (BRAVE), to develop ways to predict the remaining useful life of these critical components rapidly, accurately and repeatably.
Urszula Sachadel, team leader for bearing steels, and Edwin Tummers, team leader for Experimental Verification at SKF, are running the project.
‘We need a flexible testing facility where we can simulate different application conditions and see how a bearing system, including the materials from which it is made, and the lubrication employed, performs when operating under different loads and at different speeds,’ said Mr Tummers.
‘We also need to be able to do that in a way that allows us to perform investigations on that system, so we can determine how defects are generated, how they progress and how long the bearing will last until maintenance is required.’
When completed, BRAVE will feature a number of rigs – all specifically designed and tailored to meet SKF specifications – that will be used by researchers to develop and experimentally verify bearing failure models. The functions of these rigs will be categorized as ‘contaminate’, ‘initiate’ and ‘propagate’, and they will often be used in sequence.
Urszula Sachadel explained: ‘With the contaminate set-up, for example, we can generate defects such as dents, abrasion, electrical damage and corrosive damage in the bearings in different ways. We can also apply different lubricants. In the initiate set-up, we can then run the bearings under certain conditions to create some initial damage to them. Finally, in propagate, we can determine how different load and speed conditions influence the rate at which this damage spreads. Each set-up type can also be used in isolation or in a ‘mix-and-match’ approach, allowing a wide range of tests to be performed.’
In this way, SKF researchers will be able to screen many different variants of bearings very quickly, to determine the best solution for a given application. Test procedures will be developed, controlled and monitored closely, and all of the data regarding vibration, temperature, load history etc will be recorded for detailed analysis either during or after the experiments.
Ms Sachadel continued: ‘Using BRAVE, we will be able to quickly evaluate potential bearing solutions, screen them, and understand the impact of different manufacturing processes on their performance. Furthermore, in the future, we can use the data we gather to support our development of artificial intelligence and machine learning techniques to predict or improve the performance of our bearings.’
BRAVE will be of particular benefit to SKF’s Rotating Equipment Performance (REP) business and its remanufacturing operations. ‘We plan to look at the bearings after different stages of remanufacturing to determine how the process affects their performance and how to boost it,’ explained Ms Sachadel, who added: ‘Work on the facility is currently scheduled for completion in early 2021. We’re going to learn a lot of new things through BRAVE, which we look forward to sharing with our customers.’