Wolf Minerals Start Production at Britain's First New Metal Mine for 45 Years
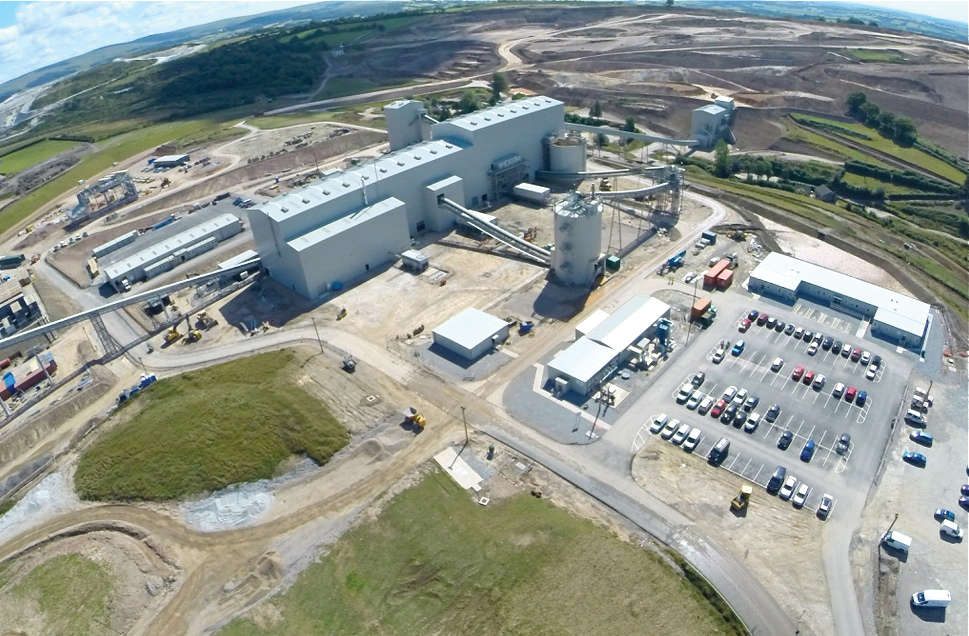
First published in the March 2016 issue of Quarry Management as Ramping-up at Drakelands
A new era dawns for the Hemerdon tungsten and tin project as Britain’s first new metal mine for 45 years gears up for full production
With the continued decline of year-on-year average commodity prices leaving many metal mining firms facing the prospect of serious cash burn, Wolf Minerals, the company behind the Hemerdon tungsten and tin project, near Plymouth, in Devon, have recently secured a new £25 million equity facility from Resource Capital Fund VI. This standby facility will help strengthen the company’s balance sheet as the processing plant at the recently opened Drakelands open-pit mine, at Hemerdon, gears up for full production.
Commenting on the establishment of the equity facility, Wolf Minerals’ managing director, Russell Clark, said it would enable the company to focus on ‘ramping-up’ the processing plant at a time which has seen the price of tungsten fall by almost 40% since construction of the plant commenced in March 2014, with drawdowns being used to support operations at the mine and facilitate debt repayments.
To date, Wolf Minerals have invested more than £140 million in the project, creating more than 200 permanent jobs and including around 15% female staff among the workforce. The mine’s official opening ceremony took place on 17 September 2015 following an 18-month construction phase, which, at its peak, involved more than 600 people. Following the start of wet commissioning in June 2015, during the September quarter the entire processing plant was handed over to Wolf Minerals from the project’s main contractor, GR Engineering Services.
Since then, Wolf Minerals have been ramping-up towards full production, with design throughput expected to be achieved in early 2016. For the past six months the mine and processing plant have been operating on a seven-days-a-week trial basis, which is due to end this month (March 2016). If the trial proves successful, the company will apply to make the arrangement permanent, thereby boosting the available operating time by more than 27% compared with the original permission for a
51/2-day working week. This will allow Wolf Minerals to produce additional volumes without further capital expenditure, thereby providing the opportunity to reduce operating costs and pushing the operation further down the tungsten concentrate production cost curve.
Drakelands is the first new metal mine to be opened in Britain for 45 years and the site is recognized by the British Geological Survey as the fourth largest tungsten resource in the world. At full capacity, annual production at the mine is expected to reach 5,000 tonnes of tungsten concentrate (WO3) and 1,000 tonnes of tin concentrate (Sn), with revenues split 90% and 10% respectively. Binding tungsten concentrate off-take contracts are in place for 80% of the project’s production for a five-year term with leading US processors Global Tungsten & Powders (Plansee) and Austria-based Wolfram Bergbau und Hutten (Sandvik). A tin off-take agreement with Traxys is also in place.
