Radial Record-breaker
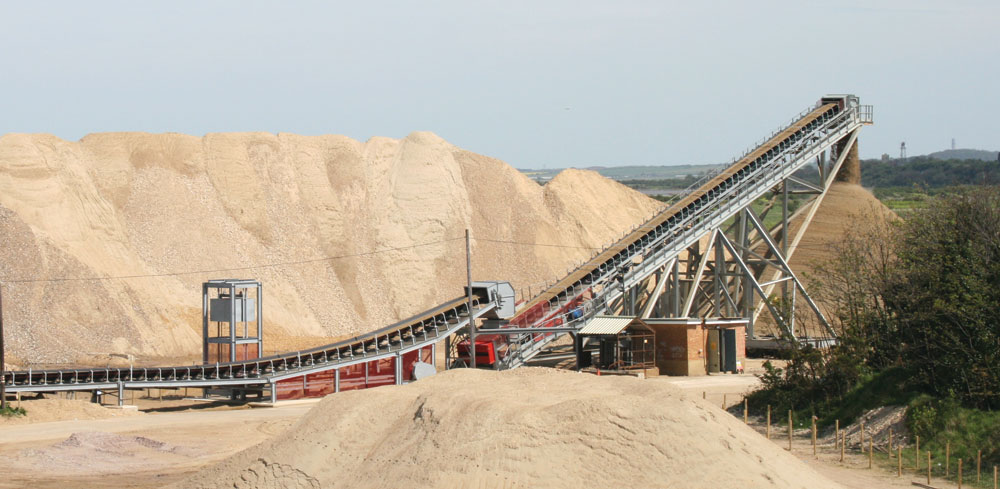
Brett Aggregates install Europe’s largest radial stockpile conveyor at Cliffe
With annual sales of more than £60 million, Brett Aggregates are one of the leading suppliers of sand and gravel (both marine and land-won), crushed rock, asphalt and recycled sub-bases to the building and civil engineering markets in London and the counties of southern and eastern England. Operating over 30 supply locations across the region and with total aggregate sales in excess of 4 million tonnes a year, the company forms a key part of the long-established and highly successful Brett Group, one of the UK’s largest independent suppliers of construction materials.
Responding to increasing customer demand, in 2007 Brett Aggregates made significant investments in their flagship marine aggregates facility on the river Thames, at Cliffe, in Kent, to improve the site’s ability to discharge and process aggregate materials. Currently handling around 1.3 million tonnes of BAD (ballast as dredged) per year, the site produces a wide range of products (40mm, 20mm, 10mm, 6mm, grit, sand etc), around 50% of which are dispatched by rail to aggregate depots throughout the South East. A further 25–30% of production is supplied to Brett Landscaping & Building Products, who also have operations at Cliffe, while the bulk of the remainder goes to Brett Concrete plants throughout the region.
Being the closest wharf to the North Sea and English Channel dredging grounds, and with a water depth of at least 7m available at all times, Cliffe is one of the favoured destinations for dredging vessels visiting the Thames wharves. However, with modern dredgers carrying cargoes of up to 10,000 tonnes and having the ability to self-discharge at rates well in excess of 2,000 tonnes/h, the site’s original ageing quayside unloading facility, with its 1,350 tonnes/h static discharge conveyor and 5,000-tonne stockpile capacity, had become a ‘choke point’ that was slowing down the unloading process and necessitating the use of two loading shovels for costly re-handling duties.
Currently, around 75% of all BAD delivered into Cliffe is landed by the 10,000-tonne capacity vessel Charlemagne, which is owned and operated by Belgian dredging firm DEME, while the bulk of the remainder is supplied by the Britannia Beaver, a 5,000-tonne capacity A-class vessel owned and operated by Brett joint-venture company Britannia Aggregates. As a condition of DEME’s current supply agreement, the Belgian operator had requested that Brett Aggregates provide an unloading system capable of matching the Charlemagne’s 2,500–2,800 tonnes/h discharge capability.
With significant structural repairs needed to bring the old conveyor back up to a suitable standard, and with a view to accommodating even larger vessels in the future, Brett Aggregates took the decision to invest £750,000 in a brand new system capable of achieving a discharge rate of up to 3,500 tonnes/h (peak) and offering a significantly increased primary stockpile capacity of 50,000 tonnes. This would not only speed up ship turnaround times and improve the company’s ability to negotiate on costs, but would also avoid the need for costly double handling by allowing several ships to discharge without having to move material around using loading shovels. Moreover, a system with the ability to create a number of larger, discrete stockpiles would permit better blending of the sands and gravels from different dredging areas, giving a more consistent feed to the processing plant at Cliffe and achieving a more even split on the processed materials. As well as the investment in the unloading system, Brett Aggregates have spent a further £150,000 at Cliffe to create extra storage space for an additional 400,000 tonnes of BAD.
Mark Wraight, area production manager for Brett Aggregates, commented: ‘Typically, we struggle to get ships in during the winter months due to bad weather, therefore our stocks for processing deplete quickly and need to be built up again during the spring and summer months. With demand forecast to increase significantly over the coming years, the new quick-discharge facilities and significantly expanded storage capacity will allow us to accept as many ships as are available, and at relatively short notice.’
