It’s In The Bag At Tolworth
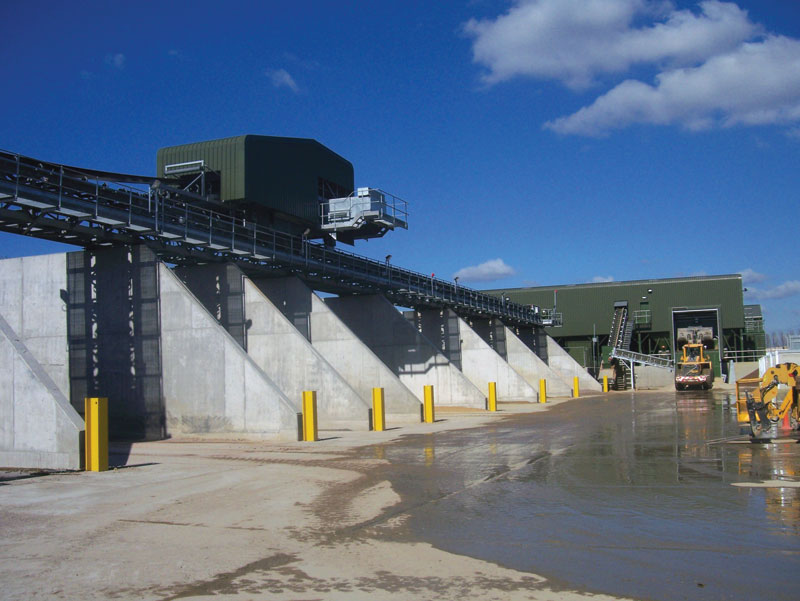
New rail aggregate discharge system with twin bagging lines for Day Group’s south-west London site
Having previously installed a new rail discharge system at Purley, in south London, the Day Group recently used the experience gained at that site when installing a similar system at Tolworth, in south-west London, during spring 2008. The company originally established the Tolworth site around 10 years ago as it formed a strategic fit between their sites in Purley and Brentford, providing comprehensive coverage of the South East.
Currently serving its neighbouring London Concrete plant with bulk aggregates, the Tolworth site also dispatches bagged aggregates from a Webster Griffin bagging plant that was installed during the summer of 2007. Day Group, having gained an increased share of the bagged aggregates market, as well as an increase in bulk haulage for the builders’ merchant trade, when they acquired CJ Burgess in 2005, saw the addition of the bagging plant as an opportunity to add value to the Tolworth site and subsequently secured a significant contract with building product suppliers Wolseley UK.
The bagging plant itself commenced production in July 2007 and now supplies several independent operators. Owing to a number of recent important contracts, the site expects to see a significant increase in the 70,000 tonnes of bagged aggregates supplied in its first year. ‘We expect to be heading towards 150,000–175,000 tonnes, even in the current climate,’ commented Michael Woodward, project manager for Day Group at Tolworth.
To facilitate this level of throughput a more efficient means of receiving and unloading aggregate became imperative for the Tolworth site, which originally operated simply as a railhead where the wagons were unloaded by a mechanical grab.
After the success of the first aggregate discharge system at Purley, Day Aggregates once again appointed LJH – DUO Manufacturing as the main contractor at Tolworth. The Somerset-based company was subsequently charged with the complete design, manufacture and engineering for the new system.
The first train passed through the new rail discharge system at Tolworth during the first week of April 2008. Since then there has been an average of three trains a week delivering aggregates from Aggregate Industries’ Torr Works, in Somerset, and from Brett Aggregates’ site at Cliffe, in Kent, but with the anticipated increase in volumes, up to five trains a week are expected to arrive at the depot in future.
‘The rail discharge system gives us an efficient and environmentally convenient means of delivering aggregates, and also provides a significant advantage in terms of serving our markets,’ said Mr Woodward.
Although broadly similar to the systems operated at Day’s other sites, this latest system incorporates a number of differences to meet the specific site requirements at Tolworth. Located adjacent to the mainline railway station, space restrictions mean the aggregate depot is smaller than the one in Purley and also at a slightly lower level than the rest of the yard area.
The new discharge system itself is housed in a composite-clad building that provides effective noise attenuation and, at 8m in length, is long enough to contain an entire wagon while it discharges its load. From the outside, it is no longer possible to hear the discharge from the trains, whereas the previous grab discharge operations were clearly audible.
Whereas the Purley system has two large hoppers located beneath the discharge point from which two inclined conveyors feed on to a main conveyor, at Tolworth the discharged aggregate drops on to a single 1,800mm wide conveyor, which, in turn, feeds on to a 1,400mm wide 18.5° inclined conveyor equipped with a belt weigher.
This, in turn, feeds on to the 1,400mm wide main tripper conveyor, which traverses the top of the concrete stockpiling bay walls until the required bay is reached. At this point the aggregate is transferred on to a 1,400mm wide carriage-mounted cross conveyor, which deposits the aggregates in the selected bay. This conveyor can discharge either side of the tripper and is counterweighted to balance the load on the tripper rails. Ultrasonic level sensors and a back-up deflection probe prevent the various bays from being overfilled.
