A Grand Union
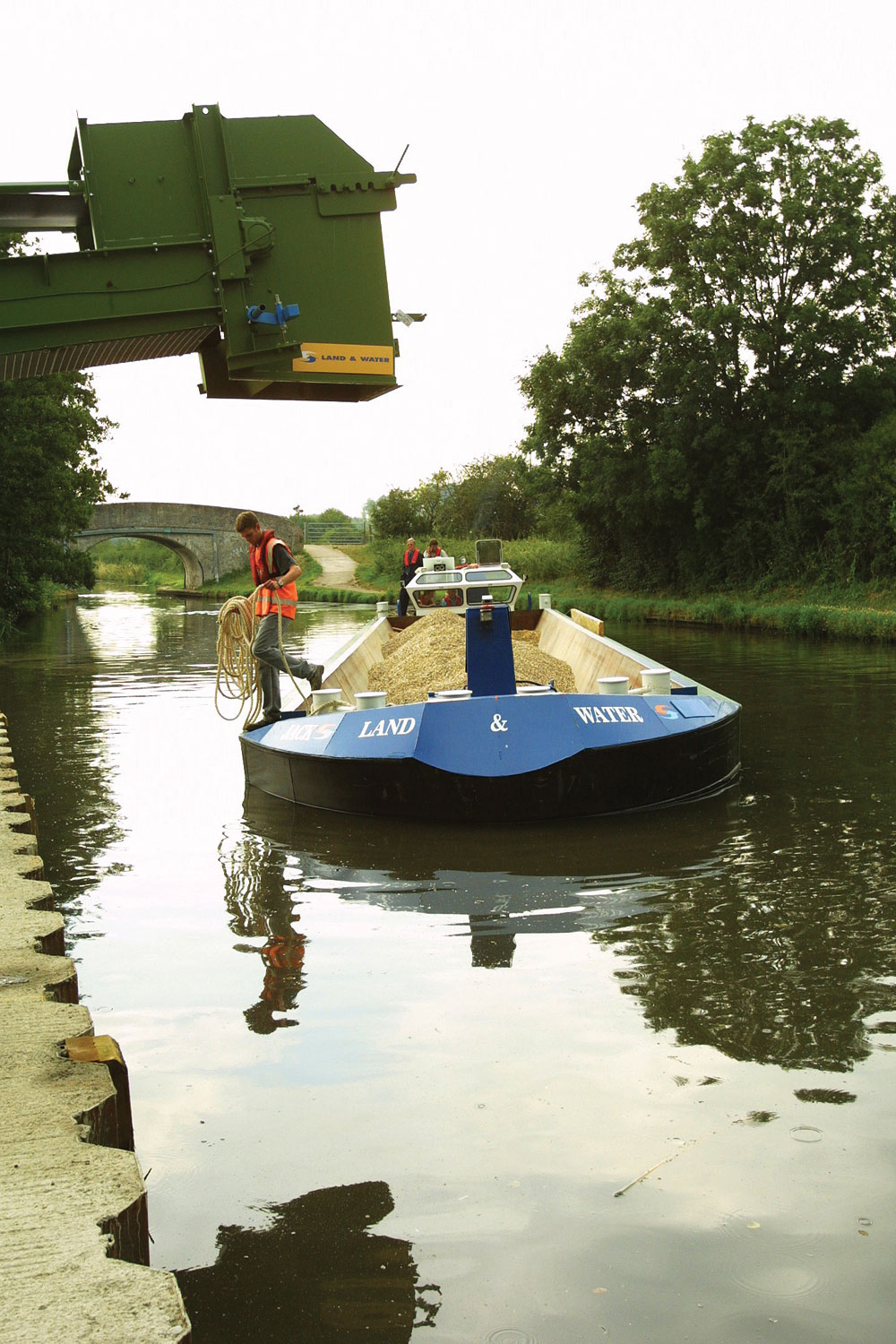
Hanson and Harleyford team up to transport aggregates by canal
A little bit of waterways history was made in July when a stretch of the Grand Union Canal west of London carried its first contracted freight vessels for over 30 years. The regeneration of this part of the canal as a regular freight transport route has been brought about as a result of a new contract between British Waterways London, Hanson Aggregates Ltd and privately owned Harleyford Aggregates Ltd, which will see the latter supply over 450,000 tonnes of sand and gravel to Hanson over the next seven years.