New unloading system
Initial ideas and designs for the new unloading system were sketched out in late 2006 and, having quickly ruled out the preferred solution – a tripper-type system – due to excessive cost and the limited footprint available, Brett opted for a large radial stockpiling conveyor as the most practical and cost-effective solution. Following in-depth discussions with various conveyor manufacturers early last year, the contract was put out to tender and subsequently awarded to Ranskill-based Atherton Conveyors Ltd in April 2007. Working in close partnership with Brett Aggregates, they produced an initial design incorporating a large but conventional-type radial system running on a curved concrete pad.
Complications arose, however, when concurrent soil investigations revealed that the combined weight of the proposed conveyor system and its 50,000-tonne stockpile would result in a considerable amount of ground heave owing to the soft, unstable nature of the land adjacent to the river Thames. With concrete piling of the area ruled out as a possible solution to this problem, due to the additional costs involved, the ground consultants recommended that Brett Aggregates place toe weights (comprising several thousands of tonnes of BAD, contained in bulk bags) at each end of, and adjacent to, the stockpile to help prevent any rippling effect due to stockpile surge.
Atherton Conveyors were also required to rethink their original radial conveyor design and came up with a radically revised solution. The conveyor, with its robustly engineered and fully galvanized supporting framework, would now run on eight foam-filled earthmover tyres – each with a rated load-carrying capacity of 30 tonnes – mounted in two groups of four in a wide chassis specially designed to spread the weight of the structure and reduce its ground pressure. Despite the unforeseen geotechnical problem and the ensuing equipment redesign, the close working relationship between Atherton Conveyors and Brett Aggregates ensured that the project remained on schedule with completion achieved as planned at the end of September 2007.
Believed to be the largest radial conveyor of its kind currently operating in Europe, the vast new structure weighs 150 tonnes and measures 50.3m between centres. The conveyor itself is inclined at 15°, reaches a stockpiling height of 16.6m at its head drum, features double walkways with Davis Derby pull-wires along its entire length, and is fitted with a 1,400mm wide belt that operates at a speed of 2.5m/s. The belt is powered by a 220kW tandem-drive system comprising twin 110kW CMG high-efficiency motors and twin Bonfiglioli helical-bevel gearboxes via a ceramic-lagged drive drum, while the tail end of the conveyor both sits and rotates on a 1,400mm diameter slewing ring supplied by NBC Group Ltd.
At present, the radial conveyor is pulled into position by a loading shovel using towing brackets fitted at either end of its wheeled chassis section, and, with the exception of a concrete parking/tie-down pad, the entire structure runs on a radial roadway made from compacted Type 1 material. However, once Brett Aggregates are confident that the ground beneath the stockpile area has fully stabilized, a conventional concrete roadway will be laid down and a self-powered winch system will be installed for propulsion purposes.
Atherton Conveyors were also responsible for replacing the infeed conveyor linking the reception hopper/feed boot on the berthing jetty to the new radial stockpile conveyor. This involved realigning the original straight-run conveyor path by around 2°, which, in turn, required the installation of four new concrete piles in the river Thames – a task contracted out to Costain Engineering – to support the first part of the new 120m long conveyor, which now passes over the river. The belt itself, which matches the radial conveyor in terms of its width and speed (1,400mm wide and 2.5m/s respectively), incorporates a 12m loop take-up unit, a 6m high gravity weight tower, and is powered by a 150kW ceramic-lagged double-drum unit, which once again utilizes high-efficiency motor and helical-bevel gearbox technology from CMG and Bonfiglioli respectively.
In addition, both the infeed conveyor and the radial conveyor are equipped with primary and secondary scrapers on their respective head drums, and both conveyor drive systems are inverter controlled to ensure smooth, shock-free start up. Also, to meet Brett Aggregates’ desired 3,500 tonnes/h stockpiling capacity, both belts have been fitted with 5in (127mm) diameter support rollers throughout, with the two outer elements of each three-part unit installed at the unusually steep angle of 45°, in order to achieve the required tonnage on the 1,400mm wide belts. Cooper 01 bearings have also been used throughout, and all drums (drive, tail, snub, head etc) and rollers utilized on the two conveyors were constructed in house, complete with ring-lock shaft attachments, by Atherton Conveyors.
To ensure continuity of supply during the changeover, operation of Cliffe’s old jetty-mounted conveyor system was maintained while the river piling work and land-based conveyor sections were installed, after which Atherton were given a four-week ‘ship-free window’ in which to remove the old infeed conveyor and complete the installation of the new one, a challenging task which the company once again successfully managed to complete on time. As part of their work on the infeed conveyor, Atherton Conveyors also redesigned and replaced the original (and now badly corroded) steel ring beam supporting the conveyor’s 4m x 4m feed boot by welding new galvanized beams on to the four existing (and still sound) support piles.
Commenting on the success of the project, Atherton Conveyors’ managing director, Dean Atherton, said he was both delighted and honoured to have been awarded the contract at Brett Aggregates’ flagship marine aggregates operation. ‘This is definitely our most prestigious and most challenging contract to date from a design and manufacturing point of view,’ he commented. ‘And considering this is the first work we have ever done for Brett, the working relationship between the two companies has been excellent. I can say without doubt, that they are one of the best companies Atherton Conveyors have ever worked with, and we are now looking forward to further successful partnerships with the Brett Group in the future.’
Acknowledgement
The editor wishes to thank Brett Aggregates for permission to visit the site and, in particular, Mark Wraight, area production manager, and Dean Atherton for their help in preparing this report.