Unlike the Purley depot, at Tolworth there was insufficient space to install a ground hopper/feed conveyor system because of the difference in height between the depot and the rest of the yard. The ground hopper would have been too deep and would have presented too steep an angle for the feed conveyor to deliver on to the main tripper conveyor.
As a result, the discharge system at Tolworth does not remain loaded while the wagons are shunted, contrary to the operation at Purley. The time difference, however, is not considered to be significant; the Tolworth system still only takes around 1h 15min to discharge an entire 18-wagon train and requires just one person to operate the system.
‘The system capacity is actually 1,400 tonnes/h but, with shunting time, the discharge rate is approximately 1,200 tonnes/h,’ explained Mr Woodward. ‘This solution not only fits the space restrictions at Tolworth but, with fewer conveyors and equipment to maintain, is also a more cost-effective solution.’
A graphical interface on the computer control panel inside the building allows the operator to monitor the entire discharge system, including the storage bays for each of the aggregates, which comprise: washed marine sharp sand; 10mm and 20mm shingle; scalpings; Type 1 limestone; 20mm ballast; and 4/20 limestone.
A re-feed hopper similar to the one at the Purley site, although arranged in a different configuration, allows Day to blend recycled aggregates with the primary aggregates as they are being discharged.
‘Depending on what we are discharging from the train, and taking into account specific customer requirements, we might want to blend recycled sharp sand, recycled glass sand or recycled sub-base material from our construction and demolition waste plants,’ said Mr Woodward.
The recycled aggregates can be introduced in blend ratios ranging between 5% and 40% using the control interface’s main menu. According to Day, the blending process is very efficient as the recycled materials are mixed with the primary aggregates at three locations as they travel from rail wagon to stockpile – first, as the material is being discharged; secondly, at the transfer point on to the cross conveyor; and finally, as the load is discharged by the cross conveyor into the stockpile.
The bagging plant
Aggregates from the stockpiles at Tolworth are delivered by loading shovel to two bulk hoppers that serve the London Concrete plant and Day’s four bagging lines – two bulk-bag lines and two 25kg bag lines.
Having been notified of the type of aggregate needed by staff within the plant, the shovel operator deposits the required amount of material in the plant feed hopper. A digital display board informs the shovel operator of the level of material in each of the four hoppers that supply each of the bagging lines.
The materials bagged in the plant comprise approximately 30% sharp sand, 30% soft sand and 30% ballast. The remaining 10% comprises shingles and sub-base.
One of the 25kg bagging lines is semi-automatic, whereby the operator mounts a pre-formed bag on the machine, which then fills and seals the bag before sending it, via a roller conveyor, to a robot palletizer. This semi-automatic line fills nine 25kg bags per minute.
The second 25kg line employs a fully automatic, form fill and seal bagging line, which also prints a description of the contents on the bag. A roll of film is fed through a series of rollers and automatically centres itself on the forming tube and the length of bag is then filled with aggregate.
Day hold rolls of film with customers’ print on it as well as plain film – the automated machine has three printing heads that can print on the bag’s sides as well as the front, so that when the bags are palletized and stacked the contents can be easily identified. The machine seals the top of lower bag and bottom of the filled bag and sends the filled bag on a roller conveyor to the line’s own robot palletizer.
The semi-automated line gives Day’s bagging operation greater flexibility. ‘It’s not economic to buy large amounts of film for independent builders’ merchants, as we need the flexibility to bag for either large clients or the smaller independents,’ said Mr Woodward.
Having two robot palletizers – one for each of the 25kg bagging lines – also helps to keep operations moving should one robot requires maintenance. Originally, a single robot was used, but this meant the machine had to turn through 180° to pick up a bag from each of the two roller conveyors – one from the semi-automated bagging machine and the other from the automated unit. Adding a second robot to work in tandem means that each machine now only needs to turn through 90°, which speeds up the palletizing process considerably. It takes just 2.5min for the automated line and 5min for the semi-automated line to stack fifty 25kg bags on a pallet.
‘The quality of the stacking is very good,’ said Mr Woodward. ‘We spent a lot of time getting this right so that we don’t need to shrink-wrap. The bags have a non-slip layer on the outside to create resistance when they sit on top of each other. This keeps the stack stable.’
Day are currently increasing their 1,000-tonnes a week bagging plant throughput to 2,000 tonnes a week and, with the hope of additional business, they expect this to increase further. This, say Day, will come close to the system’s current capacity, so further investment may be required in the future if demand dictates.
DUO Manufacturing (LJH), Mendip Works, Leigh Road, Chantry, Nr Frome, Somerset BA11 3LR; tel: (01373) 836451; fax: (01373) 836879; email: sales@ljhgroup.co.uk