Major Investment Completed At Cloud Hill
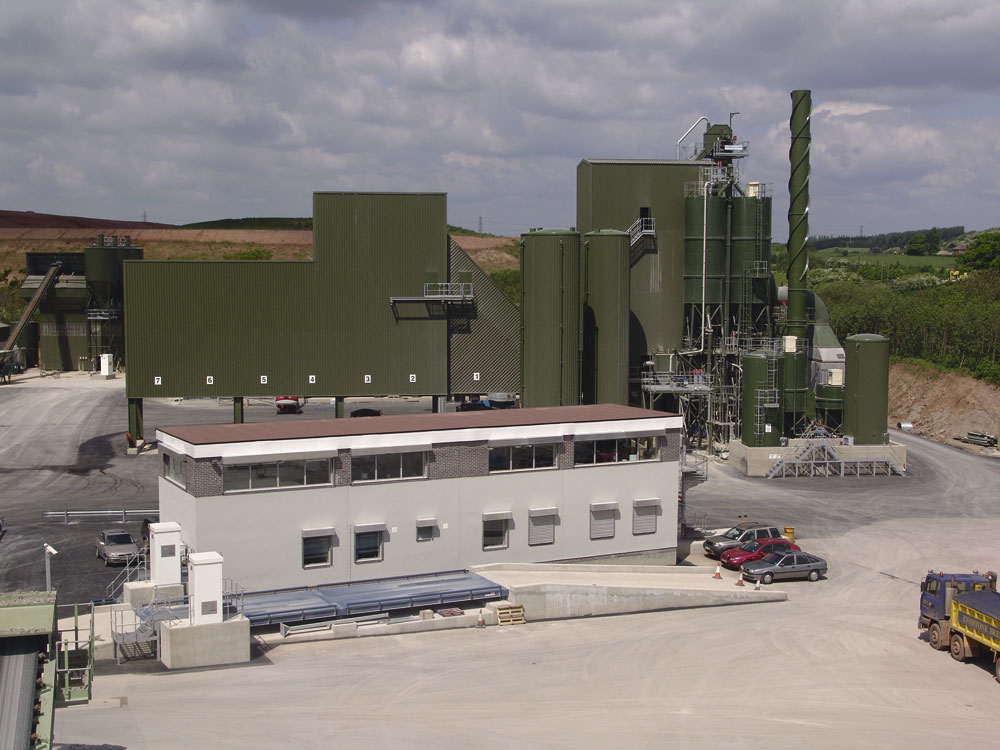
New coating and concrete plants deliver added value for Ennstone Johnston
Cost saving and adding value are fundamental problems facing many quarrying companies today as they strive to achieve higher values and new outlets for their materials. The recently completed £8 million redevelopment of Ennstone Johnston’s Cloud Hill Quarry, near Nottingham East Midlands Airport, in Leicestershire, has addressed these problems from several different angles, transforming the site’s existing low-value, low-quality production base into one of greater value and higher quality. And with the recent commissioning of new asphalt and concrete plants, the 1.4 million tonnes per annum site is now delivering significantly higher yields and better returns.
‘With today’s markets increasingly looking for a one-stop-shop, we needed the facilities to produce more value-added products at Cloud Hill,’ said Ed Reed, managing director of Ennstone Johnston Ltd. ‘Strategically, this site is in a very good location, situated in close proximity to the major centres of Birmingham, Leicester, Nottingham and Derby. It fills the gap in the Midlands region and has excellent transport links via the M1 and M42. We are well placed for major projects such as the M1 widening, the dualling of the A453 and future developments at East Midlands Airport.’
The investment programme at Cloud Hill began three years ago with a rationalization of the production process, whereby the dumptrucks that were previously used to haul blasted rock to an ageing static processing plant were replaced by an in-pit mobile primary crusher and seven mobile link conveyors. Now these flexible link conveyors transport the primary crushed stone to a permanent field conveyor that feeds the reconfigured main processing plant, thereby eliminating the need for dumptrucks and delivering considerable cost savings (see QM March 2004).
