Hillhouse Quarry Revamp
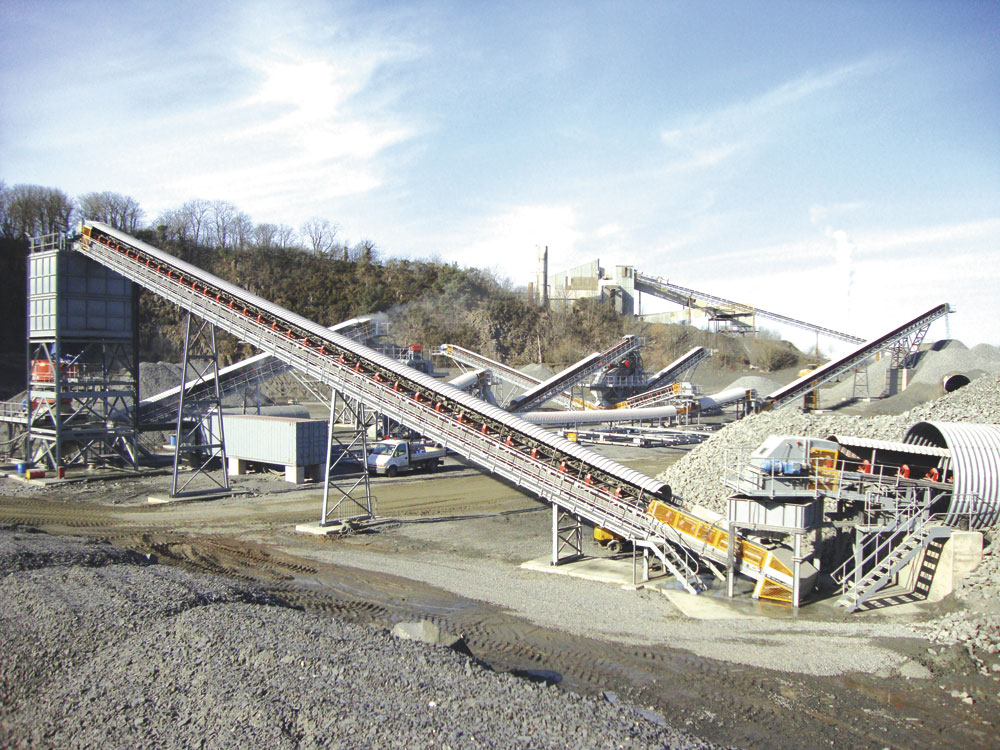
First phase of quarry upgrade delivers significant output and efficiency gains
Hillhouse Quarry Group Ltd are one of Scotland’s largest privately owned heavy building materials businesses, supplying drystone, coated stone and concrete products to markets throughout Central and Southern Scotland, particularly Ayrshire and Glasgow. The company was founded just over a century ago with the opening of Hillhouse Quarry, near Troon, and has remained in the Vernon family’s ownership ever since. Today the business employs around 200 people and comprises two hardstone quarries, three asphalt plants, a surfacing division, four ready-mixed concrete plants and a concrete blocks business, all in Ayrshire, together with precast concrete businesses in Beith and Inverness.
When Hillhouse Quarry first opened for business in 1907 the site was capable of producing 150 tonnes of whinstone (dolerite) a day using the techniques of the time, which included a rail track and wagon system for removing material from the face. In the decades since then, ongoing expansion of the quarry and investment in new plant and equipment has seen production increase to the point where today the site has the capacity to deliver around 1 million tonnes of drystone per annum, making it one of the largest privately owned hard rock quarries in Scotland. A significant proportion of the quarry’s output is used in house by on-site operations; the company’s three asphalt plants are all located at Hillhouse, along with one ready-mixed concrete plant and the company’s concrete block-making business. In addition, Hillhouse Quarry now has the capability to supply bagged aggregates and washed surface-dressing chippings, and recycling operations have also been developed in the past 12 months, giving the site a true one-stop-shop capability.
In spring 2009, a decision was taken to upgrade a section of the processing plant at Hillhouse Quarry as the first step in a proactive move to modernize and improve the efficiency of the entire plant. Despite its million tonnes per annum output, the plant was still struggling to meet the demand from internal and external customers when the markets were busy, due in part to an imbalance between the capacity of the primary crusher and the more limited capabilities of the rest of the processing plant, but also because of the age and condition of some of the equipment and the inefficient nature of the discrete bottoming plant used for Type 1 production, which was creating a production bottleneck.
