Goodnight Lignite
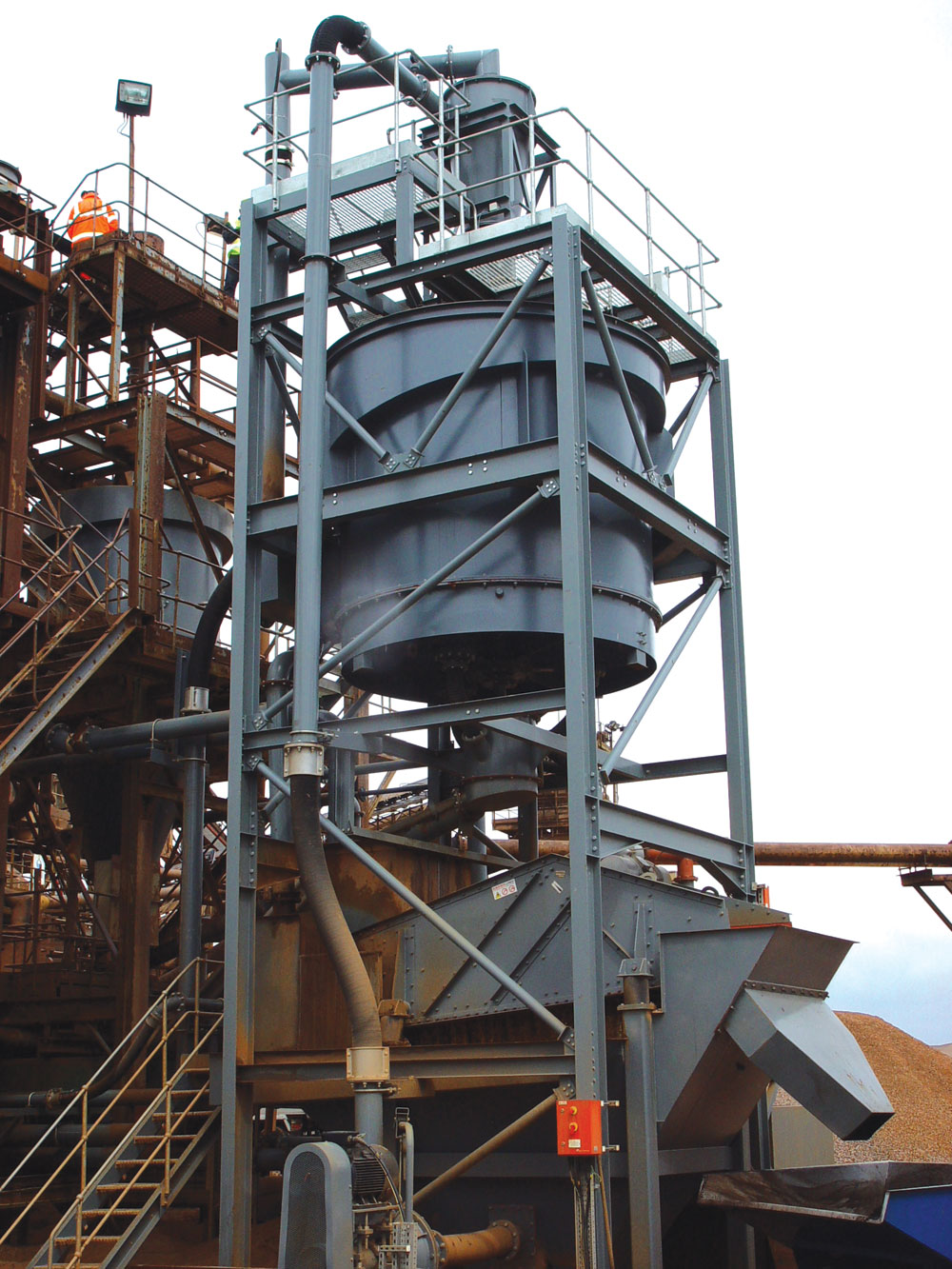
New computer-controlled Linatex sand plant solves lignite problem at Hanson’s Barton Quarry
Hanson UK’s Barton Quarry is a large sand and gravel site situated alongside the river Trent, some two miles south-west of the famous brewing town of Burton upon Trent, in east Staffordshire. The quarry was first established in the early 1970s and, when operating at full capacity, produces around 750,000 tonnes of sand and gravel annually – comprising a range of 20mm, 10mm and 6mm concrete aggregates, as well as a tile sand (a concrete sand that has had its top end taken out by re-screening) – for major customers such as Marley and CEMEX Roof Tiles.
Processing operations at Barton are handled by the site’s 220 tonnes/h capacity main gravel-washing plant and an associated sand plant, which was originally built by Linatex in the early 1990s to produce 150 tonnes/h of concrete sand. At this time the sand plant comprised a pair of T-type classifiers fed by 624 hydrocyclones, together with overflow sieve bends, a C-type fines classifier and a tower-mounted 1048 stockpiling sand separator. Subsequently, a fine tile-sand screening, dewatering and stockpiling plant was added adjacent to the T-type module, to produce a high-value secondary product from any excess fine material. This operation was later mothballed and remains so today.