This development was followed by the installation of a novel jet washing system, which deals with the problem of waste fines by converting them into a valuable manufactured concrete sand (see QM June 2006), together with the concurrent installation and commissioning of the new asphalt and wet-batch concrete plants.
Coating plant
To achieve Ennstone Johnston’s required asphalt mix specifications, production targets and environmental criteria, a Benninghoven model TBA320 asphalt plant equipped with a 4,000kg mixer was selected. Capable of delivering a wide range of standard and specialized mixes, the plant has a production output of 320 tonnes/h of dense basecourse, at 4% initial moisture, and 240 tonnes/h of HRA (hot-rolled asphalt) at 6% initial moisture.
Erection of the coating plant began in mid-November 2005 with Benninghoven UK Ltd as principal contractor. All the equipment was supplied, installed and commissioned in compliance with current CDM and UK health and safety regulations. Commissioning took place just five months later and asphalt sales began in earnest in early April 2006.
Design parameters for the new plant called for an installation that would provide a high flexibility of mix specifications together with on-demand volume production. Due to the plant’s location, particular emphasis for planning was placed on its low-profile design, together with minimal noise and dust emissions. As a result the plant meets the most stringent of environmental controls.
The mixing tower comprises individual pre-built modules, installed in set positions. This configuration allows for standardization of components and provides a high level of reliability with minimum maintenance.
The aggregate feed system consists of an in-line unit of ten 20m3 capacity cold-feed hoppers, each fitted with a frequency-controlled belt feeder for accurate blending. Four of the hoppers are for sand; these are equipped with hopper-wall vibrators to ease material flow. All the hoppers are sheeted on their sides, ends and roofs, to prevent dust when loading and to protect feed stocks from the weather.
A 47m long collecting conveyor delivers material on to a 26m long x 800mm wide inclined feed conveyor, which discharges directly into the aggregate dryer drum. Measuring 2.8m in diameter x 10m in length, the drum is fully lagged with 70mm thick Rockwool insulation and aluminium clad for heat retention and noise reduction. The dryer drum is friction-driven by four support rollers, through individual 22kW geared motor units, and enclosed within a 2m high safety fence fitted with an electrical interlocked access gate.
The burner is a Benninghoven model RJO4, which burns gas oil. This is equipped with a full range of operating and safety devices to deliver high-efficiency fuel usage. An air inlet silencer is connected to the burner to suppress noise levels. Both the burner and silencer are mounted on a track to allow the unit to slide back from the dryer for routine servicing.
To meet stringent dust-control regulations, the plant’s dust-collection system, sized for the dryer unit and mixing section scavenging, is rated at 84,000Nm3/h and achieves emission levels of less than 25mg/m3. A primary skimmer unit mounted alongside the dryer separates any coarse dust from the airstream, which passes to the hot-stone elevator feed boot via a gravity flap valve and chute. A secondary cassette-type bag-filter system collects any remaining dust and transfers it, via two screw conveyors, to the filler elevator. Dust is also collected from nuisance points at the screen, weigh hoppers and elevator. A dust monitor mounted on the exhaust stack provides a remote read-out in the operator’s cabin.
Any excess dust collected can be discharged from the reclaimed dust silo through a rotary valve into a twin-shaft paddle conditioner, where water is introduced through spray nozzles to provide an environmentally friendly method of purging the material.
Hot aggregates are transported from the dryer up to the screen by a vertical bucket-type elevator. This is totally enclosed and features a heavy-duty double-strand chain and wear-resistant steel buckets with replaceable liner plates at impact points. Elevator drive is provided by a 45kW geared motor and toothed chain wheels at the elevator head. The elevator features externally located bearings and a safety backstop facility, together with a platform and wide inspection doors for ease of maintenance.
Material discharged from the elevator passes into a six-deck screen, powered by four 13kW low-maintenance external drives, to allow for high-temperature and superheated mixes when the plant is using recycled materials. An extraction fan ensures negative pressure is maintained within the screen housing for optimum dust control. The screen is fitted with a by-pass facility.
The hot-storage section comprises six bins with a total capacity of 150 tonnes. All the bins are insulated and clad and each is fitted with a continuous level indicator and overflow chute. Bin discharge is by pneumatically operated radial doors, which accurately regulate material flow to the aggregate weigh hopper, from where the aggregates are discharged directly into the mixer.
