Hurn Court Farm Comes on Stream
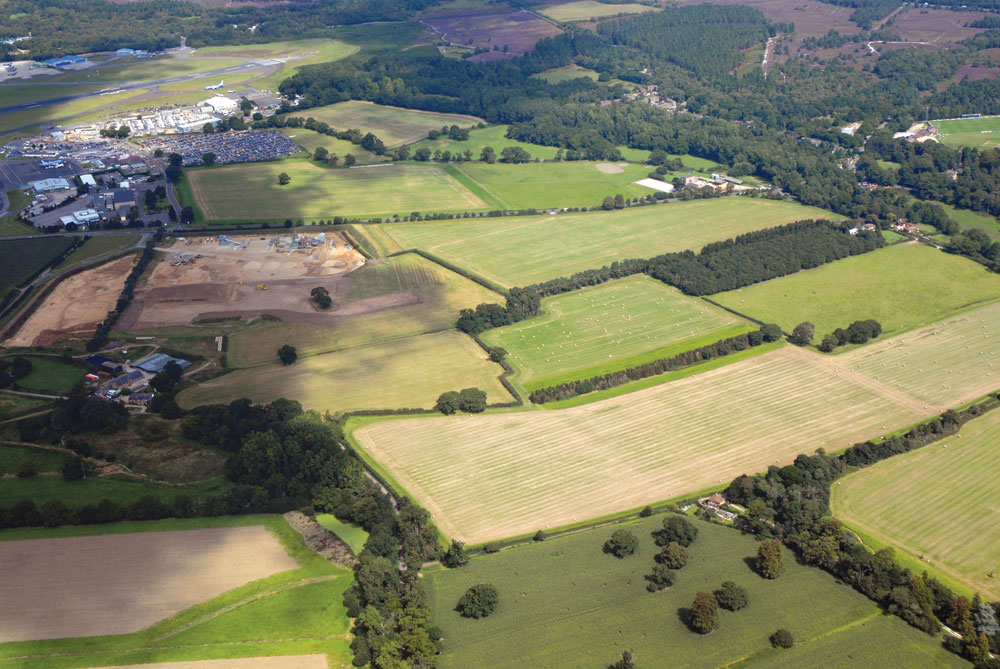
New Milton Sand and Ballast open new greenfield sand and gravel site adjacent to Bournemouth Airport
Since their foundation some 70 years ago, New Milton Sand and Ballast (NMSB) – a wholly owned subsidiary of H.H. & D.E. Drew Ltd – have established themselves as a relatively small but highly successful regional business providing high-quality aggregate, concrete and waste solutions to meet the demands of a particular niche market – namely the smaller builders, local tradesmen and householders in and around the southern counties of Hampshire and Dorset.
Based in the Hampshire town from which the business takes its trading name, NMSB are owned by joint managing director Michael Badcock (12%), the Drew Family Trust (39%) and Hanson Aggregates (49%), with the company’s board of directors comprising Mr Badcock and recently appointed joint managing director Trevor Poole, together with three members of the family trust and one representative from Hanson. This management structure allows the company to operate as a wholly independent organization but with the security of a ‘big company’ umbrella, although Hanson have no controlling interest in the day-to-day management and operation of the business.
Today the company has a turnover of around £14 million, employs over 90 staff and has various operations extending from Wareham in the west to Lymington in the east. These include: four sand and gravel extraction sites, two of which are equipped with washing plants; one bagging plant; two ready-mixed concrete plants and a mini-mix business; a sand quarry joint venture in Dorset; one waste recycling site; and three waste-transfer/collect aggregates depots with associated skip and muckaway services. NMSB are also looking to expand their washed secondary aggregates and small-load merchanting activities, and have recently acquired Steve Perrins Supplies Ltd, the Ringwood-based building supplies business.
The latest NMSB extraction and processing operation to come on stream is a £4.5 million development on a 185-acre greenfield site at Hurn Court Farm, adjacent to Bournemouth Airport. Owing to the height of the local water table and the potential for standing water, the current planning consent allows for the extraction of 1.8 million tonnes from total proven reserves of around 2.2 million tonnes. This means that some 1.5m of the 4m thick sand and gravel deposit will have to be left in the ground, as the site’s close proximity to the airport prohibits the presence of large open water bodies, balancing ponds, silt lagoons etc, which could attract flocks of migrating birds. NMSB plan to work the site at a rate of 140,000 tonnes per annum over a 12-year period, with a rolling restoration scheme being used to replace carefully preserved topsoils and subsoils to return the land back to agriculture, albeit at a slightly lower elevation than before.
