Bespoke Volvo for Albion Stone
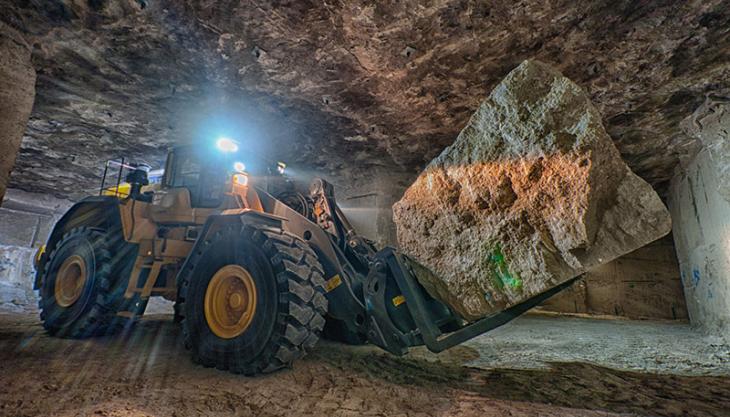
Brand new L150H loading shovel for Jordans underground stone mine on the Isle of Portland
A NEW 25-tonne loading shovel has been selected by Albion Stone after extensive research into the feasibility of introducing this size of machine into the general working and modus operandi at their underground Jordans stone mine on the Isle of Portland, in Dorset.
‘We wanted a robust and productive machine to replace our somewhat unreliable telehandler, but one of the important criteria was the overall height of the machine,’ said mine manager Mark Godden. ‘Having looked at what was available and researching our options, we approached the team at Volvo to come up with the right machine and specification for the job.’
The initial approach was to trial what was deemed to be the optimum-sized loader in the application and so a Volvo L150G was sent in on an extended demonstration. The machine not only demonstrated its superior power and tractive effort over the resident telehandler but, more importantly, the significant breakout torque available – thanks to Volvo’s patented TP loader linkage when fitted with block handling forks to prise the partly sawn blocks from the mine face.
The solution to the overall height issue would be overcome by the ability of Volvo to reduce the cab height by 350mm through a third party, Kiruna Industri, located in the far north of Sweden.
Thus, with the requisite boxes ticked, the order was placed. The whole process from initial enquiry to machine delivery took just under 12 months and the net result is a bespoke loading shovel perfectly matched to the needs of Albion Stone’s production requirements at Jordans mine.
Besides the reduced height of the operator’s compartment, the L150H features a hydraulic quick-hitch to facilitate the easy changeover of attachments. These include: a standard 3.8m3 general-purpose bucket for cleaning up; heavy-duty 1,500mm block forks capable of handling blocks weighing from 7 to 12 tonnes; and uniquely designed ‘upside-down’ forks.
Whilst the L150H has plenty of breakout torque to prise the majority of part-sawn blocks from the mine face, there is the occasional need to encourage some more awkward blocks away from the face – particularly from the mine roof – and this is accomplished utilizing the bespoke fork attachment.
Launched at this year’s Hillhead exhibition, the L150H features a 13-litre stage IV final engine that develops 300hp between 1,300 and 1,400 rev/min. The machine also benefits from Volvo designed and manufactured driveline components including Optishift with torque converter lock-up and Volvo’s patented reverse by braking feature – all designed to offer considerable fuel savings each shift.
Fuel savings are further enhanced by the Volvo Eco pedal, which encourages the operator to run the machine at its optimum rev/min in the engine’s torque curve.
Besides its main activity of extracting stone blocks from situ, the new L150H carries the blocks to the mine entrance where they are sorted and cut to customer requirements. The machine then carries the sawn material up to a marshalling area where it is loaded on to trailers to be transported to the cutting shops. To aid this activity, the L150H has been fitted with Volvo’s optional ride control or boom suspension system together with Bridgestone 26.5 x 25 VSDT L5 tyres.
The machine has also been equipped with additional safety features for working underground, including: a fire-suppression system; double-pole battery isolator; and a Chelwyn valve to meet mine regulations on exhaust emissions. To properly counterbalance the weights of the blocks, the machine has been fitted with an optional block-handling counterweight, while additional LED working lights fore and aft afford the operator effective light and vision when working at the mine face.
For complete peace of mind the L150H has been supplied with Volvo’s Silver customer support agreement, which includes a flexible customer-linked repair and maintenance programme tailored to Albion Stone’s needs.
Albion Stone plc have been involved with the Portland stone industry for nearly three quarters of a century, quarrying the stone from the Basebed, Whitbed, and Roach seams for more than three decades. In recent years the company has switched its extraction operations from quarrying to mining. This process has significantly reduced the operation’s environmental impacts, making Portland stone an economical yet sustainable choice that compares favourably with many alternative construction materials.