Old operation
Previously, –300mm crushed material from the site’s Allis Chalmers 42/65 primary gyratory crusher was delivered by an inclined conveyor to a 10,000-tonne surge pile. Material reclaimed from this pile was carried by a single straight-line field conveyor and discharged on to an inclined feed conveyor to the main crusher building/screenhouse located on the rim of the quarry where secondary and tertiary crushing and final screening were carried out. A separate conveyor leg allowed material to be split off the field conveyor and diverted to the bottoming plant, which consisted of one Allis Chalmers 18/50 crusher, two Allis Chalmers 45in crushers, one double-deck and two triple-deck screens, together with associated motors, conveyors and feeders. With a maximum capacity of 100 tonnes/h, this bottoming plant had a total power draw of 571kW.
Today, thanks to a £2.5 million investment in a brand new secondary crushing and screening circuit, the old field conveyor and inefficient bottoming plant have both been rendered redundant and Hillhouse Quarry is now able to make Type 1 much more easily and efficiently, and at a much reduced cost. Moreover, the new plant not only achieves a power saving of 90kW over the old plant, but at the same time has also boosted the quarry’s Type 1 and single-size production capacity by 140 tonnes/h.
Preparations for the new processing section commenced in May 2009, the first task being the removal of an accumulation of waste fines, in some places up to 25ft thick, from the area where the new plant was to be situated. This area was cleared down to the underlying bedrock by an in-house earthworks team and then covered by a 1.8m deep layer of compacted fill material to provide an effective drainage layer. Substantial plant foundations comprising 1.2m deep concrete rafts were then laid down by Kilmarnock-based civil engineering contractors Kelburne Construction Ltd, using 757m3 of ready-mixed concrete from the quarry’s on-site batching plant.
Following a competitive tendering process, and based on the site management’s previous experiences working with the firm, the role of main contractor for the plant design, fabrication, assembly and construction work was awarded to Annan-based John Hope Engineering Ltd. Their experienced design team devised a well-ordered, high-specification static plant based around a Sandvik secondary cone crusher and two Sandvik screens. The entire plant is fully modular in design and, therefore, easy to dismantle and transport elsewhere should the need ever arise. Construction proper commenced in August 2009 and continued through to Christmas, and at the time of writing the plant was undergoing final commissioning and installation of the crusher and screenhouse buildings, with completion scheduled for the end of April 2010.
New operation
Output from the quarry’s existing standalone primary crusher is now delivered on to a new 66m long x 1,000mm wide inclined feed conveyor, which reaches a discharge height of 15.5m and delivers the –300mm crushed material on to a slightly repositioned surge pile. Material is recovered from this new 10,000-tonne pile by two 500 tonnes/h Rotex feeders mounted within a 3.8m diameter reclaim tunnel built from corrugated steel sections supplied by Asset International Structured Solutions. The feeders discharge on to a primary tunnel reclaim belt, which, in turn, feeds a 45.7m long x 1,000mm wide inclined conveyor that discharges into a 100-tonne live-capacity feed hopper mounted above the new secondary crusher. To help minimize the abrasive effects of the harsh whinstone, material flow from the reclaim conveyor to the feed boot of the inclined conveyor takes place via a robust transfer box arrangement, rather than a chute. For similar reasons, all three conveyors in this first section of the new plant are fitted with high-specification, abrasion-resistant Dunlop UsFlex belting, supplied by Rema Tip Top.
Mounted on a modular stacking frame that was specially designed by John Hope Engineering for rapid erection on site, the crusher feed hopper is equipped with a 500 tonnes/h Rotex feeder which choke feeds the new Sandvik CS660 secondary cone crusher. Once plant construction is completed, the crusher itself will be fully enclosed within a free-standing building featuring an easily removable roof section complete with all-round walkways and handrails – another innovative yet simple feature devised by John Hope Engineering to allow safe and easy access to the crusher for servicing and maintenance purposes.