Since the quarry was first established, an ongoing issue for the site operator has been the presence of significant amounts of coarse (>1mm) and fine lignite in the raw sand and gravel, which, if left unchecked, would have a detrimental impact on the final quality of the tile sand. During the 1990s, the industry standards of the day meant that sieve bends, in combination with a C-type classifier downstream, were able to produce an acceptably contaminant-free end product. However, with the building industry demanding ever higher sand quality, last year Linatex were invited to tender for, and were subsequently awarded, a project to re-engineer and recommission the existing sand plant to meet today’s more rigorous standards for lignite removal.
The end result is sand-classification and lignite-removal system designed to produce a single-grade, high-quality concrete tile sand with a ‘guaranteed’ lignite content of less than 0.04% (average) by weight. This necessitated the retrofitting of additional process equipment, including new slurry pumps, replacement T-type classifiers, a new sizing screen, a dense-medium separator (DMS) module and a new computerized classification control system, together with a radio-controlled stockpiling swivel chute. Phase 1 of the project, which included the renewal of the T-type classifiers and preparations for the subsequent phase, was completed in May 2008. Phase 2, which included the DMS plant installation and final commissioning, was concluded in June 2008.
Process description
Like the previous plant, the newly configured version is designed to process up to 150 tonnes/h of –5mm material, but now the old sieve bends have been decommissioned and replaced by a 1mm aperture sizing screen operating in conjunction with the state-of-the-art Linatex DMS system to handle contaminant removal.
The feed material, having already been screened to –5mm, is first pumped to a pair of hydrocyclones, which are fed by a common distribution box. Each of the two subsequent T-types is configured to perform (approximately) a 400µm cut on 75 tonnes/h of the feed. The underflow from the T-types is reunited within a feed regulating sump in readiness for transfer to the sand stockpiling tower together with the overflow after its passage through the DMS lignite-removal module.
Conditions within the T-type classifiers mean that all low-density (SG <1.6) contamination is discharged – along with the –400µm sand – in the overflow launder and directed to the DMS module where the coarse (+1mm) lignite is first screened off and discharged directly into a mini-skip for removal from the plant.
A feed-regulating under-pan located beneath the coarse lignite screen allows all the –400µm sand to be collected and pumped to a sand separator from where it is discharged, in a dewatered condition, directly into the DMS for removal of the remaining (fine) lignite and any other small-particle, low-density contamination.
Within the DMS unit a deep bed of fine sand creates conditions through which low-density particles cannot pass. A gentle up-current maintains the bed in a heavy, non-turbulent but fluidized state, while the computerized DMS control algorithm closely controls the underflow discharge valves such that all the fine lignite – but very little, if any, fine sand – is returned via the DMS overflow to the effluent-management system.
Fine sand leaving the DMS underflow collector box rejoins the coarse fraction from the T-type classifier underflows and together they are pumped to the stockpiling tower where a sand separator removes most of the water, rendering the end product suitable for stockpiling directly.
Beneath the stockpiling tower separator are three discharge chutes which are fed selectively by means of a Linatex radio-controlled swivel chute. This is powered by 12V DC electric motor which derives its total energy requirement from a wind-driven vertical turbine mounted at the top of the tower. The swivel chute is operated remotely from the main plant control room using a hand-held transmitter, providing a welcome and safer alternative for the plant operatives, who no longer have to routinely climb up the tower to effect a chute changeover.
All items of equipment subject to wear through wet abrasion (pipelines, hoses, chutes etc) are protected with Linatex natural rubber. Wear life has been further enhanced through the use of minimal moving parts throughout the plant.
Start/stop control of the sand plant’s pump and screen motors is incorporated within the main SCADA-based Batching & Blending start/stop control system for the gravel plant that feeds it, although the Linatex PLC control system independently supervises the sand-classification and lignite-removal processes. The Linatex system includes a touch-screen a human/machine interface (HMI), situated local to the sand plant, and provides continuous parametric data-logging, giving a four-month rolling record of plant operation, as well an automated interface signal to invoke a material feed stoppage upon any one of a number of configurable alarm conditions.
Charles Grocott, commercial support group manager with Linatex, said: ‘It’s very easy to change the set points on the plant, but generally we don’t need to. Once the system is set up and running correctly, it effectively defaults to success – there is no need to tweak it on a regular basis.’
Results in service
Since final commissioning, the newly enhanced and refurbished plant has been producing consistently high-quality, lignite-free, premium-grade concrete tile sand with complete reliability. Although the plant is guaranteed to produce a clean sand containing less than 0.04% lignite by weight, actual samples taken have been found to contain as little as 0.01%.
As a potential bonus for Hanson, the system also produces a very clean waste lignite product at a rate of about one mini-skip load every one or two days. Owing to its high calorific value, this is currently being stockpiled on site and, at some time in the future, may be used as a supplementary fuel source in Hanson cement plants.
Commenting on the new sand plant’s performance to date, Barton Quarry manager Peter Luker said: ‘The old sieve bends used to take out the coarse lignite but not the finer grains. Now the sand is far cleaner than it has ever been, and we have full confidence that it will be like that every day.
‘In addition, the superior performance of the sizing screen/DMS combination over the previously used sieve bends has yielded a marked reduction in the loss of fine sand with the effluent return water. The tiny amount that necessarily goes over the weir on the DMS is nothing compared to what we used to loose through the sieve bends.
‘It really is an impressive piece of kit that does exactly what it is supposed to do, and Linatex’s training and support has been second to none.’
Acknowledgement
The editor wishes to thank Hanson UK for permission to visit Barton Quarry and, in particular, Peter Luker, quarry manager, and Steve Slingo and Charles Grocott of Linatex Ltd, for their help in preparing this article.