New Coating Plant For Glasgow
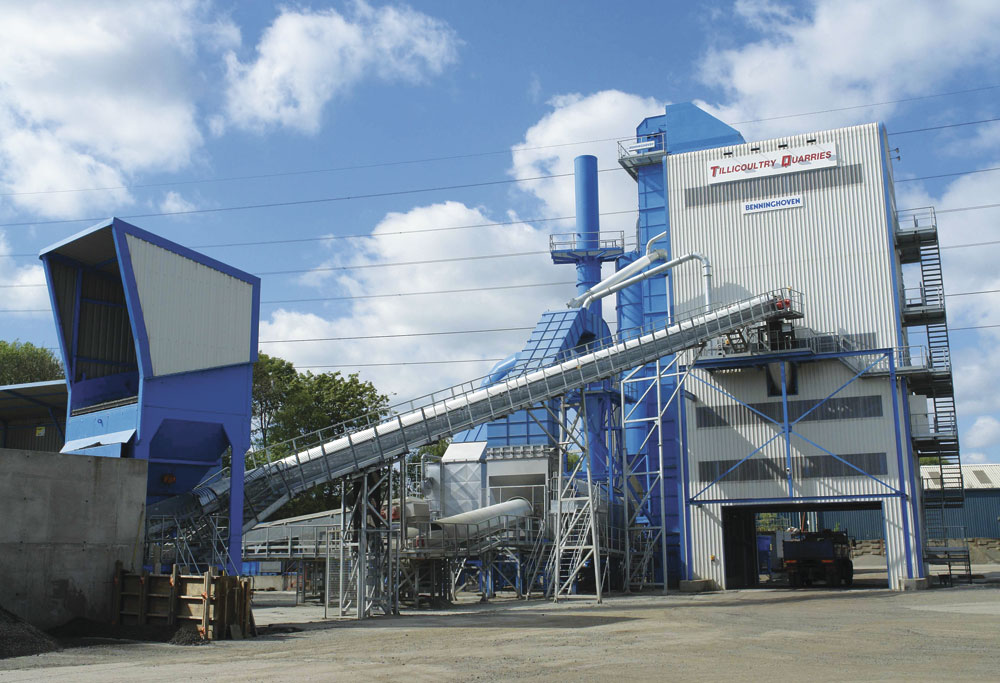
Tillicoultry Quarries choose Benninghoven for Clydebridge site
Established in 1931, Tillicoultry Quarries are a family-owned quarrying company who operate five hard rock quarries, four ready-mixed concrete plants and five coating plants around the central belt of Scotland.
The company’s main business is the provision of a full range of construction materials, including aggregates, ready-mixed concrete and bituminous products, to local authorities and the construction and road-building industries.
Tillicoultry’s latest coating plant installation, in Clydebridge, is sited alongside Junction 2 of the newly constructed M74 extension, providing easy access to Scotland’s transport network in both easterly and westerly directions.
Designed to complement the company’s existing coating facilities at Tulliallan, Kincardine; Northfield Quarry, Denny; and Tams Loup Quarry, Harthill, the new state-of-the-art Benninghoven asphalt plant forms part of a £3 million major investment in the new Clydebridge asphalt production facility, in order to increase operating efficiency and realign output with changing market requirements.
Commenting on the new plant and its selection, Tillicoultry owner/operations director Wallace Menzies said: ‘The new plant, sited close to Glasgow, will allow us to extend our geographic cover for bituminous materials into the city of Glasgow and the western side of Scotland’s central belt.’
Designed to provide significant operational benefits and cost savings, the new Benninghoven model BA4000 plant is able to produce a wide range of high-specification coated materials, including modern thin surfacings, stone-mastic asphalts and other specialized mixes. The plant has a production capacity rated at 320 tonnes/h at 4% initial moisture (DBM).
The tower design minimizes energy consumption through all stages of the asphalt production process, combining innovative design with optimum insulation and power management, thereby minimizing running costs without affecting performance and product quality.
The aggregate cold feed consists of a set of seven in-line bins with belt feeders that discharge on to a 37m collecting conveyor. This, in turn, feeds at right angles on to a 13m feed conveyor. Both conveyors are fully covered and mounted on trestles with safety pull wires along their walkways. A further feed conveyor delivers material directly into the dryer.
