Old Becomes New At Cliffe Hill
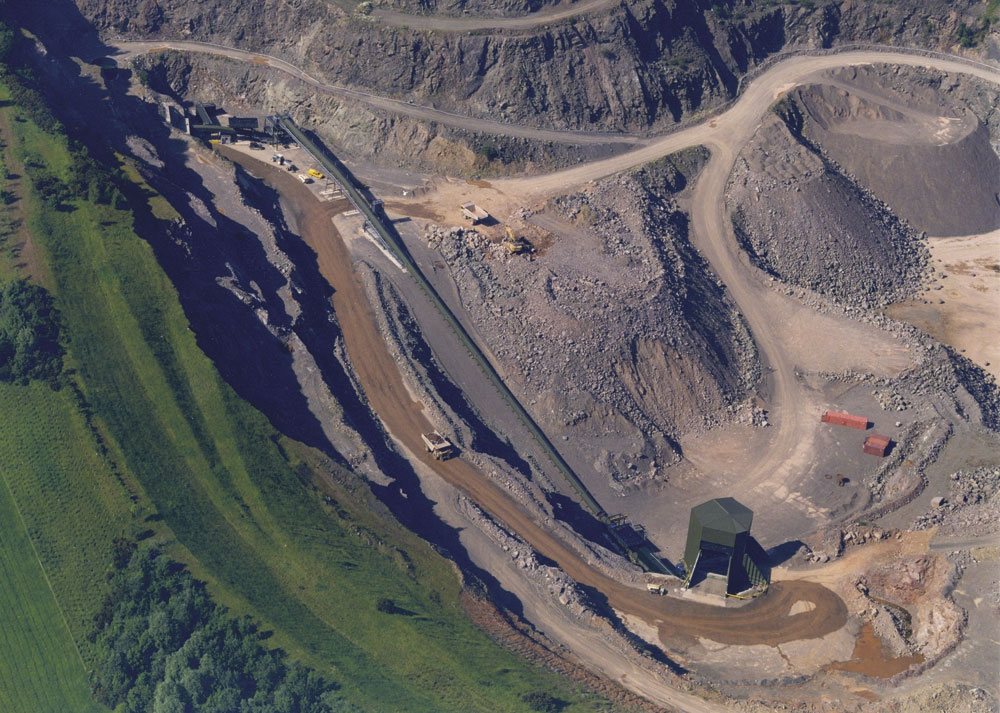
Multi-million pound redevelopment brings dormant quarry back to life
In April 2003 Quarry Management reported on progress at Midland Quarry Products’ flagship hard rock operation, near Markfield, in Leicestershire, where tunnel construction was well under way as part of an innovative scheme to link the then dormant quarry void at Old Cliffe Hill to the current operational quarry, processing plant and railhead at New Cliffe Hill, with the aim of releasing some 60 million tonnes of previously sterilized reserves of high-quality granite.
In the two-and-a-half years since then the tunnel has been completed, a new semi-mobile primary crushing plant has been installed and commissioned at Old Cliffe Hill, an extensive field conveyor system linking the two sites (via the new tunnel) has been constructed, and a huge overburden removal operation has commenced, allowing extraction and processing of the remaining reserves of stone within Old Cliffe Hill to get under way.
The return to the old site formed an integral part of the original planning permission for New Cliffe Hill secured in 1983, although no defined method of linking the two voids was outlined in the plans at that time. Subsequently, consideration was given to overland conveyors and cut-and-cover tunnels, but ultimately the most environmentally acceptable solution for the planners and local residents was a deep-level tunnel within the granite bedrock.
The ‘Joskin Tunnel’
After 10 months of drilling, blasting, scaling and rockbolting, teams of specialist engineers working from both ends of the tunnel finally achieved breakthrough on 12 June 2003, some 14 weeks ahead of schedule. A remarkable level of accuracy was achieved by the tunnellers, with the two ends of the 714m long passage being just 80mm out of alignment at the meeting point. Strict risk assessment and safety procedures during construction ensured that an equally impressive ‘zero’ lost-time incident record was maintained from start to finish.
The generally competent, fully stressed rock conditions encountered in the granite bedrock meant that anchoring the tunnel walls was largely straightforward, in accordance with Support Classification A; only one section required additional support to Classification C (ie, double rock bolts plus shotcrete). Approximately 7,000 full-column resin-bonded rock bolts were used during construction of the tunnel, some two-thirds of which was also shotcreted. Routine geotechnical inspections were conducted for a period of two years following completion, although no trace of movement was recorded in the tunnel after the first two months.
Following breakthrough in June, a further four months were spent finishing the portals and fitting the necessary services. The tunnel is now fully equipped throughout with lighting, ventilation fans, gas-monitoring and fire-detection systems, together with a two-way communication system. As a precautionary measure in the unlikely event of a fire in the tunnel, a dedicated fire-fighting line has been installed along its entire length. In addition, all trucks using the tunnel are fitted with on-board fire-suppression systems and firefighting equipment.
