Stone mining on the Isle of Portland
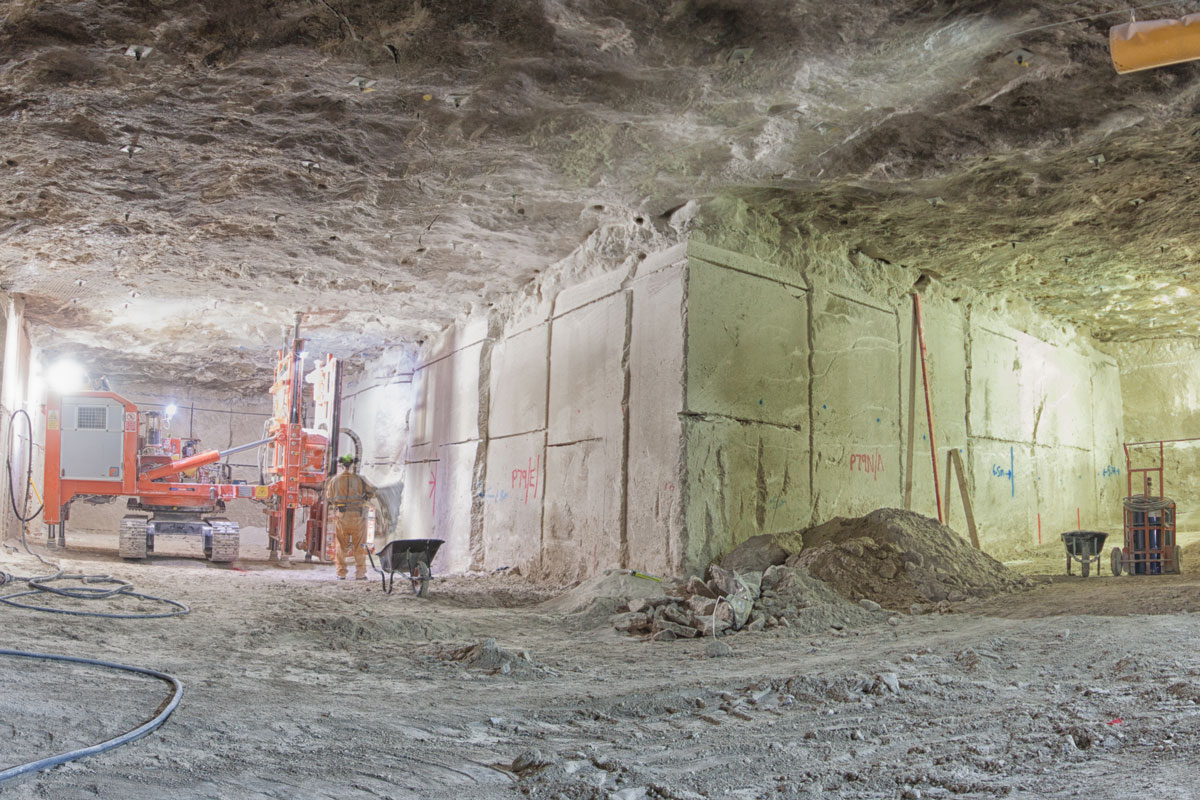
First published in the October 2021 issue of Quarry Management as Between a Rock and a Hard Place
Mark Godden of Albion Stone discusses stone mining on the Isle of Portland
Situated in the middle of Dorset’s Jurassic Coast, Portland truly is an island of stone, where the close ties between its inhabitants and the rocks upon which they live, stretch back through many centuries.
History
During the Bronze and Iron ages, skilfully knapped tools, produced using chert nodules recovered from Portland’s precipitous sea cliffs, were thought to have been manufactured on the island and then widely traded across southern England.
The first known use of Portland’s limestone was by the Romans. Many expertly hewn stone coffins (or sarcophagi) with well-fitting stone lids have been unearthed on Portland over the years. The skills necessary to produce these would have been considerable and, tantalisingly, this hints at the presence of a proto-stone industry on the island, with a surprising degree of sophistication.
