The Bray Triangle
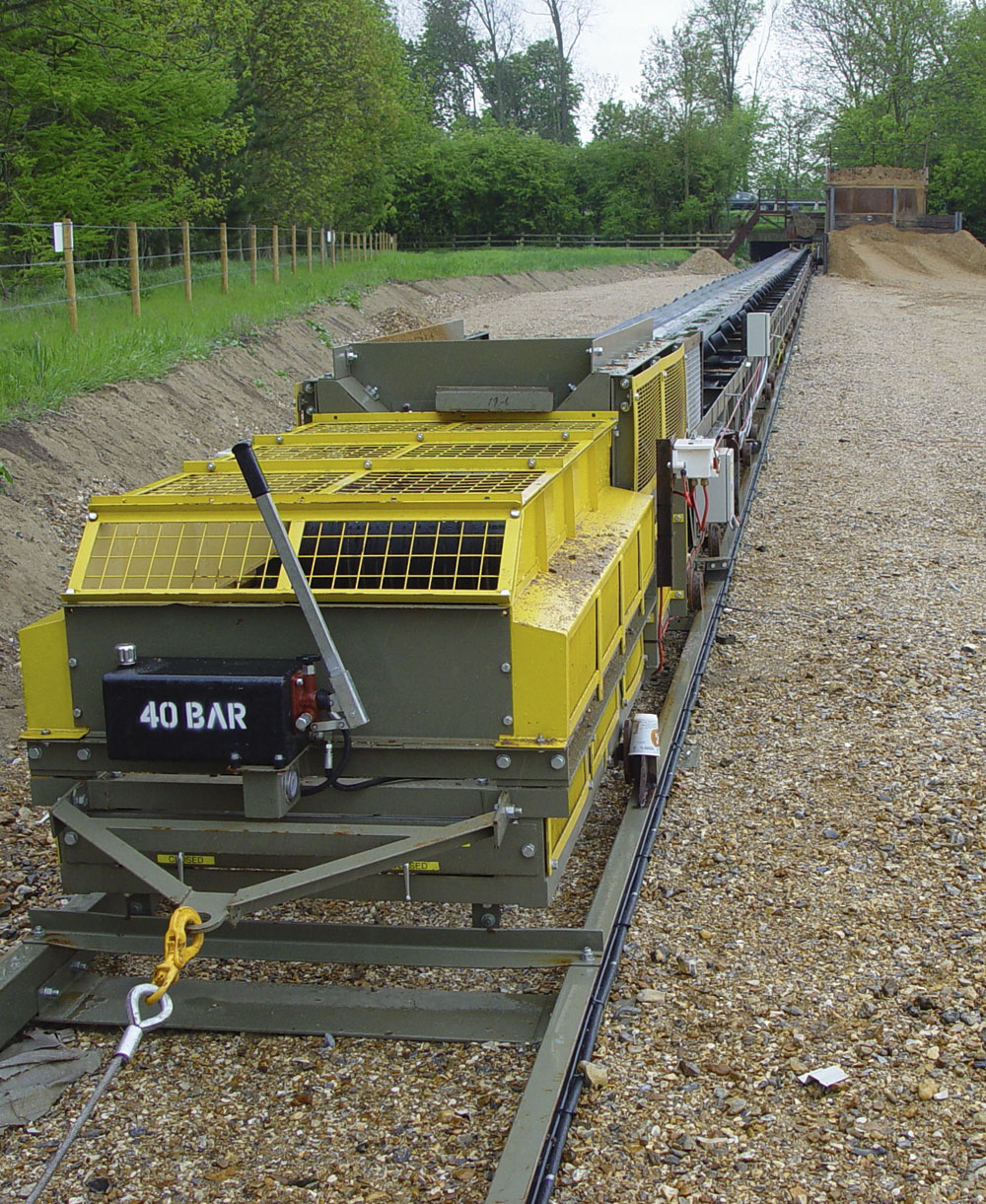
Ingenious conveyor solution opens up new reserves for Summerleaze
Earlier this year Maidenhead-based independent quarry operators Summerleaze commenced the extraction of sand and gravel from a parcel of freehold land south of the river Thames, between the towns of Bray and Holyport, as an extension to their previous workings in the Bray area. This newly opened extraction site is commonly referred to as the ‘Bray Triangle’, as its three main boundaries – the B3028 Upper Bray Road, the M4 motorway and The Cut (a man-made waterway between Maidenhead town centre and the river Thames at Bray Marina) – enclose a triangular shaped tract of agricultural land.
Summerleaze have a long history of sand and gravel extraction in this area and for many years have operated a fixed sand and gravel processing plant at their Monkey Island Lane facility, about 1km to the east of the new extraction site. Originally, this plant served the adjacent extraction areas that created the lakes north and south of The Cut, which are now used for sailing, fishing, walking and nature conservation. More recently, sand and gravel from the Eton Rowing Course at Dorney Reach was transported to the processing plant via a field conveyor system incorporating a specially designed bridge over the river Thames. Lately, sand and gravel has been imported to the site by road from a quarry near Taplow, in Buckinghamshire.