The –75mm product from the secondary crusher discharges on to a 30m long x 1,000mm wide inclined conveyor which feeds a single-deck Sandvik MSO 2460S inclined screen. Fitted with tensioned rubber mats and featuring a circular stroke in the centre of the screen and an elliptical stroke at the feed end for more accurate screening, this machine effectively does all the work of the former bottoming plant by taking out the –40mm Type 1 material, which can be discharged to a ground stockpile via a 30m long x 800mm wide inclined stockpile conveyor or sent forward to a second screen for further processing. Meanwhile, the –75mm+30mm oversize rejected by this first screen is sent to a new secondary surge pile via a 45m long ground conveyor and 51m long inclined conveyor arrangement, both fitted with 900mm wide belts. These, along with all the other belts used throughout the new plant, with the exception of those on the first three conveyors, were supplied by Glasgow-based Strathcona Conveyors Ltd.
When production requirements dictate, the –40mm Type 1 material from the first screen is redirected to the second screen, a double-deck Sandvik MSO 2160D inclined screen, again fitted with tensioned rubber mats, which produces two final products (–20mm+5mm and 0-5mm dust). These are discharged to ground stockpiles via two 650mm wide stockpile conveyors, while any –30mm+20mm rejected by the screen is transferred across, via a short link conveyor, to the previously mentioned oversize conveyor for delivery to the secondary surge pile.
Recovery of the –75mm material from the secondary stockpile is achieved by means of two 300 tonnes/h Rotex feeders mounted within a new secondary reclaim tunnel of similar design and construction to the primary tunnel. The feeders discharge on to a 900mm wide reclaim belt which, in turn, feeds on to the last new conveyor in the upgraded section of the plant. This final 49.5m long x 900mm wide gently inclined conveyor, which is equipped with a material re-feed hopper at its tail end, discharges on to the quarry’s existing feed conveyor to the main crusher building/screenhouse on the rim of the quarry.
Throughout the new plant, John Hope Engineering have taken great care to incorporate high-specification components and ancillary equipment, including Siemens drive units, Cooper bearings on the head drives, RHP bearings, Gurtec rollers and belt scrapers from RH Services. Moreover, all of the conveyors are covered along their entire length to minimize dust emissions, and all head drives, tail end pulleys and feed boots are fully protected by integral powder-coated guarding designed for easy removal when maintenance is required. The provision of remote greasing lines and 110V power points at various locations around the plant also serves to assist routine maintenance work. Another key feature of the plant is that the three buildings housing the new crusher and the two screens are all designed as free-standing fabrications and are not attached to the crusher/screen support structures in any way, thus minimizing vibration transmission and reducing maintenance.
The electrics and control system for the new plant were supplied by Livingston-based Electromech Industrial Ltd. The fully automated plant control system allows dual control from either the primary crusher control cabin or the final screenhouse, thereby allowing material to be ‘pushed’ or ‘pulled’ through the system. A management information screen is also relayed to the quarry manager’s office with real-time data on plant performance levels.
Conclusion
The addition of the new CS660 secondary crusher has allowed Hillhouse Quarry to reconfigure the site’s existing Sandvik CH660 secondary crusher and four CH430 tertiary crushers, located in the main crusher building, as tertiary and quaternary units respectively. Whereas previously the old processing plant had a maximum total production capacity of 310 tonnes/h, comprising 100 tonnes/h through the bottoming plant and 210 tonnes/h through the old secondary and tertiary crushers, the newly upgraded plant has boosted total production capacity to 450 tonnes/h. Now, some 300 tonnes/h go to the final tertiary and quaternary crushers (90 tonnes/h more than was the case previously) with the balance of 150 tonnes/h comprising Type 1 or –20mm +5mm and –5mm (dust) production. Moreover, thanks to this significant increase in production capacity, Hillhouse are now able to run the plant for fewer hours than before, thereby generating energy savings and other cost benefits in terms of reduced man hours and fewer repair and maintenance issues. As an additional benefit of the new plant configuration, the three main sections of the plant (primary; secondary; and tertiary/quaternary stages) can be run independently if necessary, which was not possible before.
With sufficient reserves to last well in excess of 20 years at current levels of production, this recent upgrade at Hillhouse Quarry represents just the first stage in an ongoing and proactive programme to modernize and improve the entire operation, to ensure the site continues to meet future demands in the most sustainable, efficient and effective way possible. Future plans include refurbishment of the primary crusher, which is scheduled to take place later this year, followed in the medium to longer term by replacement of the final screens and product bins.
Acknowledgement
The editor wishes to thank Hillhouse Quarry Group Ltd for permission to visit the site and, in particular, Justin Gill, operations manager, Gary Jones, quarry manager, and John Hope of John Hope Engineering Ltd, for their help in preparing this report.