Glendinning Complete Major Quarry Upgrade
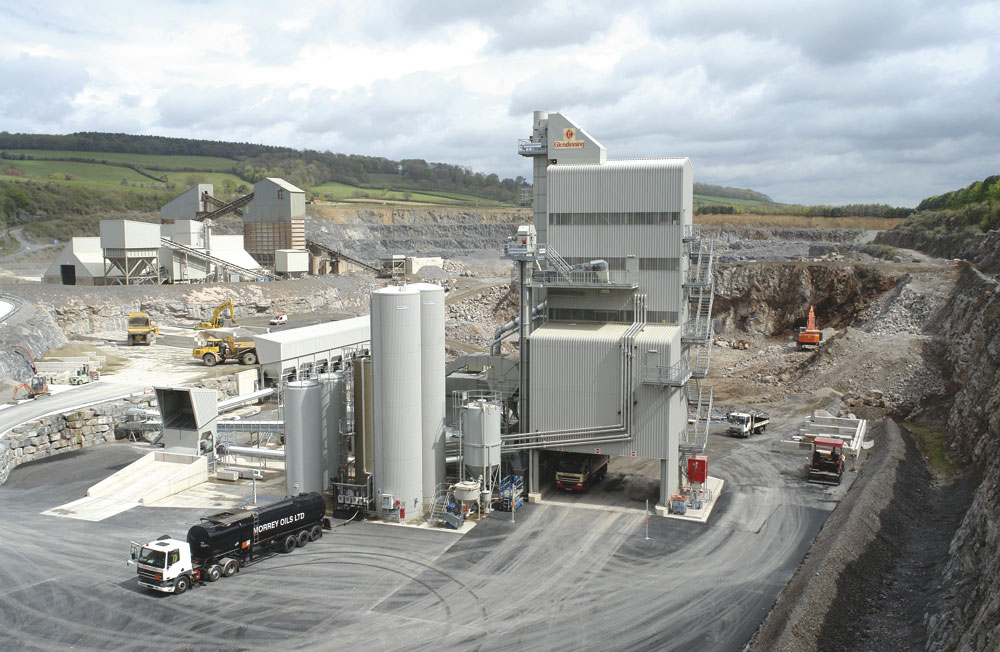
New Benninghoven asphalt plant for Linhay Hill Quarry
Glendinning, the West Country’s largest independent quarry operators, have completed phase 1 of a major upgrade at their Linhay Hill Quarry, at Ashburton, in Devon. The quarry lies on the south-eastern edge of Dartmoor, within close proximity to the main A38 trunk road running through Devon and Cornwall.
The limestone quarried at the site is late-Devonian in age, some 360–380 million years old, and is characterized by its fine-grained medium to dark grey colouring. Linhay Hill produces over 500,000 tonnes of this limestone annually, with products ranging from aggregates, coated stone and ready-mixed concrete to building blocks, decorative and industrial paving and hardcore, agricultural lime and walling stone.
Major investment in a new state-of-the-art asphalt plant from Benninghoven was part of an £8 million upgrade of the existing asphalt and crushing and screening plants, to increase operating efficiency and realign output with changing market requirements.
Commenting on the new plant and its selection, operations director Ian Glendinning said: ‘The project team, who actively involved employees from all aspects of the business, spent a great deal of time and effort evaluating the options shortlisted to ensure the plant selected provided us with the required flexibility and performance criteria. It was also vital that we gained the necessary assurance from the manufacturer with regard to build quality, delivery and erection time-scales, after-sales support and, most importantly, their approach to, and focus, on health and safety.’
Designed to provide significant operational benefits and cost savings, the new Benninghoven model TBA3000UE plant is able to produce a wide range of high-specification coated materials, including modern thin-surfacing stone-mastic asphalts and other specialized mixes. The plant is rated to produce 200 tonnes/h at 3% initial moisture (DBM) and 160 tonnes/h at 5% initial moisture (SMA).
The aggregate cold feed consists of an in-line set of eight bins with belt feeders, discharging on to a 6.5m collecting conveyor, which, in turn, feeds on to a 30m inclined conveyor. The fully covered inclined conveyor is mounted on trestles with safety pull wires along its walkways. An 18m long x 800mm wide transfer conveyor transports material on to a short reversible slinger conveyor, which feeds materials directly into the dryer.
The aggregate dryer drum, which measures 2.4m in diameter x 9m in length, is fully lagged with 70mm thick insulation and aluminium clad for heat retention and noise reduction. The drum is friction driven by four support rollers through individual 18.5kW geared motor units.