The first phase of development at the site involved the relocation of an existing road to create suitable access to the site, the re-routing of a high-pressure gas main and road junction works to an airport entrance adjacent to the site. This was followed by the installation of a 150 tonnes/h sand and gravel washing/processing plant, supplied and installed by Co. Tyrone-based CDE Ltd and commissioned in May 2007. Once again, proximity to the airport imposed certain restrictions, with a maximum permitted height of 10m for the processing plant structure and a 7m height limit for product stockpiles. The plant itself produces two grades of washed sand and features two separate coarse product lines, one producing a range of washed and graded natural ‘shingle’ products, which are particularly suitable for decorative purposes, and the second producing washed and crushed 20mm and 10mm aggregates suitable for use in concrete production.
Sand and gravel plant
The new plant encompasses CDE’s full range of equipment, including a feed hopper, a number of models from the company’s ProGrade screen range, a RotoMax log-washer, an EvoWash multi-sands plant, an AquaCycle high-rate thickener, together with an Ore Sizer VSI crusher and Klein belt press, as well as several transfer conveyors of various specifications.
A raised access ramp allows mobile plant to feed the raw material (comprising approximately 48% sand and 52% gravel) into the processing plant’s 35-tonne capacity feed hopper, which discharges on to a 25m inclined transfer conveyor. This, in turn, feeds the material on to the first of the CDE ProGrade screens, a 5.0m x 1.8m double-deck rinsing unit that offers the maximum open area to ensure the highest possible tonnage over the screen, while also increasing the unit’s dewatering capability.
Approximately 10 tonnes/h of +60mm oversize is rejected by the top deck of the screen and discharged to an adjacent oversize bay, while the sand from the feed material (approximately 60 tonnes/h) is washed through the bottom deck of the rinsing screen and piped to the EvoWash multi-sands plant. Meanwhile, the –60mm +5mm material (approximately 80 tonnes/h) is fed into an 82/7 RotoMax log-washer equipped with long-life chrome molybdenum blades for reduced wear. The entire plant uses 35m3 of water per day, most of which is recycled, with any top-up required being supplied by an on-site borehole.
Scrubbed material from the log-washer is discharged from the front of the unit on to the second ProGrade screen, this time a 3.0m x 1.5m double-deck rinsing unit, while the waste water from the rear of the log-washer is piped to the EvoWash multi-sands plant.
From this point on the plant splits into two separate lines, one for natural (uncrushed) shingle suitable for decorative purposes, and the other for crushed aggregate suitable for use in concrete. The –60mm +24mm oversize discharged from the top deck of the second rinsing screen (approximately 25 tonnes/h) is conveyed to the crushing station, while the –24mm +6mm (approximately 50 tonnes/h) passes over the bottom deck and is conveyed to the natural screening station. Any remaining sand is washed through the bottom deck and fed to a ground sump. From here a vertical Warman pump is used to pump the sand and water slurry to the EvoWash plant.
The natural screening station, which is fed by a 25m inclined transfer conveyor, consists of a 3.0m x 1.2m double-deck horizontal HR screen, a 6m transfer conveyor and another 2.4m x 1.2m single-deck horizontal ProGrade screen, all fixed to a metal structure mounted on concrete walls that form a series of stockpile bays. The 6mm product passes through the bottom deck of the first screen and drops into a bay directly below, while the –10mm +6mm product passes over the bottom deck and is discharged into the adjacent bay. The +10mm material that passes over the top deck is fed on to the short transfer conveyor and discharged on to the single-deck horizontal screen. This separates the 14mm and 20mm products, which are deposited into their respective bays.
Meanwhile, the –60mm +24mm oversize from the second ProGrade screen is conveyed to the crusher station, which comprises a 6-tonne capacity surge bin mounted above an Ore Sizer OM50 vertical-shaft impact crusher. An ultrasonic level probe located within the surge bin controls a vibrating feeder to ensure a constant feed to the crusher, which has a throughput capacity of 40–50 tonnes/h. The crushed product from the OM50 is conveyed to the crushed product screening station via a 24m inclined transfer conveyor.
This transfer conveyor feeds on to a 4.0m x 1.5m triple-deck ProGrade rinsing screen, whereupon any oversize passes over the top deck and on to a transfer conveyor for discharge into an end bay, while 20mm and 10mm crushed products pass over the middle and bottom decks, respectively, and are discharged into separate bays below. The –5mm material and wash water is piped into a sump; from here a Warman 6/4 pump transfers the slurry to the EvoWash plant.
