Modern Brickmaking At Measham
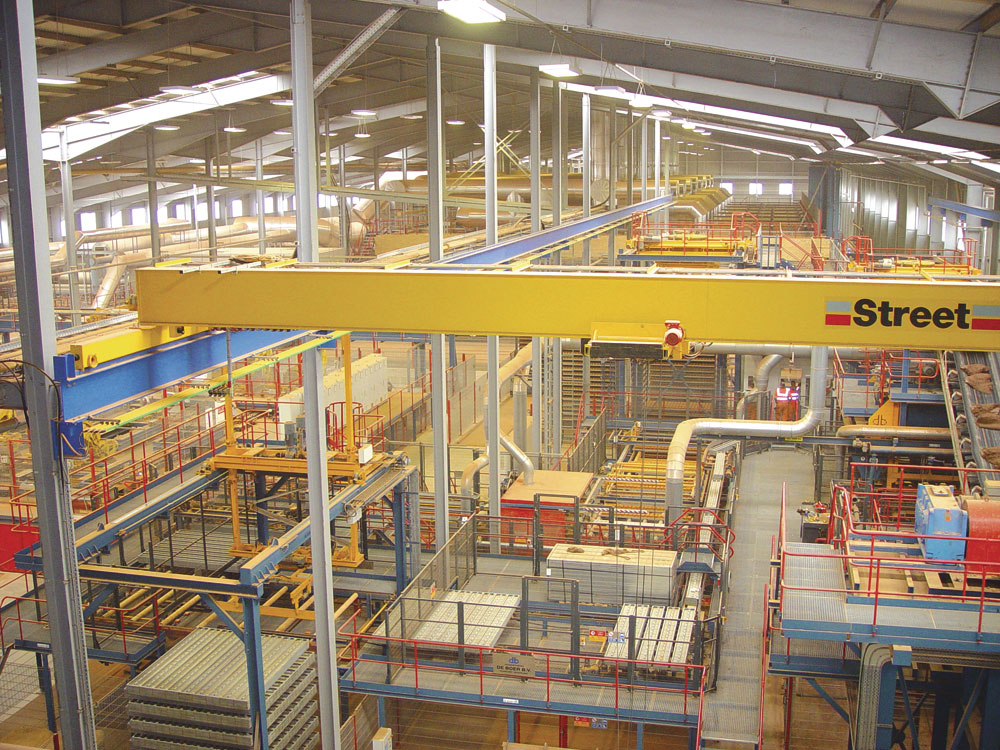
Hanson Building Products invest £50 million in new brick factory with quality and sustainability at its core
Last September saw the official opening of Hanson Building Products’ £50 million state-of-the-art ‘soft-mud’ brick factory in Measham, Leicestershire. The factory is the largest and most modern production facility of its kind in Europe and has been designed and built with sustainability and quality at its core. Located on a brownfield site close to the M42 motorway, it has been developed to combine locally sourced raw materials with highly efficient, low-energy and low-waste production processes, to make the most sustainable bricks of their kind with the lowest embodied CO2 currently available in the market. In addition to its impressive sustainability credentials, the fully mechanized facility offers bricks of consistent colour, dimension tolerance and quality, and currently produces more than 20 different varieties of facing bricks in plain reds and buffs as well as multi-coloured options.
Operated by a total of just 28 staff, the factory has the capacity to produce 100 million bricks a year (more than 30,000 bricks an hour) and forms part of a project by Hanson Building Products – part of Germany’s HeidelbergCement Group – to replace their older, smaller and less-efficient plants with large-scale, highly automated facilities for the manufacture of high-quality facing bricks. Indeed, Measham now has the capacity to produce the same volume of bricks as five of the company’s previous factories but with around one tenth of the staff, and as a result, the multi-million pound investment is expected to give Hanson a significant competitive edge when the market recovers.
The new factory has been built, in part, on the site of an earlier, smaller brickworks and adjacent to a terracotta works, both of which were originally owned and operated by Red Bank. In 2002, however, the former brickworks was bought by Hanson, who then went on to acquire the rest of the Red Bank business in January 2006 as part of a strategic move to secure the company’s extensive high-quality clay reserves, which are ideally located in the heart of central England, close to good transport links. Today the Hanson Red Bank terracotta works continues to produce hand-crafted chimney pots, flue liners, ridge tiles, finials and other ornate niche clay products, operating in complete contrast to the brand new, ultra-modern, high-output brick factory that now stands next door.
Factory construction
Groundwork in preparation for the construction of the new factory commenced in September 2007. Because of the presence of residual oil contamination in the made-up ground on which the factory was to be built, pressure cleaning of the soil across the entire area was one of the first tasks to be carried out, followed by the installation of around 1,200 driven concrete piles to provide a stable foundation for the new factory.
