New Benninghoven Plant For Clatchard Quarry
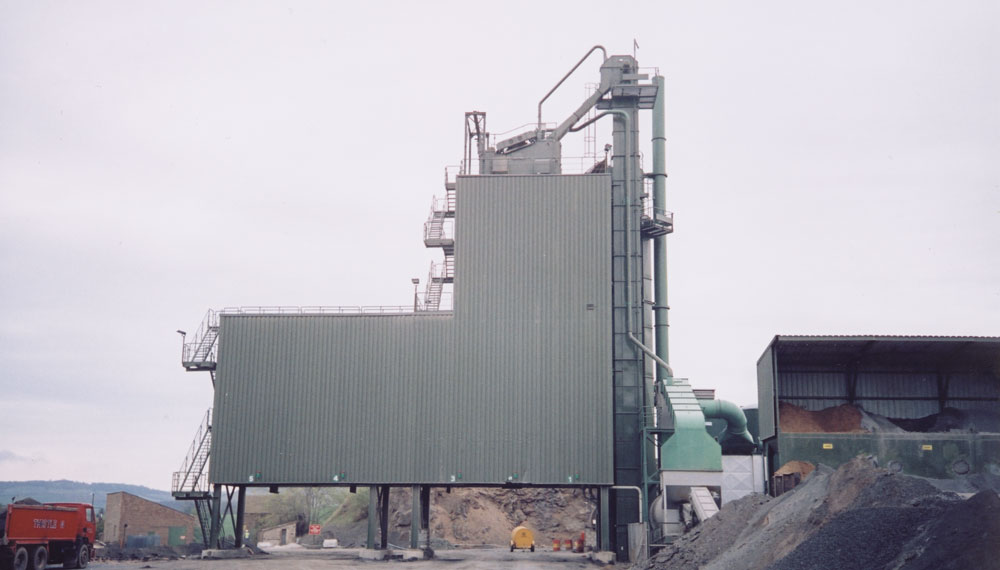
Ennstone Thistle, the Scottish arm of Ennstone plc and the leading suppliers of aggregates and asphalt north of the central belt, have recently replaced a 30-year-old hybrid asphalt plant with a brand new 130 tonnes/h Benninghoven TBA 130U plant at their Clatchard Quarry in Fife. According to Ennstone Thistle, the investment has allowed them to increase customer service levels substantially, with asphalt gangs being supplied from the plant’s 200 tonnes of hot-storage capacity in the mornings, thereby freeing the facility to turn around the lower-volume collect utility market more efficiently during the day.
Cold feed to the new plant is catered for by seven cold-feed bins, each equipped with variable-speed belt feeders to allow accurate blending, while the sand hoppers are fitted with vibrators to assist good material flow. The entire section is covered with metal sheeting on the roof and sides to keep the materials dry.
A series of collecting and inclined conveyors pass the blended feed materials to a reversible slinger conveyor for delivery into the dryer drum. The dryer, which is 2m in diameter and fully flighted with Benninghoven high-efficiency lifters, is insulated and aluminium clad for heat retention and noise reduction, and has friction drive on all four support rollers through individual 7.5kW geared motor units, thereby eliminating chain noise. The dryer discharge chute is fitted with an infrared pyrometer to control burner settings and material temperatures.
The burner itself comprises the well proven Benninghoven Rax-Jet Turbo oil burner. This is equipped with a full suite of safety devices and fitted with a sound attenuator to further reduce noise levels.
A hot-stone elevator transports the heated material to the screening level of the mixing tower. The elevator is totally enclosed and features twin-strand chain and wear- resistant steel buckets with wear-plate edges and replaceable liner plates at high-impact points. Elevator drive is via a head-mounted 11kW geared motor equipped with a backstop facility.
Material from the elevator passes to a six-deck, twin-driveshaft screen featuring two 7.5kW drive motors mounted outside the dust-protection cladding to allow high- temperature materials to be screened. The screen amplitude is adjustable and a diverter chute under the screen directs fines into one of two hot-fines hoppers. Hot aggregates which have been sized by the screen pass to seven hot-stone bins which provide a total capacity of 74 tonnes. All the bins are insulated and clad and each has its own pneumatically operated radial discharge door to accurately regulate the flow of sized aggregates to the weigh hopper. In addition, each bin is fitted with a continuous level indicator and an overflow chute.
Separate load-cell-mounted weight hoppers for aggregates, filler and bitumen are provided at the mixing level of the plant. Aggregates are discharged directly to the mixer from the aggregate weigh hopper, while bitumen is injected into the mixer from a weigh kettle by means of an injection pump, to assist with coating of the aggregates. The filler is fed via a screw conveyor from the filler weigh hopper.
The mixer itself comprises an insulated, 1,600kg capacity twin-shaft unit driven by a 37kW geared motor through synchronized equal gears at each end to give a rapid, homogenous mixing cycle.
A 1,600kg capacity horizontal skip with a 3kW drive conveys the mixed material to the mixed-material storage silos located directly below the mixing section. Mounted on load-cells for accurate discharge to delivery trucks, the silos comprise four 50-tonne vessels and one 20-tonne direct-load/foul-batch hopper. The 50-tonne silos are all lagged with 150mm thick mineral wool and equipped with electrically heated doors with thermostatic control.
The entire mixing section, including the mixed-material storage silos, is sheeted with coloured profile sheeting for aesthetic appearances.
The dust-collection system at the plant includes a pre-skimmer unit prior to the bag house to collect the coarse dust. This is equipped with a gravity flap valve and a chute to the hot-stone elevator feed boot. Fine dust is collected by the 32,000Nm3/h bag house and fed to the reclaimed-filler silo by screw conveyor and vertical elevator. The 60m3 capacity reclaimed-filler silo forms the lower section of a filler tower system, the upper silo holding up to 40m3 of imported filler. Both the reclaimed and imported fillers are fed to the filler weigh hopper via screw conveyors. Any excess fine dust is fed to a dust conditioner to allow disposal.
Bitumen is stored in two of the latest 50m3 capacity Benninghoven high-efficiency, electrically heated vertical bitumen tanks. Fitted with pumps, valves, electric trace heating and lagged pipework, these tanks incorporate maximum levels of insulation to minimize heat loss and deliver significant energy savings.
Also included in the plant specification is a gravimetric granulate feed system with two 3m3 silos for different granulate products. Each batch of granulate is accurately weighed before being pneumatically conveyed to the mixer via a cyclone unit. A belt conveyor equipped with a counter system allows pigment bags to be added to the mixer automatically.
The entire plant is controlled by a single person located in the quarry’s weighbridge complex using a Benninghoven Online Batcher 2002 computer system with touch-screen monitor. The control system provides storage capacity for up to 1,000 recipes.