Intermodal Cement Transport
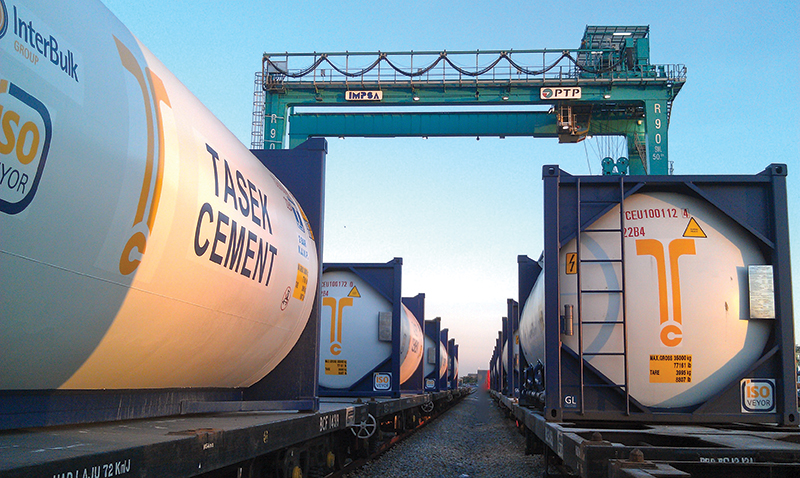
First published in the August 2014 issue of Quarry Management
Use of InBulk Technologies’ ISO-Veyor tank containers ramps up in Asia-Pacific
InBulk Technologies, part of the international bulk logistics group InterBulk Group plc, are braking new ground in the supply of their patented non-tipping ISO-Veyor container for cementitious materials in areas where there is a proliferation of islands.
The ISO-Veyor is an intermodal tank container, developed by InBulk Technologies, to facilitate easy transition between road, rail and sea. It consists of a cylindrical vessel constructed within the frame dimensions of a 20ft or 30ft ISO unit and can be handled in exactly the same way as a standard ISO container, utilizing currently available trailer chassis and rail car rolling stock.
InBulk Technologies secured a contract for ten 20ft ISO-Veyors from Golden Bay Cement for their ‘inter-island’ cement deliveries from New Zealand’s North Island down to the South Island. The contract was in two parts; an initial order for four units was placed, then, once operational quality had been established, a subsequent order for the remaining six units was made following an evaluation period of several months.
Golden Bay Cement will soon be the last remaining domestic producer in New Zealand, after Holcim recently announced plans to close Westport, their last remaining cement production facility on the North Island.
The major advantage that the ISO-Veyor system offers is transportation flexibility. By managing the logistics supply chain intermodally to the South Island, Golden Bay will be able to remain flexible and responsive to the fast-changing demands of the market without facing the large-scale investment decisions normally associated with traditional, more permanent structures and equipment such as fixed silos, road tankers and PD rail wagons.
Cement, ash or slag cement can be loaded into a truck-mounted unit at a plant and then transported to a rail, barge or shipping terminal for trans-shipment without any double handling of the material.
In recent years InBulk Technologies have witnessed a surge of activity and interest from customers operating on or between islands. Some scenarios include construction projects where the ISO-Veyor provides an ideal system for intermodal deliveries without the need for investment in silos or large-scale storage facilities.
Previous scenarios have included the use of road tankers travelling on roll-on/roll-off ships, which represents a lot of wasted space on a ship compared with an ISO-Veyor, which fits within the rails of a standard container ship. The ISO-Veyor is more environmentally friendly too, as it allows its owners to make choices between the most efficient methods of transport.
Moreover, the capability to store material horizontally, up to four units high, offers on-site storage options that in the past were hampered by economics or space limitations.
Compared with traditional designs for dry bulk tanks, the ISO-Veyor comes with a number of design improvements that provide better performance during operation, such as horizontal discharge (without need for tipping) and residues of only 0.2% following discharge. In addition, the innovative design is capable of multiple discharges of powders without the need for calibration and offers a class-leading payload due to the flat fluidization bed.
In opting for the ISO-Veyor Golden Bay showed a preference for equipment with superior build quality and a proven track record. Sean Dillon, logistics manager for the company, commented: ‘The ISO-Veyor was primarily chosen for its robust design, operational performance and long list of previous approvals. Intermodal equipment gives us greater flexibility in managing our fleet. The unit can be used across any number of combinations involving road, rail and sea options, thereby widening our flexibility and overall appeal to customers.’