The project commenced during 1999 when the two aggregates companies entered into an agreement to transport sand and gravel from Harleyford’s site at Denham in Buckinghamshire to Hanson’s depot at West Drayton in Middlesex. Although the two sites are only five miles apart, it was originally envisaged that the material would have to be transported by road on the highly congested western sections of the M40, M25 and M4.
However, as part of the planning approval gained in 2000, and as an alternative to using lorries, Harleyford Aggregates had included an option to remove material from their quarry at The Lea in Denham via a temporary field conveyor built across a flood plain, to the Grand Union Canal where it would be loaded on to barges and transported to the West Drayton mineral distribution depot owned by British Waterways and managed by Hanson.
As statutory consultees to the planning process, British Waterways had been involved with Hanson Aggregates’ proposal from the beginning and, once planning had been approved, approached specialist civil engineering and waterways contractors Land & Water Services to develop a canal transport solution for the proposed works. At the same time Hanson and British Waterways approached the Department of Transport (then part of the DETR) for funding under the EU-subsidised Freight Facilities Grant scheme, which aims to encourage non-road transport solutions for environmental and economic benefit — making this one of the earliest schemes in its sector to apply for such a grant.
The value of such grants is calculated according to the number of road miles saved, the weight of material transported and the road categories involved (the smaller/more densely populated a road, the higher its category). In this particular case it was calculated that the scheme would remove a total of 60,000 tonnes a year or 6,000 lorry loads off the busiest sections of the M40, M25 and M4 over a seven-year period.
Based on these figures an EU grant of £222,000, together with a further £240,000 from London’s Waterway Partnership, was sufficient to subsidise the infrastructure costs that would allow Land & Water Services’ proposal to compete on a competitive basis with conventional road transport.
In November 2001 Land & Water put forward a turnkey solution whereby the company would take complete responsibility for the design, procurement, manufacture, installation and operation of the entire project over the seven-year period to 2010. The proposal included the use of conventional field conveyors to transport material from the quarry to the Grand Union Canal, a pair of revolutionary self-propelled barges to move the material along the canal, and a bespoke excavator and hydraulic grab to unload the materials at the other end.
Following 12 months of fine-tuning the proposal, Land & Water signed contracts with both British Waterways and Hanson Aggregates in December 2002.
Conveyor design and installation (Denham)
The route for the conveyor had been agreed in the original planning application and was one of the most challenging aspects of the project. The conveyor had to cover a total distance of 450m, cross two private access roads and the river Colne, and circumnavigate several important woodland areas without disturbing the environmentally sensitive wetland flood plain it was traversing.
Land & Water undertook early consultation with the Environment Agency, particularly with regard to the potential impact of the river crossing. As part of this consultation the height of the underside of the conveyor bridge was raised to match that of the adjacent A40 road bridge in order to allow safe passage for flying swans. Further liaison took place with regard to the engineering works on the riverbanks either side of the bridge crossing. Again Land & Water modified the original design, with the proposed concrete foundations replaced by tubular driven piles that did not require excavation (and the consequent ground disturbance) for installation.
To facilitate construction of the conveyor as well as its ongoing maintenance Land & Water were required to build a temporary access road. A fibrous geotextile was laid down to protect the wetland soils before the road was constructed using material from Harleyford’s quarry.
Construction of a section of the road between the river and the canal required these materials to be imported by lorries via the A40, but despite early approaches by Land & Water to the Highways Agency, access to the field using an existing gate on to the A40 was denied as a result of traffic-management issues.
To mitigate the resulting costs and loss in time associated with the problematical access to this field, Land & Water developed an ingenious method of ‘handing’ the road materials across the 30m wide river using a combination of two long-reach excavators. The two machines were mobilized at short notice for this exercise and completed the task in just seven days.
Supplied by Continental Conveyor, the field conveyor was subsequently modified to allow remote starting by Harleyford Aggregates’ quarry staff in order to mitigate the delay in barge loading as the mineral travels along the conveyor. A radio link between the vessels’ skippers and the quarry has been provided to enhance communications in this respect.
A new wharf and quay to accommodate the barges alongside the conveyor’s overhead discharge gantry was designed and constructed by Land & Water in a field adjacent to the canal.
Barge design and manufacture
Research by Land & Water Services into the history of the Grand Union Canal established that the locks between the Denham site and the river Thames (including passage past West Drayton) had been modified in the late 1960s to accommodate larger vessels than those publicized by British Waterways for the rest of the canal. This allowed the company to design vessels of considerably greater capacity than had previously been considered possible.