The burner is a Benninghoven model Rax Jet oil 4-3 OFU type, designed to burn both gas oil and Eco oil. This is equipped with a full range of operating and safety devices to deliver high-efficiency fuel usage. An air-inlet silencer is connected to the burner to suppress noise levels. The burner and silencer are mounted on a track to allow the unit to slide back from the dryer for routine servicing.
The plant’s dust collection system, which is rated at 64,000Nm3/h, is sized for the dryer and mixing section scavenging, and achieves emission levels of less than 20mg/m3. A primary skimmer unit mounted alongside the dryer separates any coarse dust from the airstream, which passes to the hot-stone elevator feed boot via a gravity flap valve and chute. The secondary cassette-type filter system collects any remaining dust and transfers it, via two screw conveyors, to the filler elevator. A dust monitor mounted on the exhaust stack provides a remote readout in the operator’s cabin. As a result, the plant meets the most stringent dust control regulations.
Any excess dust collected can be discharged from the reclaimed dust silo through a rotary valve into a twin-shaft paddle conditioner, where water is introduced to provide an environmentally friendly method of purging the dust. Any excess filler can also be directly loaded into road tankers.
Hot aggregates are transported from the dryer up to the screen by a 28m vertical bucket-type elevator. This is totally enclosed and features a heavy-duty double-strand chain and wear-resistant steel buckets with replaceable liner plates at impact points. Elevator drive is by a 37kW geared motor and toothed chain wheels at the elevator head. The elevator features externally located bearings and a safety backstop facility. A wide platform provides access for maintenance.
Material discharged from the elevator passes into a six-deck screen featuring twin-shaft drive via two19kW ‘bolt on’ low-maintenance vibrating motors. These drive units are mounted outside the screen housing to allow the high-temperature screening of materials. Wide access doors, together with a rollaway chute, provide access to all screen decks. An extraction fan ensures negative pressure is maintained in the screen housing for optimum dust control.
The hot storage section has a total capacity of 80 tonnes and comprises six bins. All the bins are insulated and clad and each is fitted with continuous level indicators and an overflow chute. Discharge is by a pneumatically operated radial door, which accurately regulates material flow to the aggregate weigh hopper, from where the aggregates are discharged directly into the mixer.
Accurate weighing out of ingredients is achieved by separate load-cell-mounted weigh hoppers, which comprise a 3,000kg capacity aggregate hopper, 600kg filler weigh hopper, and 350-litre capacity weigh vessel for bitumen. Mixing takes place in an insulated 3,000kg capacity twin-shaft paddle mixer, with drive provided by two 37kW geared motor units through synchronized gears. A radiation pyrometer is situated at the mixer discharge to indicate mix temperature.
Mixed material discharged from the mixer falls into a 3,000kg skip unit, which runs on horizontal tracks and distributes the material into a 200-tonne capacity silo, arranged in four 50-tonne compartments. All four compartments are equipped with high-level warning indicators and are insulated and fitted with electric trace heating around the discharge doors. A 6-tonne direct load-out hopper is positioned beneath the mixer. All bins are mounted on load-cells to ensure accurate material loading.
Bitumen is stored in two vertical tanks (70m3 and 100m3 capacity) located adjacent to the plant, both of which are Benninghoven’s latest electric high thermal efficiency units that deliver low running costs due to their stepped heating system design. An in-built loading system with high-level probes offers fail-safe filling with no possibility of spillage and ensures compliance with the latest RBA standards.
Filler is stored in an external two-compartment vertical silo holding approximately 60m3 of reclaimed filler and 40m3 of imported material. Both silos are equipped with level indicators and shut-off valves.
A gravimetric additive system is also incorporated within the plant to feed granulated material from a 30m3 silo. Each batch of granulate is accurately weighed in a load-cell-mounted weigh hopper before being discharged through a butterfly valve to the mixer. A 3m3 silo for pigment, which is filled from bags, is situated alongside.
A RAP system has been incorporated in the facility to deliver precise percentages directly into the plant mixer. The system comprises a steep-sided, 10m3 capacity feed hopper fitted with an oversize grid and two vibrators. A 4kW belt feeder mounted beneath the hopper discharges the RAP on to a 30m long covered conveyor equipped with a belt weigher to give accurate batches proportional to the weight of aggregates. The RAP is transported up to the mixer level via a recycling elevator. An automatic vent duct at the mixer allows rapid extraction of steam during recycling operations.
The plant is controlled by a Benninghoven Online Batcher 3000 computer system that displays all plant functions via colour graphics. The system, which is housed in an existing control cabin adjacent to the plant, is modem linked and provides storage for up to 500 asphalt mix recipes.
Acknowledgements
Thanks are due to Ian Glendinning, operations director; Barry Wilson, managing director; and Richard Webb, operations manager, of E&JW Glendinning; as well as Nigel Moreton of Benninghoven UK Ltd, for their help in preparing this report.