The ISO-Veyor is now available across the globe. As well as recent contracts and expansion in Asia and Europe, InBulk’s specialist containers are also widely used in countries such as the US, Canada, South America, Africa and Iceland. Recently, many cement suppliers and construction and mining companies have made the switch to ISO-Veyors and are establishing new supply chains in a bid to increase efficiency and cut transport costs.
The products that can be transported in ISO-Veyors includes minerals such as cement, fly ash, ground granulated blast-furnace slag, white cement, aluminates and waste materials. Future developments may see the system extended to chemicals and food-grade versions, which would be fully cleanable; in line with current systems for liquid ISO tanks.
Dean Reilly, marketing manager at InBulk, explained: ‘We are delighted to receive the first orders for ISO-Veyors from Golden Bay Cement. In order to fulfil the requirement, we achieved the necessary ‘Worksafe’ approvals in a matter of only a few weeks. We are experiencing a large volume of new enquiries, especially from island locations in and around Asia. In particular, there is huge scope for development in Indonesia and Malaysia.’
In addition to new developments in New Zealand, InBulk Technologies Ltd have received an order from one of Malaysia’s leading cement producers, Taesk Cement.
Singapore provides a stable market for cement with just over 6 million tonnes consumed during 2013 and current yearly growth estimated at close to 5%. A combination of factors is driving the trend for 100% imports, including the closure of the country’s long-established grinding facilities, zero trade tariffs and excellent supporting infrastructure.
Tasek Cement were looking for the necessary equipment for the flexible exportation of cement by rail to Singapore. Cement loading takes place in Malaysia, with the empty ISO-Veyor trains passing through a rail-loading shed where the containers are quickly filled via drop-down loading spouts. Once an entire train has been loaded, it makes its way to Singapore.
Tasek Cement had long been looking towards intermodal tank containers as a means of transport and storage. One of the key reasons for choosing intermodal tank containers, as opposed to traditional dedicated bulk equipment or fixed silo storage capacity, was the reduction in capital expenditure. Whereas with traditional fixed equipment it can take many years before the cost of the assets is recovered, the same level of commitment/payback is not required with intermodal tank containers.
Moreover, the flow of cement by rail provided a clear opportunity for Taesk Cement to maximize payloads and improve competitiveness, compared with road deliveries where the combined weight of the full container, plus truck, plus trailer, generally reaches the maximum permissible weight for public highways (approximately 40 tonnes) before the container has been completely filled.
Bulk density, which is defined as the mass of the particles of materials divided by the total volume they occupy, is not an intrinsic property of a material and can change depending on how the material is handled. Bulk densities of powders are reported as ‘freely settled’ or ‘poured’ density, whilst ‘tapped’ density refers to bulk density after compaction.
The densification process is relatively simple but effective. The three-quarters-full ISO-Veyor is suspended on a cradle and literally ‘shaken’ until the cement settles and any air pockets are released. This requires a certain robustness of design and superior build quality, which the ISO-Veyors offer. Once shaken another load can be added on top.
Cement has a bulk density of around 1.0 tonne/m3 (poured) and 1.2 tonnes/m3 (tapped). Tasek Cement, who were looking to vigorously shake the filled container in order to release the air pockets and achieve the highest possible payload, quickly identified a target of 30 tonnes per container, taking up 25m3 of space.
When a road tanker, rail wagon or bulk ship is initially filled there is usually no time to allow the cement to settle and for the air to escape. Companies invariably purchase their cement at a ‘poured’ bulk density, meaning efficiency and money is being lost. Tasek Cement insisted on providing a ‘tapped’ bulk density for their planned rail cement exports into Singapore, thereby achieving a 10% increase in payload as 30 tonnes is reached after filling instead of the 27 to 28 tonnes that would normally be expected. Taking into consideration the extra 3 tonnes per container and the fact that there are 60 ISO-Veyors per train, the savings begin to mount up and a clear strategic competitive advantage emerges.
During 2011 and 2012, Tasek Cement took delivery of 150 20ft ISO-Veyors. For InBulk to secure the business, DOSH approvals had to be achieved for the first time – this is a particular Malaysian standard whereby InBulk Technologies had to ensure that every component, down to the last nut and bolt, met with specific material quality standards.
Martin Press, managing director of InBulk Technologies, concluded: ‘We were delighted that Tasek Cement came to InBulk Technologies for this very strategically significant project. The increased payloads being achieved in combination with lower residues and rapid discharge performance are all helping to provide a competitive edge for the import of high-quality cement into Singapore’s Jurong Island.’
- Subscribe to Quarry Management, the monthly journal for the mineral products industry, to read articles before they appear on Agg-Net