Measuring 9m in width and 6m in height, the tunnel accommodates both a single-lane roadway and a suspended belt conveyor. Asphalt surfacing has been laid throughout and wide aprons mark the approaches to both ends of the passage. Vehicles using the tunnel are separated from the overhead conveyor by a concrete safety barrier. The dimensions of the tunnel and roadway are such that fully laden 50-tonne articulated dumptrucks can pass through safely. Vehicle speed is restricted in the tunnel, with single-file traffic flow controlled by traffic-lights at both ends.
Electronic message display boards have also been mounted at each end of the tunnel to supply production data and critical safety information to personnel waiting to enter. Warnings of fire, gas and vehicle breakdowns are all examples of messages that can be displayed to drivers, as a part of the traffic-management system that controls movements through the tunnel.
A competition to find a name for the new tunnel resulted in numerous suggestions from the local community, with ‘Joskin’ (an old local name still used today by many residents in nearby Stanton under Bardon) being the name eventually chosen by MQP. In September 2003 over 1,000 local residents and other members of the public attended the Joskin Tunnel open day and official naming ceremony. Monthly chronicles were produced and distributed by MQP informing the local residents on progress of the scheme throughout the three-year project.
Primary crushing
On-site preparations for Old Cliffe Hill’s new semi-mobile primary crushing station included foundation work and the creation of a smooth and stable V-shaped rock slot to accommodate the plant. The latter was achieved using pre-split engineering blasting techniques, a task that proved particularly challenging owing to the granite’s tendency to break back during blasting.
The crushing station itself — the first of its kind in the UK — was designed and built by Leipzig-based MAN Takraf Fördertechnik GmbH. The steelwork for the main support structure (parts of which weigh in excess of 100 tonnes) was manufactured in Germany, while many of the lighter ancillary components were produced in Poland. On-site fabrication was carried out by a team of 14 welders and five steel erectors, although at peak times as many as 50 people were involved in the plant’s assembly. Stringent quality assurance was maintained throughout the fabrication work, with ultrasonic tests conducted on all welds.
Mounted within the massive support structure is a 54in x 77in Fuller Traylor gyratory crusher supplied by Pennsylvania-based FFE Minerals. Powered by a 450kW, 3.3kV motor supplied by ABB, the crusher is capable of reducing 1.2m3 lumps of granite down to 300mm at a rate of up to 2,500 tonnes/h. A similar machine is currently used for primary crushing duties at New Cliffe Hill, providing MQP with commonality of parts and spares.
Other key features of the primary crushing plant include: twin tipping ramps to suit 60-tonne rigid dumptrucks; a 200-tonne surge bin mounted above a 2,500 tonnes/h Don Valley vibratory discharge feeder; a 55-tonne capacity service crane with slewing jib; a boom-mounted Rammer G80 Pro hydraulic hammer; and a two-man lift for easy access to all levels of the plant. Switchgear and lubrication systems for the primary station are housed in skid-mounted containerized units located at ground level adjacent to the plant.
With a service weight of over 1,000 tonnes, the 37m high, free-standing structure has been designed so that it can be relocated to a new position in the quarry every 5–10 years, allowing the reserves to be developed in the most efficient manner possible. With the tipping ramps, discharge feeder and other ancillary gear removed, the entire tower will be jacked up and transported using multi-wheel trailer units, resulting in downtime of just 7–10 days for each move.
Commissioning of the new plant began earlier this year, with the first rock passing through the crusher on 17 May. After just two days the machine had been tested up to an output of 2,000 tonnes/h without any problems. Following further trials and final adjustments, the resumption of production from Old Cliffe Hill commenced in earnest in July 2005.
Conveyor link
The new field conveyor linking the primary crushing station at Old Cliffe Hill to a new intermediate surge pile and reclaim facility at New Cliffe Hill was designed and built by Coalville-based Whitwick Engineering, with Italian SIG belts supplied and installed by MES International Ltd of Leicester. The fully encapsulated system extends some 1.5km in length and comprises five separate 1.6m wide conveyors of varying lengths, each with an integral belt-reeling system for ease of maintenance.
The primary conveyor carries material from the base of the crushing station at 120m AOD to the tunnel portal area at 150m AOD via a newly created access ramp. The next section of conveyor passes through the tunnel suspended on chains anchored to the roof, allowing clear ground access for maintenance purposes and minimizing the likelihood of contact by passing vehicles. A further three overland conveyors complete the link to the intermediate surge pile. In designing the conveyor link, the use of one-tenth scale models of the various conveyor transfer points helped ensure accurate and efficient material flow/transfer in the full-scale system.