Accurate weighing of ingredients is achieved by separate load-cell-mounted weigh hoppers, comprising a 4,000kg capacity aggregate weigh hopper, a 600kg filler weigh hopper and a 400-litre capacity weigh vessel for bitumen. A 1,400 litres/min injection pump forces the bitumen into the mixer. Mixing takes place in an insulated, 4,000kg capacity, twin-shaft paddle mixer, driven by two 55kW geared motor units through synchronized gears. The mixer’s paddle arrangement ensures rapid and thorough mixing, while a radiation pyrometer situated at the mixer discharge indicates the mix temperature.
Mixed material discharged from the mixer falls into an inclined skip unit, which distributes the material into six insulated storage silos offering a total capacity of 450 tonnes. All are equipped with ‘high level’ warning indicators and fitted with electric trace heating around the discharge doors. A direct load-out hopper is positioned beneath the mixer. Each of the 75-tonne storage silos is mounted on load-cells to give an accurate reading of material load out.
Bitumen is stored adjacent to the plant in three vertical, 100m3 capacity tanks. These are Benninghoven’s latest high-thermal-efficiency units, which deliver low running costs due to their stepped heating system design. An in-built loading system with ‘high level’ probes offers fail-safe filling with no possibility of spillage.
The site is self-sufficient in reclaimed limestone filler from the plant’s dust-recovery system. This is stored in two 70m3 vertical silos, fed by a 20 tonnes/h belt-type elevator. A screw conveyor transfers the filler from the silos direct to the weigh hopper. Both silos are equipped with level indicators and shut-off valves. Any excess filler is distributed to other coating plants within the Ennstone Johnston group across the East and West Midlands.
A gravimetric additive system is also incorporated in the plant to feed granulated material from a 30m3 capacity silo. Each batch of granulate is accurately weighed in a load-cell-mounted weigh hopper before being discharged through a butterfly valve into the mixer. A pigment silo of similar specifications is sited alongside.
A cold RAP (recycled asphalt planings) system has also been incorporated in the facility to deliver precise percentages into the plant mixer. The system comprises a steep-sided, 10m3 capacity hopper fitted with a grid and vibrator. A belt feeder mounted beneath the hopper discharges on to a 38m long transfer conveyor, then on to a 3.5m long weigh conveyor. A steam-extraction duct transfers any steam to the dust-collection system.
The plant tower and mixed-material storage is fully sheeted to minimize noise and to provide a pleasing aesthetic appearance to the whole plant.
The plant is controlled using a Benninghoven on-line Batcher 3000 computer system, which displays all plant functions via colour graphics. This advanced system, which offers the latest hardware within a user-friendly package, is housed in the quarry’s new control centre. The system is modem linked and provides storage for up to 500 asphalt mix recipes.
The new, purpose-built, two-storey control centre, which overlooks the coating and concrete plants and the new weighbridge complex, accommodates the quarry manager, sales and technical staff, concrete and asphalt plant operators, and the weighbridge and dispatch clerks in air-conditioned comfort. This spacious, open-plan office provides a 360° view of the entire site and allows all key staff to communicate face to face, providing effective central control of all production, shipping, dispatch and fleet operations.
Concrete plant
The commissioning of a brand new Steelfields SM 60 wet-batch concrete plant a month or so after the coating plant has not only provided another route to market for Cloud Hill’s manufactured concrete sand, but also opened up new routes to market for value-added single sizes. Cloud Hill’s manufactured sand is also supplied to sister company Ennstone Building Products, in Telford, who previously had to buy sand on the open market for concrete pipe production. Now a straightforward ‘milk run’ delivering the manufactured sand to Telford, then travelling a few miles to Ennstone Johnston’s Leaton Quarry to backhaul high-PSV stone for Cloud Hill’s new coating plant, addresses the supply and demand issues in house.