Bedford-based SDC Construction Group were appointed as the lead contractor for the initial phases of construction work, with specialist brickmaking plant and equipment suppliers, including German-based firms Händle and Lingl, as well as Dutch company De Boer, responsible for the design and installation of the manufacturing machinery. The vast factory building, which measures approximately 300m in length x 100m in width, was constructed in line with BREEAM sustainability criteria, utilizing as much natural light and ventilation as possible, in conjunction with low-energy artificial lighting, together with provision for the capture rainwater from the factory roof for use in the production process. In addition, all motors and inverters (2kW and above) used within the factory are highly energy-efficient EFF1-rated units, and a flocculant system is used to ensure effective recycling of waste sand and water from the brick production process.
Brick production – quarry operations
Measham has more than 6 million tonnes of owned and permitted clay reserves – sufficient to last for 25 years at the current production level of 100 million bricks a year. The clay pit itself is situated adjacent to the new factory but is separated from it by a public road. The indigenous raw material – a red-burning clay belonging to the Keuper Marl formation – is extracted by contractors on a twice yearly campaign basis to form a 30,000m3 main stockpile, which is built up in layers to provide an element of preliminary mixing. The Keuper Marl represents approximately 80% of the feedstock to the new factory, with the remaining 20% comprising locally imported fireclay, which is also stockpiled on site for use in the production of a range of buff-coloured bricks. Quantities of imported body sand and fuel additive (anthracite) are also held on site.
Initial processing and blending of the clays and additives takes place within the quarry site. Three 60-tonne capacity load-cell-mounted box feeders, which are fed by wheel loader and housed within their own covered building, feed correct proportions of the main clay feedstocks on to a conveyor belt for delivery to an adjacent primary crusher building at a rate of 130 tonnes/h. The primary crusher comprises a heavy-duty Händle twin-shaft roller mill driven by two Hägglunds hydraulic motors and capable of reducing 0.5m clods of hard shale and clay down to 100mm. The unit is equipped with a breakout device for the release of tramp metal.
After primary crushing, between 10–20% body sand is added to the clay to control shrinkage of the bricks during drying and firing. If a multi-coloured red brick is to be produced, a small percentage (1–2%) of anthracite is also added to the carbon-poor indigenous clay at this point; this is not necessary with the imported fireclay, which has a higher naturally occurring carbon content. These additives are introduced proportionally via two additional load-cell-mounted box feeders and belt conveyors housed within the primary crusher building.
From here, the material stream is fed to the new factory building via a series five belt conveyors. This 140m long conveyor line passes over Atherstone Road via a new bridge, which, at the request of local residents, has been clad with Wonderwall brick slips to give it a visual appearance similar to the canal bridges often seen in this part of the Midlands.
Brick production – factory operations
On arrival in the new factory, the main phases of clay preparation begin with delivery of the material to a Händle wet-pan mill, where 2–3% water is added. This centre-feed milling unit is equipped with four 16-tonne rollers that revolve around the pan, forcing the clay through a slotted base at a rate of 130 tonnes/h. This reduces the clay down to 10–20mm while mixing and homogenizing the material at the same time. The clay is then discharged on to two 2.4m wide collecting conveyors, each of which can operate independently if necessary, for delivery to two sets of rollers; first, a medium-speed pair with a gap setting of 2.5 mm, followed by a high-speed pair with a finer setting of 0.8mm. Operating in parallel, these units finely grind the clay to ensure that any impurities, such as lime nodules, do not cause problems when the bricks are fired. All four roller units are equipped with integral turning lathes to allow regular trimming of the rollers, as the accuracy of the gap setting is critical to the quality of the finished bricks. The two clay streams are then sent to a pair of double-shaft, paddle-bladed screening mixers where further mixing takes place together with the addition of water to achieve a moisture content of around 13–15%. A barium carbonate slurry is also added at this point to prevent soluble salts from causing discolouration on the surface of the finished bricks.
From here the prepared clay is delivered to the ‘souring’ house, where it is discharged by overhead shuttle conveyor into one of four 1,125m3 capacity bunkers, each capable of holding around 2,500 tonnes of clay. The souring house provides a material buffer stock for the downstream brickmaking plant, allowing various compositions to be stored and called upon when needed. Importantly, it also provides for further conditioning and homogenization of the clay, helping to improve its workability.
The clay is recovered from the souring house by means of a fully automated, 12m long bucket reclaimer, which scrapes across the face of the stockpiles, planing off and mixing the clay and delivering it on to a lower belt which feeds two screen feeders. These are designed to further moisten and homogenize the clay after its period of storage in the bunkers, and to ensure the soft-mud mixers on the downstream brickmaking plant receive an even and consistent feed. If necessary, the souring house shuttle conveyor can be moved to a bypass position to feed the two screen feeders directly.