By surveying each bridge, pinch point, sharp corner and lock on the canal between the loading and unloading points Land & Water were able to maximize the vessel size. Then, having established the critical craft dimensions (length 23.6m, width 4.25m and depth 1.65m), the company undertook a feasibility study on the removal of the conventional boat ‘skeleton’ (reinforcement between the carrying hold floor and the underside of the boat) and its replacement with a reinforced 10mm thick single-skin floor, thereby saving weight and cost.
The feasibility study also considered the shape of the bow and the need for a minimal bow wave when cruising on the well inhabited waterway. A further consideration was the need to mitigate labour costs, so the study looked at the design requirements necessary to produce a vessel that could be operated safely by a single crewman.
Draft drawings were submitted to British Waterways for approval in October 2002 and construction of the boats commenced in January 2003, once the project contract had been signed. Ongoing refinements and modifications were made during the construction process, resulting in the production of a safe, modern and highly manoeuvrable craft.
Particular features of note include:
Safety
Each vessel is fitted with the following safety features:
- a novel ‘man overboard’ device fitted to all life jackets. If a life jacket enters the water, electronic tags trigger audible and visual alarms on the vessel and simultaneously send an SOS message identifying which employee is in the water to the second vessel’s skipper, the local British Waterways officer and Land & Water Services’ safety advisor
- GPS tracking for pinpoint location monitoring via the Internet
- a bow-mounted video camera and in-cab monitor which allows the skipper to view the water directly under the bow when the unladen vessel is navigating ‘lightship’
- a long-range CB radio operating on a common frequency with Harleyford Aggregates
- two-tone claxons, flashing beacons and working lights (for winter working)
- an elevated wheelhouse to provide the skipper with 360° vision
- the latest technology in vibrationless transmission couplings and hydraulic control to mitigate vibrations and operator discomfort.
In addition to individual safety features, all the design works and stability calculations were checked and authorized by accredited marine architects. Both vessels carry a Class 4 work boat certificate and have been evaluated and approved for use for inland navigations, estuaries and inshore maritime waters. In addition, each vessel conforms in full to the prescriptions of the British Waterways and Environment Agency Boat Safety Scheme.
Manoeuvrability and wave mitigation
- steerage and propulsion is delivered through a patented Schottel unit, which is shrouded by a Kort nozzle. The Schottel unit affords forward propulsion through a conventional propeller but, uniquely, rotates through 360° to obviate the need for a rudder. This method of steerage provides the vessels with the ability to manoeuvre sideways and backwards under full control. In addition, the Kort nozzle protects the Schottel unit from stray debris in the canal and can be cleaned by reverse thrusting the Schottel unit
- further steerage is provided by a bow-mounted 25hp bow thruster that allows parallel manoeuvring at lock structures
- control of the steering units is provided by hydraulic joysticks (as opposed to a conventional wheel), while an electronic indicator in the cab denotes the direction of the Schottel thrust
- the entire underside of the stern of the vessel incorporates a stepped void which is designed to afford the Schottel maximum water flow during passage to mitigate stern turbidity
- repeated design checks and modelling have resulted in the introduction of a two-stage curved bow.
Carrying capacity
- an actual design capacity of 100–110 tonnes was achieved (the previous maximum capacity thought possible on the Grand Union Canal was 70 tonnes)
- a special single-skinned hold floor affords the vessel maximum carrying capacity
- skeletal reinforcement to the load hold reduces side-plate thickness to 8mm and increases carrying capacity
- enhanced buoyancy through a bespoke bow design increases capacity significantly.
Unloading excavator and wharf facilities (West Drayton)
Mindful of the former uses of the Hanson Aggregates site and with the benefit of research using historic land-use maps, together with a considerable amount of exploratory site investigation, Land & Water Services were able to develop an unloading facility that accommodated the requirements of the fully laden barges and integrated with the operating requirements of Hanson Aggregates.
The final solution included the demolition of a number of redundant mineral storage bins along the canal bank to allow the construction of a concrete plinth for the sighting of a specialist long-reach excavator. The size, reach and operating capacity of the excavator and grab bucket was optimized to suit rapid barge unloading while retaining the ability to reach two new, separate, mineral storage bunkers. These bunkers were designed to accommodate a feed from the barge/excavator on the canal side and to retain easy unhindered access for the safe operation of Hanson Aggregates’ loading shovels from the landward side.
With an average of four boat movements a day between Denham and West Drayton, each 5h round trip will have negligible impact on the waterway environment but will ultimately result in the removal of the equivalent of 45,000 lorry loads from west London’s congested roads over the next seven years, bringing genuine local benefits without compromising the canal’s role as a national leisure and environmental asset.