Cloud Hill’s new modular space-frame ready-mixed concrete plant incorporates a 300-tonne capacity, four-compartment aggregate storage bin (split 100/50/50/100 tonnes) equipped with high level probes and heavy-duty dosing gates. The two sand compartments are fitted with automatic moisture probes as well as pneumatic vibrators and low-friction liners to ease material flow. Raw feed stocks are supplied from 17 covered ground storage bays via a 30-tonne capacity ground loading hopper and a 750mm wide inclined radial feed conveyor. During batching, aggregates and sand are weighed in a 7,000kg capacity load-cell-mounted weigh hopper equipped with impact liners and a pneumatic vibrator, before being delivered to the mixer via a 900mm wide inclined batch conveyor. The manufactured sand is mixed 50:50 with virgin sand from Ling Hall during concrete production.
Cement and ground granulated blast-furnace slag is stored in three 80-tonne capacity single-compartment silos, each equipped with a reverse-jet exhaust filter, aerated cone and pressure-relief valve. During batching the cement/slag is fed into a 1,500kg capacity load-cell-mounted weigh hopper equipped with an independent reverse-jet exhaust filter and single-speed screw discharge for delivery to the mixer.
Clean water is supplied from a storage tank via a 75mm system featuring a feed pump, Promag flowmeter, pneumatically operated control valves and a 25mm trickle by-pass facility. A Fosrock liquid admixture storage and dispensing system has also been incorporated within the plant.
Driven by a 75kW motor, the Steelfields SF2000 high-speed pan mixer has a maximum batching capacity of 2.0m3 (compacted) and a maximum output of 60–80m3/h. An additional steel/fibre hatch has been provided in the mixer’s electrically operated gull-wing type cover. Discharge is via a single hydraulically operated door and rubber sock arrangement, with the plant’s elevation designed to suit ‘wet’ deliveries into 8m3 truckmixers.
Batching is controlled and monitored remotely from the quarry’s new control centre using a PC-based COMMANDbatch system, supplied by Command-Alkon, which features a multi-recipe/mix storage facility, digital weight displays, hard-copy printouts and full manual override. The plant operator also has full CCTV coverage of the plant, with cameras fitted over the aggregate bins and at the truckmixer load-out point. In addition, a Safe-Weigh system is fitted to the silos to give the operator a continuous visual indication of the contents of each vessel.
Multi-purpose vehicles
Taking account of the construction and infrastructure development plans throughout the East and West Midlands, the Ennstone Group has recently taken delivery of a fleet of 37 new multi-purpose delivery vehicles capable of carrying dry stone, coated materials or ready-mixed concrete. Eight of the vehicles are based at Cloud Hill.
Built around a Foden Euro 3 light chassis, these bespoke trucks feature an innovative pneumatic system developed by Hymix and Tanker Solutions Ltd, which allows a 20-tonne Wilcox insulated tipper body to be replaced with an 8m3 Hymix mixer body (or vice versa) in approximately 10min. This provides much greater flexibility for the transport department and ensures maximum truck utilization with reduced transport costs.
Conclusion
The recent investment at Cloud Hill has transformed the site from a low-value operation into a modern, state-of-the-art facility capable of delivering added value for the company for many years to come. As well as the operational and commercial improvements, however, the site has also undergone significant environmental enhancements with the addition of extensive paved areas and effective dust-suppression measures.
In total, some 14,000 tonnes of asphalt have been laid around the plant yards and roads, dust-suppression sprays have been placed on key roadways around the site and wheel washers have been installed ahead of both outbound weighbridges. As a result, delivery vehicles leave the site in a much cleaner condition and the company no longer needs to hire a road sweeper to maintain the condition of the public highways around Cloud Hill.
Summing up the latest phase of investment at Cloud Hill, quarry manager Carl Ashurst said: ‘I’m very pleased with the new plant. The last six months have been very challenging, but the benefits of everyone’s hard work can now be seen. We have a very clean and tidy site, and one that will provide added value for the company well into the future.’
Acknowledgement
The editor wishes to thank Ennstone Johnston Ltd for permission to visit the site and, in particular, Ed Reed, managing director, Phil James, operations director, Jon Brummitt, director of corporate services, and Carl Ashurst, quarry manager, for their help in preparing this report. Thanks are also due to Nigel Moreton of Benninghoven UK Ltd.