At this point in the process, the fully automated Händle clay preparation and processing facilities feed into the interlinked De Boer brickmaking plant. Drawing the prepared clay at a rate of 100 tonnes/h and capable of making 34,000 bricks per hour, the brickmaking machinery combines two technologies which provide the ability to produce pressed bricks, thrown bricks or water-struck bricks through relatively minor adjustments to the plant. Previously, such flexibility would have required the use of three separate machines.
Clay from the Händle screen feeders is delivered, via conveyor, to a pair of De Boer soft-mud mixers. These two final mixing units automatically add the correct amount of water to achieve the final consistency needed for the brickmaking process (18–22% moisture content). The brick-forming machine works by either pressing or throwing the soft clay into a series of pre-sanded moulds, each mould being 22 bricks across, which form a chain-driven mould train that passes beneath the machine. Metal trays are automatically placed on top of the filled moulds, allowing the bricks to be de-moulded for delivery into the dryer car via a walking beam, elevator and multi-forked lifting crane. While the bricks are being transported to the dryer by a transfer system, the moulds undergo a washing and re-sanding process before being returned to the press for the next filling. At this stage, any waste clay from the brick-forming machine is recycled back to the soft-mud mixers.
The drying section at Measham comprises eight Lingl chamber dryers where the ‘oversize’ bricks are dried/cured for 30h to reduce their moisture content from around 20% down to less than 2% before they are set for firing. The drying chambers, each of which is capable of holding 73,920 bricks, utilize waste heat from the cooling section of the factory’s gas-fired kiln for optimum energy efficiency and fuel usage. A transfer system retrieves the dry cars of bricks from the chamber dryers and delivers them, via another multi-forked crane, to the dry descender, whereupon another walking beam collects the bricks and transports them to a series of brick turners. These turn over the bricks and their metal trays, allowing the trays to be removed and returned to the brick-making machine while the dry bricks progress to a robotic setting station.
At the setting station the bricks are automatically rotated, spaced, turned on edge and formed into groups of 11 ready for setting. Four setting robots then place the groups of bricks on kiln car pallets in stacks or ‘hacks’ comprising 528 bricks, ready for a forked crane to lift them on to waiting refractory kiln cars. The fully laden kiln cars, each of which carries 32 hacks comprising a total of 16,896 bricks, are automatically sent, via a rail system, to warm storage at the entrance to the tunnel kiln. The kiln itself measures more than 200m in length and, together with its preheat section, contains a total of 32 kiln cars at any given time. The cars are pushed through the kiln by means of hydraulic rams on a one-in, one-out basis. The firing cycle lasts for 36h with a firing temperature that can vary between 1,025°C and 1,080°C, depending on the brick type being produced. The kiln temperature and conditions (ie whether using oxidation or reduction firing), the composition of the clay mixture used and the way the bricks are set in the kiln, all contribute to the finished pattern and colour of the bricks. At the end of the kiln, a flue-gas scrubber containing 300 tonnes of limestone filters out hydrogen fluoride from the exhaust gas, which is emitted via a 45m tall chimney.
On exiting the kiln, the haulage system transports the kiln cars to the de-hacking station where the hacks of fired bricks are removed from the cars by a forked crane and placed on a belt which presents them to the de-hacking robots. These remove alternate layers of bricks from different hacks to ensure a good blend and maximum colour mixing within the individual finished packs. The layers of bricks are placed on a chain conveyor for transport to the packing area where paper is placed on top of each layer to minimize scuffing during transport. The brick layers are then doubled up and built into packs comprising a total of 495 bricks by a series of packing robots. Voids are left within the packs to allow for fork-lift truck handling. The finished packs are then strapped automatically before moving on to stretch hood machines which apply a protective film covering. A roller conveyor transports the finished packs out of the factory building, where they picked up and taken to stock by a unique 16-tonne Linde fork-lift truck that is capable of handling six packs at a time.
Conclusion
Despite the economic downturn and resulting reduction in demand for bricks, there remains a pent-up demand for housing in the UK and Hanson Building Products say this major investment in, and commitment to, the future of the brick industry will ensure the company is well positioned when recovery kicks in. Indeed, the Measham factory, which currently works on a day-shift basis only, has the potential to work round the clock as demand increases. Moreover, the factory itself has been designed to allow for the possible future addition of another drying section and kiln, which, at a cost of around one third of the original investment, would double Measham’s output to 200 million bricks a year. But whatever the economy holds in store, the long-term clay reserves at Measham, combined with a highly efficient manufacturing facility which has quality and sustainability at its core, puts Hanson Building Products in a very strong position, both now and into the future.
Acknowledgement
The editor wishes to thank Hanson Building Products for permission to visit the Measham site and, in particular, Tim Barnett, general manager, Paul Brader, production director, and Duncan Edwards, head of projects, for their help in the preparation of this report.