As the hardest of all metals, tungsten has no substitutes. It is heavier than gold, non-corrosive, and has a very high melting point (c.3,420°C). The European Commission has named it as one of 14 ‘critical raw minerals’ that are essential to the economy of the EU. Vital to range of industrial, mining and agricultural applications, its primary use is in cutting tools (cemented carbides), whilst other key uses include steel alloys, metal products, light bulbs and drill bits, and new/emerging applications include smart glass, batteries and nuclear fusion. Current global demand for tungsten amounts to around 100,000 tonnes per annum, and it is anticipated that in excess of 20% of the Western world’s needs will be met by the Hemerdon project.
Drakelands Mine history
The discovery of tungsten near Hemerdon dates back to 1867. The first significant workings took place around the time of the First and Second World Wars, when relatively small-scale processing plants were built and put into production. Operations ceased in 1944 following the resumption of shipments of tungsten from overseas.
Attempts to reopen the mine during the 1960s and early 1970s proved unsuccessful until American mining company AMAX became involved and a significant programme of exploratory drilling got under way in 1977. Further drilling was completed in the 1980s and planning permission was granted by Devon County Council in 1986, subject to stringent conditions governing the development and operation of the mine. However, due to a fall in the price of tungsten at that time, AMAX pulled out and the project was discontinued until 2007 when Wolf Minerals – a specialty metals mining and development company listed on both the Australian and London stock exchanges – became involved. They entered into an option agreement with the landowners to acquire a 40-year lease to the mineral rights and rights to mine the Drakelands ore body.
Updated planning permission to mine tungsten at Hemerdon until 2021 was approved by Devon County Council and the Secretary of State for Communities and Local Government in 2011, after which Wolf Minerals went on to assemble an international finance and investment package, including both debt and equity, to allow the £140 million project to be built. Following detailed engineering design work during 2013, work to construct the mine, its processing plant and associated infrastructure commenced the following year. The company is currently seeking a
15-year extension to its planning permission that would see mining operations continue until 2036.
Construction phase
In 2013, GR Engineering Services Ltd (GRES), an Australian-based firm with global experience in the execution and delivery of engineering, procurement and construction (EPC) projects, were awarded the £75 million, fixed-price, fixed-term contract to build the Drakelands Mine processing plant and associated infrastructure.
The plant construction phase commenced in mid-March 2014 and involved an extensive list of sub-contractors and process equipment suppliers appointed by GRES, including many familiar names such as Centristic, Don Valley, Eriez Magnetics, Ersel, Hewitt Robins, Horizon, Metso, Sandvik, Schneider Electric, Sepro and VEGA Controls. Despite the huge scale of the undertaking, in June 2015 the processing plant was completed on schedule, on budget and with no lost-time incidents, ready for a three-month wet commissioning phase ahead of the official opening ceremony in September 2015.
Mining operations
Most of the valuable tungsten and tin at the Drakelands Mine is dispersed throughout a complex ‘stockwork’ of randomly orientated quartz veins within the granite ore body. With little or no overburden covering the site, the granite mass is exposed at surface and well weathered to a depth of 30–40m, making mechanical excavation possible for much of this upper section. Once extraction advances below the weathered horizons more extensive drilling and blasting operations will be required.
Extraction of the ore body is being carried out using open-pit mining methods. Ultimately, the open pit measuring some 850m in length by 450m in width will reach a depth of 260m. Exploratory drilling has identified around 35.7 million tonnes of proven or probable ore reserves with mineralization to a depth of at least 400m, ie some 140m or more below the final base of the mine. With a potential southerly extension to the pit, or even underground operations, Wolf Minerals believe deeper mining of the site may be possible in the future.
In 2013, the major mining services contract at Drakelands, which is worth £85 million over five years and will involve the excavation and haulage of some 45 million tonnes of ore and waste rock or ‘killas’ (metamorphosed sedimentary country rock), was awarded to bulk earthmoving specialists and major plant operators CA Blackwell (recently acquired by Hargreaves Services). An estimated 3 million tonnes of ore and 7 million tonnes of waste will be mined from the site annually.