In medieval times, the first stone bridge to span the river Thames in London was constructed from Portland stone that would have been hauled along England’s south coast and up the river, using barges.
Sir Christopher Wren used stone from Portland to reconstruct buildings in London following the devastating fire of 1666, which imbued its enduring pedigree as a much-loved building material within the capital.
During the last few hundred years, stone quarrying on Portland became increasingly intense. Huge quantities of Portland’s white limestone have been used to construct literally thousands of buildings and monuments in London and many other provincial towns and cities within the UK – and across the wider world.
Geology
Portland limestone is an oolite. It is composed of billions of microscopic spheres of calcium carbonate which naturally accreted in huge shoals on the floor of a warm, sub-tropical sea, at the very end of the Jurassic period, some 145 million years ago. At this time, what is now Portland was situated much closer to the equator than Portland is today. It was here, under warm, sub-tropical conditions, that the natural processes which result in the precipitation of calcium carbonate from sea water and the subsequent formation of the oolitic Portland limestone, took place.
During the time that the Portland limestone was being laid down on the sea floor, the depth of the overlying sea water was generally decreasing. As time moved on, environmental conditions on the seabed changed because of the reducing water depth, and these changes have been recorded as textural changes within the rocks. In general, the density of comminuted shell fragments and other fossiliferous material increases from bottom to top through the Portland Freestone Series. The Basebed contains very few recognizable fossils, the Whitbed contains variable concentrations of fossil shells, and the Roach is packed full of the easily identifiable remains of bivalves and gastropods (fig. 2). The late-Jurassic strata on Portland gently dip to the south-east because the island forms the southern limb of the Weymouth anticline. The Portland limestone contains several systematic joint sets but no vertically displaced faults.
Mining
Centuries of intensive opencast quarrying has left an indelible mark upon the surface of Portland. Vastly increased levels of house building and other pressures on land use, along with increased levels of environmental awareness amongst residents, have conspired to make the winning of planning permissions to dig new ‘greenfield’ quarries on Portland practically impossible.
It was under these circumstances, around 25 years ago, that Albion Stone first considered underground mining as a potential way to secure much-needed additional reserves of dimension stone. Mining would allow the extraction of valuable stone from areas where opencast quarrying would simply not be possible because of the inescapable proximity of sensitive environmental receptors. The mining of stone is a bit like ‘keyhole surgery’ compared with opencast quarrying (fig. 1). Stone mining yields minimal environmental impacts to those living and working nearby.
Following a huge amount of preparation and planning, a small, experimental room-and-pillar mine was developed in the south-west corner of Bowers Quarry during 2002. This operation was designed as a trial, to gauge the viability of underground stone mining on Portland (from both a geotechnical and a financial perspective). Before this time, no underground stone mining of any kind had ever been attempted on Portland.
A great deal of investigative geotechnical work was undertaken in conjunction with Albion Stone’s planning consultants, Wardell Armstrong, before any mining commenced. This strongly suggested that systematically supported roadways 6.5m wide would remain stable under all reasonably foreseeable circumstances, and pillars of 6.5m2 would be strong enough to support the gravitational load of the overlying strata. This led to the adoption of a maximum aerial extraction ratio of 75% for Jordans Mine. This means that when considered in terms of area, a minimum of a quarter of the beds being won are left behind as roof-supporting pillars (fig. 4).
After many incremental tweaks to the working methods used, the trial mine ultimately proved to be successful. Building on this experience and taking all the lessons learned during the trial mine’s creation, a new production mine was begun in the long-abandoned Jordans Quarry during 2008. The orientation of the redundant vertical quarry face was geotechnically perfect for the establishment of two new mine portals, from which tunnels could be driven horizontally into the in-situ beds of limestone lying behind (fig. 3).
Work at Jordans Mine initially concentrated on the uppermost Roach and Whitbed seams, which were removed together, in the first two 4m high drivages. The mine’s roof horizon is coincident with a weak stratum called the ‘Basal Dirt Bed’, which is a thin palaeosol separating the underlying oolitic Portland limestone from the overlying lacustrine thrombolite, that is colloquially known as Cap. Cap is a tough rock which makes for a very competent mine roof but has no value as dimension stone because of its relative hardness and often vuggy character.