With a requirement for further local reserves to provide the majority of sand and gravel supplies for the Monkey Island Lane plant, in order to reduce the dependence on imported material, Summerleaze considered a number of alternative sites in the area before finally deciding on the Bray Triangle as the best option in the short term. Although not earmarked as a Preferred Area in the Berkshire Minerals Local Plan, the very limited nature of any potential environmental impacts of this extension resulted in the company’s planning application being granted consent at appeal in 2008.
The total permitted area, which encompasses both the mineral working site and a conveyor corridor to the processing plant, amounts to 12.6ha, although the actual extraction area covers just 7.8ha. The site contains an estimated 475,000 tonnes of sand and gravel and is being worked wet in annual phases over a three-year period at a rate of approximately 160,000 tonnes per annum. Phase 1 operations commenced earlier this year and restoration to a lake and reed beds suitable for conservation and passive recreational use is due to be completed by the end of year four.
All material extracted from the site is fed on to a 750mm wide ground conveyor for delivery to the processing plant. Comprising four separate conveyors, this 1,500m long conveyor system utilizes an existing flood water culvert to pass under the M4 motorway before crossing over and then running alongside The Cut, at the level of the river bank, eventually linking up with the existing ground conveyor associated with the construction of the Eton Rowing Course. Designed, manufactured and installed by Leicestershire-based Wileman Engineering, the new, fully interlinked ground conveyor system is key to the viability of the Bray Triangle operation, as material transport by road was ruled out under the terms of the planning permission
However, because the conveyor structure could potentially block or impede the effectiveness of the 1.3m high x 6.0m wide x 47m long flood-relief culvert beneath the M4, the planning consent called for a 90m section of the ground conveyor to be fully retractable, allowing it to be withdrawn from the culvert each night and during periods of high flood risk, then moved back into position during normal working hours or after a flood event has subsided. This required an unusual and ingenious solution involving a travelling conveyor supported on steel wheels that could be moved back and forth along a 165m long rail track.
Retractable conveyor
Water levels in The Cut are monitored continuously by a sensor, as the waterway can reach full flood and overspill its banks within relatively short period of time (around 5–6h). If a flood event threatens during site working hours, a flashing beacon mounted on top of the conveyor system control cabinet warns the loader driver that the conveyor needs to be retracted from the culvert.
Two 4kW Huchez electric winches, one mounted at the head end of the rail track and the other at the tail end, are used to move the travelling conveyor. Both winches have a fixed power supply and are controlled via an electronic inverter system that utilizes bespoke software to prevent over-tensioning of the winch wires. As one winch reels in and the other spools out, the electronic inverter monitors the load and releases the wire accordingly to maintain the correct tension on the winch wires at either end of the conveyor. The operation of the winches is carried out at the control cabin by a single switch, allowing ease of use. The total time to extract the conveyor is 9 min.
Fed by an existing feed hopper arrangement, the travelling conveyor itself is capable of receiving and handling up to 300 tonnes/h of as dug sand and gravel. It is constructed from rolled-steel sections, formed into a lattice-frame boom fitted with 150mm diameter flanged, flat-tread, steel channel wheels. These run on PFC channel rails supported on steel sleepers pegged to a compacted base, except in one particular section of the culvert where the presence of a buried gas main precludes ground fixing. Here, the rail track is attached to the side of the concrete culvert by restraining members connected to tensioning plates to maintain the correct rail gauge.
A series of standard bogies with flexible rubber-lined hinges at the joints allow the conveyor boom to bend slightly to accommodate a gentle upward incline of the rails at the head end, while the 750mm wide, three-ply 500/3 rating (3 x 1.5mm thickness) conveyor belt runs on Rulmeca three-roll troughing idler sets mounted in fixed-angle transoms, with impact idler sets fitted at the tail-end feed point. The conveyor drive is provided by a 500mm diameter Rulmeca motorized head drum, rated at 15kW, which achieves a belt speed of 2m/s. The return idlers consist of 100mm diameter plain rollers supported by bolted end brackets. A hand-operated hydraulic tensioning device at the tail drum allows for the rapid release of belt tension for conveyor movement, when required. Because of the regular movement of the new conveyor, power supplies for the conveyor drive drum, safety pull-wires and conveyor motion sensor are delivered via a series of plug-in connectors.
The new conveyor system with its ingenious retractable section has allowed Summerleaze to open up the Bray Triangle as the main source of supply for the company’s Monkey Island Lane processing plant for the immediate future. Making use of this local source of material provides a number of significant benefits: it maintains the continuity of operations at Monkey Island Lane, which has the benefit of a permanent planning permission; it minimizes the need for imported materials and thereby helps reduce road traffic movements; it delays any major development of alternative sites in the region; and ultimately, in a few years time, it will create a lake suitable for nature conservation and passive recreational use that will enhance the area.
Acknowledgement
The editor wishes to thank Mike Lowe, director of Summerleaze, and Matthew Joyce of Wileman Engineers, for their help in preparing this article.