The aggregate dryer drum, which is 2.8m in diameter x 10m in length, is fully lagged with 70mm thick insulation and aluminium clad for heat retention and noise reduction. The drum is friction driven by four support rollers through individual 22kW inverter-controlled geared motor units.
The burner, a Benninghoven model Evo Jet oil EG4FU type designed to minimize CO2 emissions, is adapted to run on gas oil and natural gas. The compact unit is equipped with a full range of operating and safety devices to deliver high-efficiency fuel usage. In addition, an air inlet silencer is connected to the burner to suppress noise levels, and the burner and silencer are mounted on a track to allow the unit to slide back from the dryer for routine servicing.
The plant’s dust-collection system, which is rated at 84,000Nm3/h, is sized for the dryer and mixing section scavenging, and achieves emission levels of less than 25mg/m3. A primary skimmer unit mounted alongside the dryer separates any coarse dust from the airstream; this passes to the hot-stone elevator feed boot via a gravity flap valve and chute. The secondary cassette-type filter system collects any remaining dust and transfers it, via two screw conveyors, to the filler elevator. A dust monitor mounted on the exhaust stack provides a remote readout in the operator’s cabin. As a result, the plant meets the most stringent dust control regulations.
Any excess dust collected can be discharged from the reclaimed dust silo through a rotary valve into a twin-shaft paddle conditioner where water is introduced, thereby providing an environmentally friendly method of purging the reclaimed dust. Any excess filler can also be directly loaded into road tankers.
Hot aggregates are transported from the dryer up to the screen by a 23m vertical bucket-type elevator. This is totally enclosed and features a heavy-duty double-strand chain and wear-resistant steel buckets with replaceable liner plates at impact points. Elevator drive is by a 45kW geared motor and toothed chain wheels at the elevator head. The elevator features outside-located bearings and a safety backstop facility, while a wide platform provides access for maintenance.
Material discharged from the elevator passes into a six-deck screen which features twin-shaft drive via two 19kW ‘bolt-on’ low-maintenance vibrating motors. These drive units are mounted outside the screen housing to allow high-temperature screening of materials. Wide access doors, together with a roll-away chute, provide access to all screen decks. An extraction fan ensures negative pressure is maintained in the screen housing for optimum dust control.
The hot-storage section has a total capacity of 215 tonnes and comprises seven bins. All the bins are insulated and clad and each is fitted with continuous level indicators and an overflow chute. Discharge is by a pneumatically operated radial door which accurately regulates material flow to the aggregate weigh hopper, from where the aggregates are discharged directly into the mixer.
Accurate weighing out of ingredients is achieved by separate load-cell-mounted weigh hoppers consisting of a 4,000kg capacity aggregate hopper, a 600kg filler weigh hopper and a 450-litre capacity weigh vessel for bitumen. Mixing takes place in an insulated, 4,000kg capacity, twin-shaft paddle mixer, with drive provided by two 55kW geared motor units through synchronized gears. A radiation pyrometer is situated at the mixer discharge to indicate mix temperature.
Filler is stored in two external vertical silos holding approximately 80m3 of reclaimed filler and 50m3 of imported material. Both silos are equipped with level indicators and shut-off valves.
A gravimetric additive system is also incorporated within the plant to feed granulated material from a 3m³ silo. Each batch of granulate is accurately weighed in a load-cell-mounted weigh hopper before being discharged through a butterfly valve to the mixer.
A RAP system has also been incorporated in the facility to deliver precise percentages directly into the plant mixer. The system comprises a steep-sided, 10m3 capacity feed hopper fitted with an oversize grid and two vibrators. A belt feeder mounted beneath the hopper discharges the RAP on to a 35m long inclined conveyor leading to a 1,000kg weigh hopper which provides accurate proportioned batches. A flap-type inlet chute transfers the material into the mixer, while an automatic vent duct at the mixer allows rapid extraction of steam during recycling operations.
The plant is controlled by a Benninghoven on-line Batcher 3000 computer system that displays all plant functions via colour graphics. The system, which is housed in an existing control cabin adjacent to the plant, is modem linked and provides storage for up to 500 asphalt mix recipes.
Acknowledgements
Thanks are due to Wallace Menzies, director of Tillicoultry Quarries; Russell Sinnott, asphalt plant manager Scotland area; and Nigel Moreton of Benninghoven UK Ltd, for their help in preparing this report.