Following a few years of Whitbed only extraction, work began to recover Basebed from within Jordans Mine. To access the Basebed, two 10° ramps were driven downwards from the base of the Whitbed horizon, through the Curf (a generally micritic and chertified bed of limestone) and through the Basebed itself (fig. 6). The ramps eventually extended down to the bottom of the Basebed, creating two vertical faces through it (fig. 7). Once these free faces had been created, bench mining of the Curf, followed by more bench mining to recover the highly prized Basebed, could commence.
Bench mining of the Curf and Basebed is undertaken using three Fantini bench saws (fig. 5). These are mainly used to make advanced vertical cuts around the pillars. Fantini GU50 mining machines are used to make horizontal cuts at the bottom of vertical working faces for the insertion of hydro-bags. Curf and Basebed extraction follows the exact footprint of the headings that were previously driven into the Whitbed. The lowering of the mine’s floor horizon (after the extraction of the Curf and the Basebed) results in 9.5m high pillars and roadways. Backfilling of worked-out areas of the mine is undertaken as soon as possible after all the usable stone has been extracted, mainly using offcuts and uneconomic rock generated during the mining process.
Roof support is provided by regularly spaced, 2.4m long x 30mm diameter rock bolts, which are installed vertically upwards into the mine’s roof beam in a pre-determined pattern. The bolts are held in place using a specialist polyester resin designed to transfer gravitational loads from the rock mass to the bolts. The aim of the bolts is to confine the roof and, therefore, reduce the chance of roof beam failure. Bolts are installed using a state-of-the-art bolting rig supplied by Epiroc (fig. 8). This machine allows the operator to install bolts at the prescribed density from within a protective cab, which is positioned well behind the area of roof being supported. The integrity of the mine’s roof is continuously monitored using telltales and accurate surveying techniques to ensure it remains stable.
Jordans Mine is ventilated using a 2m diameter, electrically powered fan, capable of delivering up to 70m3 of fresh air into the workings each second. The mine is ventilated to maintain a healthy, respirable atmosphere underground and to flush diesel exhaust emissions, dust, and radon gas out of the mine.
Mining is undertaken using six Fantini GU 50 mining machines that are owned and operated by Albion Stone. Fitted with diamond-tipped, chainsaw-type blades, these machines are used to make 40mm wide x 1.8m deep cuts into working faces within the mine (fig. 9).
Stone from cut faces is displaced using ‘hydro-bags’, which are 1m2 flat envelopes, made from high-tensile steel, that can be inserted into cuts and then forcefully inflated with water to displace the stone (fig. 10).
Loosened blocks of dimension stone weighing up to 20 tonnes are taken out of the mine using one of three Volvo L150 loading shovels, which have been specially adapted to work underground. These can be equipped with either rock buckets or very-heavy-duty block-handling forks, which are easily exchanged, as required, using a hydraulic quick-release mechanism (fig. 11).
The mine produces several thousand cubic metres of excellent-quality dimension stone annually. Much of this stone is used within Albion Stone’s own masonry works located close to the mine. The balance is sold to external masonry contractors.
The health and safety of employees and visitors to the mine is Albion Stone’s top priority. The mine is equipped with a fully stocked rescue room. An in-house rescue team is always available on site and its members, operating under the umbrella of MRSL (the former Mines Rescue Service), are fully trained in the use of breathing apparatus and other mine rescue techniques. Employees also take part in regular mock emergencies and mine evacuation exercises.
The future
Jordans Mine has an estimated remaining life expectancy of around 15 years. Work to develop a completely new mine at Stoneshill – a 50-acre site situated about 1km south of Jordans Mine – is currently well under way (fig. 12). Stoneshill Mine is expected to yield high-quality blocks of Portland stone for many decades to come, thus providing the literal building blocks for many, as-yet unimagined, architectural masterpieces of the future.
- Subscribe to Quarry Management, the monthly journal for the mineral products industry, to read articles before they appear on Agg-Net.com