The EvoWash multi-sands plant, which allows NMSB to define the required cut points, processes approximately 70 tonnes/h (60 tonnes/h from the first screen and 10 tonnes/h from the other screens) of sand containing fragments of wood and lignite. The EvoWash process utilizes a series of cyclones, upward-flow classification tanks, sieve bends and dewatering screens to maximize the quantity of sand produced, while eliminating the contaminants and reducing the loss of fines. The end result is two clean sand products – a washed concrete sand and a washed building (plastering) sand, both with a moisture content of around 12% – together with a lignite-contaminated ‘waste’ sand.
Meanwhile, owing to the prohibition on settlement ponds at Hurn Court Farm, a water-treatment plant and belt press are used to deal with the waste water and fines. The –63 micron slurry discharged from the EvoWash multi-sands plant (approximately 400m3/h) is piped into an 8m diameter AquaCycle high-rate thickener tank, into which both cationic and anionic polyelectrolyte solutions are dosed to help settle the solids, while the clean water overflow is recycled back to the site’s main storage tank for recirculation and reuse.
The sludge produced by the thickener tank is pumped into a 60m3 buffer tank located beneath a 2.5m wide Klein belt press, which is housed in a fully clad building, together with the flocculant mixing and dosing equipment. The press is fed using a 6in seepex pump, with the sludge being dosed with both anionic and cationic polyelectrolytes, to aid the dewatering process in the belt press, before passing through two in-line mixers in the press feed pipe. The press discharges up to 12 tonnes/h of pressed filter cake, while the filtrate solution is recycled back to the washing plant via the AquaCycle high-rate thickener. After a period of natural drying, the waste filter cake is later returned to the land as part of the site’s restoration process.
Concrete plant
Hurn Court Farm is also the location of New Milton Sand and Ballast’s second and newest ready-mixed concrete plant. Supplied and installed by Co. Tyrone-based McCrory Engineering and commissioned in June 2007, the low-level plant features: two separate sets of in-line-feed bins, each with its own weigh belt; a covered feed conveyor; a gantry-mounted 4m3 capacity Pemat planetary mixer; two 50-tonne capacity cement silos; and a 30,000-litre water tank.
The plant has a nominal capacity of 60m3/h, but the twin feed lines cater for multi-batching, with one line weighing the next batch while the previous batch is being discharged, resulting in an actual capacity of around 80m3/h. Plant monitoring and control is via a Practicon control system, which works in conjunction with Weighsoft software to provide fully automatic operation with varying degrees of operator intervention as and when required. The plant is equipped with two discharge doors, one for transit mixers and the other suitable for smaller flat-bed vehicles. The plant’s steel support structure has also been designed so as to allow larger tipper wagons to back into position under both discharge doors for rapid loading of floor screeds.
NMSB have also invested in three DAF trucks featuring fully demountable and interchangeable 4m3 Hymix mixer units and 10.75-tonne capacity Wilcox Wilcolite tipper bodies. Offering greater delivery flexibility and improved truck utilization, these have already proved so successful and versatile that the company is planning to buy another three similarly equipped vehicles. The company also owns and operates its own 37m3 capacity bulk cement delivery tanker, which makes a particularly striking sight in its bright orange and white livery.
Main markets
The south coast towns of Poole and Bournemouth, which lie just to the south of Hurn Court Farm, provide the largest outlets for the site’s products. New Milton Sand and Ballast deliberately choose not to compete for major contracts in the region, instead preferring to focus attention on the sale of their ISO 9001-accredited bulk sands and gravels, decorative bagged aggregates, ready-mixed concrete and floor screeds direct to smaller end-users, trade customers, local builders and householders. As a result, much of site’s output is used in smaller building and renovation works, house extensions, garages, garden walls etc. This marketing strategy works particularly well for the company, helping to minimize the seasonal fluctuations in demand experienced by some of their larger competitors.
Despite their inclination to shy away from the region’s bigger jobs, one major contract on Hurn Court Farm’s doorstep that NMSB are hoping to win a share of is the redevelopment of Bournemouth Airport. Last year the airport was given the go-ahead for a £32 million expansion project involving the construction of a new arrivals hall and departure lounge, additional aircraft parking stands and extra car parking facilities to accommodate a predicted trebling of passenger numbers within the next 10 years. The redevelopment work is scheduled to take place over the next four to five years, and with the airport located, quite literally, just across the road from Hurn Court Farm, this opportunity is regarded by the company as one large job that really would be too good to miss.
Acknowledgement
The editor wishes to thank New Milton Sand and Ballast for permission to visit their Hurn Court Farm site and, in particular, Trevor Poole, joint managing director, for his help in preparing this article.