The waste material is loaded by excavators on to dumptrucks and driven, via internal haul roads, to the Drakelands mine waste facility (MWF) on nearby Crownhill Down, with fines slurry being pumped, via pipeline, to the MWF’s tailings settlement area. Meanwhile, mineral-bearing ore removed from the pit is delivered by dumptruck to the processing plant where it is crushed and ground to liberate the tungsten and tin, which are then separated and concentrated using various gravity-based methods.
Processing operations
At the processing plant, the ore is loaded into the run-of-mine (ROM) bin and fed to a crushing and screening circuit that comprises hybrid primary and secondary roll crushers, a rotary scrubber and vibrating screens. Oversize from the scrubber trommel is sent to tertiary cone crushers operated in closed circuit with the scrubber screen. Fines from the scrubber screen are separated on a product screen. All –9mm +0.5mm material is directed to the dense-media separation (DMS) feed bin, while the –0.5mm fines gravitate to the fines storage tank.
The DMS plant features primary, secondary and scavenger concentration with intermediate float product reduced in size by a primary ball mill operating in closed circuit with a vibrating screen. Final DMS concentrate containing approximately 40% WO3 is separately milled down to –0.5mm.
In the fines gravity circuit the –0.5mm fines from the crushing, washing and screening circuit are de-slimed in two stages using 500mm and 250mm cyclones. Secondary de-slime cyclone underflow is pumped to spiral concentrators operating in rougher, middlings and cleaner configuration. Cleaner spiral concentrates are further upgraded by three stages of Holman Wilfley shaking tables with intermediate sizing to produce a recleaner table concentrate containing around 40% WO3.
The flotation conditioner receives concentrate from both the fines gravity circuit and from the DMS concentrate regrind mill. Sulphide minerals, including arsenopyrite, are removed by flotation and the tailings are filtered and dried before being sent to a reduction kiln.
The reduction kiln converts haematite to magnetite which is removed using a low-intensity magnetic separator (LIMS). Non-magnetics are sent to high-intensity magnetic separators (HIMS) where the wolframite is recovered as a magnetic concentrate containing 62–65% WO3. HIMS non-magnetics are tabled to remove any remaining gangue to yield a final tin concentrate containing a minimum 40% Sn.
Approximately 5,000 tonnes of tungsten concentrate and 1,000 tonnes of tin concentrate will be produced each year – representing approximately one truck load a day for export to specialist customers in Europe, the US and Asia.
Mine waste facility
The operations at Drakelands Mine result in a significant volume of both coarse and fine waste. This is delivered to the site’s purpose-built mine waste facility (MWF) at nearby Crownhill Down, which is situated close to three of the southernmost china clay workings and mine waste facilities associated with the Lee Moor china clay mining area.
Designed to be inherently stable, the 175ha MWF will provide some 30 million m3 of waste rock storage and 10 million m3 of tailings storage. The facility consists of a rock-fill embankment progressively constructed from run-of-mine waste. Finer residues (tailings) are contained within this embankment and allowed to settle, with the excess water being pumped back to the processing plant for recycling.
As well as its settlement ponds, the MWF includes other necessary infrastructure such as emergency spillways, decant structures, tailings and return water pipelines, and seepage control systems – all designed and constructed to the latest national and international guidelines and statutory requirements. An additional embankment dam has been constructed immediately downstream of the MWF to provide an additional process water supply and ultimate control of all site run-off from Crownhill Down.
Environment
Wolf Minerals are committed to their responsibilities to the environment and have made a significant investment in designing a modern mine with systems and procedures to ensure best-possible environmental management. The mine has been certified ISO 14001 compliant for its environmental management systems, and strict conditions within the mine’s planning permission cover matters such as hours of operation, traffic, noise and dust.
A number of Environment Agency permits are also in place covering the technical and environmental operations of the mine, including the extraction and discharge of water and construction and operation of the mine waste facility. The latter permit is aligned with the recently introduced European Mine Waste Directive and is the first of its type to be issued in the UK by the Environmental Agency.
As part of the mine development, Wolf Minerals have already planted 40,000 trees (in total some 1 million trees will be planted during the course of the project), constructed new bridleways and footpaths, established biodiversity enhancement zones, and built three bat roosts.
An ongoing programme of environmental monitoring and reporting by Wolf Minerals, Devon County Council, the Environment Agency and independently appointed experts will ensure that the mine and its associated facilities continue to operate to the highest standards and continue to meet all statutory requirements.
- Subscribe to Quarry Management, the monthly journal for the mineral products industry, to read articles before they appear on Agg-Net.com