The five conveyors are powered by specially manufactured drive packages comprising Sumitomo Paramax gearboxes and WEG W21-series motors. These were supplied to Whitwick Engineering as packaged systems mounted on base plates. Six units were supplied in total: four single drive units, each comprising a gearbox and premium-efficiency motor of 132kW, 160kW, respectively, plus two of 200kW rating, together with a further pair of 200kW motors and gearboxes which drive the inclined primary conveyor. All five conveyors feature ABB inverter drives for soft starting and variable speed control, with the twin drives on the primary conveyor featuring master-follower software to ensure that one drive dominates the control pattern while the second one follows.
The final conveyor in the system discharges primary crushed material from Old Cliff Hill on to a new intermediate surge pile situated adjacent to New Cliffe Hill’s existing primary crushing station and on top of its primary discharge conveyor. The creation of this facility necessitated the construction of a concrete tunnel/reclaim system above the ‘active’ primary discharge belt, a particularly awkward and technically challenging project that was tackled with great success by civil engineering firm Wildgoose (Bonsall) Ltd. Primary crushed material from Old Cliffe Hill is now fed from this surge pile on to the New Cliffe Hill primary discharge conveyor, via two Don Valley 1,500 tonne/h vibratory feeders, for the remaining 1.1km journey to the scalping plant and main processing area.
Plant control
The challenge for the electrical team was to design, supply and install an electrical system that would safely and efficiently control the plant over the long distances involved between the quarries.
Three custom-built motor-control centres, each over 16m in length, have been installed within new 11,000/415V substations at strategic points along the system. To allow the soft starting of the primary crusher motor, a 3,300V SF6 starter and a Vapourmatic resistance starter were custom-built for the application.
Control of the plant is achieved via the installation of Allen-Bradley PLCs in each of the new substations. To supply local plant control and diagnostics to maintenance staff, PanelView operator interfaces have been fitted in each motor-control centre. These give a graphical mimic of the plant and a detailed status of each drive on the system.
To provide communications, a fibre-optic cable has been installed, starting at the new primary crusher and terminating at the quarry offices some 4km distant. This cable links all of the new substations installed within the scope of this project, and all existing substations at New Cliffe Hill, to allow for planned future modernizations. The fibre provides a 100MB/sec Ethernet link between PLC, HMI and SCADA, and access from remote locations via broadband modem.
CCTV imagery is also transmitted along the fibre-optic cable, giving very high picture quality over considerable distances. Quarry personnel are able to communicate with each other via an audio communication system which runs along the full length of the conveyors and back to all control rooms and substations.
To provide overall control of the process, the existing SCADA system in the main control room at New Cliffe Hill was extended to include the new crushing plant and tunnel systems. This system now integrates material from Old Cliffe Hill into the existing processing plant. A further extension to the SCADA system gives both production and maintenance managers real-time plant information at their desks.
The entire electrical system was entrusted to Specialist Electrical Services Ltd, in a joint venture with Acorn Process Controls Ltd, who supplied the control system.
Earthmoving operations
The demanding logistical task of removing six million cubic metres of overburden from Old Cliffe Hill has been contracted out to Alfred McAlpine Asset Management on a cost-per-cubic-metre basis. Earlier this year the company were awarded a six-and-a-half-year contract to excavate the clay/marl material and transport it, via the tunnel, to the eastern end of New Cliffe Hill, where it is being used to backfill the void.
In addition to existing mobile plant used at the site, Alfred McAlpine purchased eight 50-tonne Bell B50 articulated dumptrucks (the largest trucks available that can safely fit through the tunnel), together with a Komatsu PC750 excavator and D155 dozer, specifically for this task. A total of 18 Alfred McAlpine operatives and one supervisor are employed on the overburden contract alone.
In addition to overburden removal duties, Alfred McAlpine Asset Management are also engaged in a separate seven-year load and haul contract at the site, utilizing a fleet of seven 60-tonne rigid dumptrucks. Operating on a cost-per-tonne basis, this phased contract currently involves loading and hauling blasted material at both sites, but by the end of 2005 operations will have switched entirely to Old Cliffe Hill as the retreat from New Cliffe Hill draws to a close. A further 13 staff are employed on this operation, with additional Alfred McAlpine maintenance staff permanently based on site.
Conclusion
After lying dormant since the late 1980s, Old Cliffe Hill quarry has now been brought back on stream to replace the almost exhausted reserves at New Cliffe Hill. In the coming months output from Old Cliffe Hill will be progressively ramped up as output from New Cliffe Hill winds down. In this way, Old Cliffe Hill will essentially become New Cliffe Hill, and vice versa, with employment at the site secured for the next 15–20 years.
Acknowledgement
The editor wishes to thank Midland Quarry Products Ltd for permission to visit the site and, in particular, Ian Conway, company engineering manager, for his help in preparing this report.